Vous avez géré avec succès la partie matérielle de votre activité : les entrées/sorties de stocks, les composants et les produits finis avec les nomenclatures, la planification des OA et des OF. Maintenant, descendons dans l’atelier. Nous allons mettre en œuvre cette logistique sur le terrain avec votre équipe et vos machines.
Analysez vos processus de fabrication
Tout d’abord, vous devez avoir une vision globale de votre atelier (plan de masse), de vos implantations (topologie), de vos flux (analyses cinétiques) et du déroulement des opérations. Prenez de la hauteur. Observez bien :
Quels sont les cycles avec valeur ajoutée (ce que le client achète) ?
Quels sont les cycles sans valeur ajoutée nécessaires à la production mais que vous jugez pénalisants à cause de :
temps de changement d’outils trop long et aléatoire ?
temps de mise au mille (réglages au démarrage) variable ?
Quels sont les cycles sans valeur ajoutée qu'il faut éliminer pour cause de :
manutention ?
recherche d’informations ?
erreur de procédure qualité ?
erreur d’approvisionnement ?
attente de décision ?
stockage d’en-cours de fabrication + manipulations de stockage/déstockage ?
Ces 3 questions sont schématisées ci-dessous :
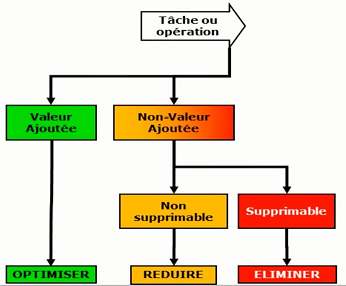
Vous pouvez consulter cette vidéo pour plus d’informations.
Vous l’avez compris, avant de lancer vos productions il faut maîtriser votre territoire, c’est à dire :
connaître votre zone de travail ;
identifier vos ressources.
Nous sommes dans une démarche lean manufacturing (pour approfondir le sujet, je vous invite à suivre le cours de Cédric Facon sur l’Amélioration continue). Nous allons aborder quelques outils de base d’organisation.
Comment est configuré votre processus de fabrication ? Quelles sont les causes de gaspillages ? Peut-on l’améliorer ?
Implantation traditionnelle de type atelier
Dans ce type d’implantation, votre usine est découpée en ateliers spécialisés et homogènes.
Exemple : fabrication de 3 modèles de vélos : “acier, “alu”, “titane” dans 8 ateliers (en jaune). Chacun possède une spécialité.
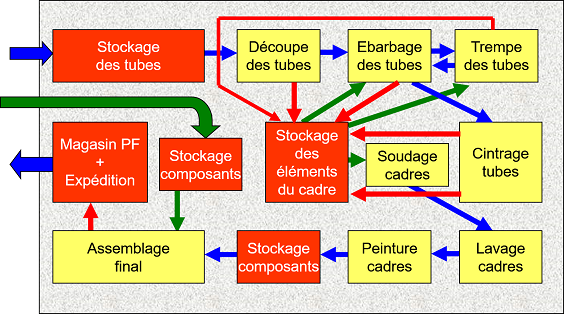
Les opérations de production sont lancées par lots, ce qui implique des “décumulations” de stock, puis des accumulations dans un autre stock. Ces stocks sont visibles dans chaque secteur. Le premier vélo sort quand le lot est terminé, c’est-à-dire longtemps après qu’il soit lui-même achevé. Des manutentions manuelles ou par chariots font la liaison entre les stocks. Résultat : un taux de non-valeur ajoutée élevé.
Implantation rationalisée en flux continu
Dans celle-ci, votre usine travaille non pas par spécialité, mais par gamme de produits. Chaque Unité Autonome de Production (UAP) produit une seule gamme de vélos. Les stocks ont disparu. L’acheminement est opéré vélo par vélo en chaîne de fabrication. La sortie du premier vélo est très rapide. Le risque de défauts est faible puisqu'une erreur à un poste est détectée immédiatement au poste suivant, ou en fin de ligne.
Cependant, il est nécessaire de créer 3 mini-usines avec les mêmes équipements.
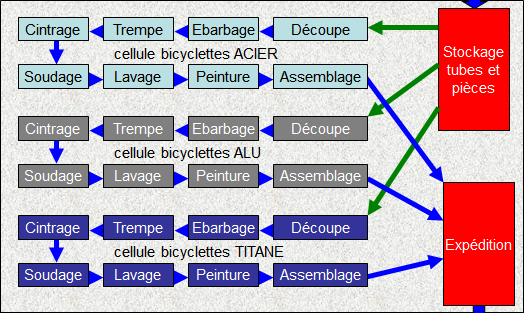
Regardons maintenant les déplacements dans nos usines.
Diagramme spaghetti
Le principe de ce diagramme est de :
tracer sur un plan d’atelier à l’échelle chaque aller et venue au cours d’un poste ;
spécifier par un trait de couleur les caractéristiques du déplacement : avec chariot, à pied, à vide, chargé X kg, chargé Y kg…
Exemple de poste de montage de miroir sur des meubles de salles de bain.
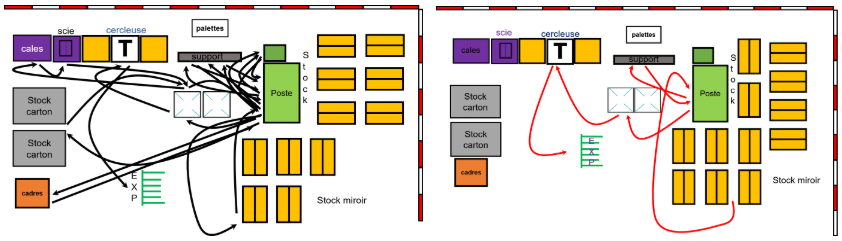
Les distances sont mesurées. Les charges sont calculées. Dans cet atelier, l’opérateur porte de 1 500 à 3 600 kg/mois. L’opérateur est seul à connaître ce poste. Il se plaint de maux de dos. En cas d’absence, la production est stoppée !
Après observations, questionnements, calculs, analyse et propositions, la solutions définitive suivante est adoptée :
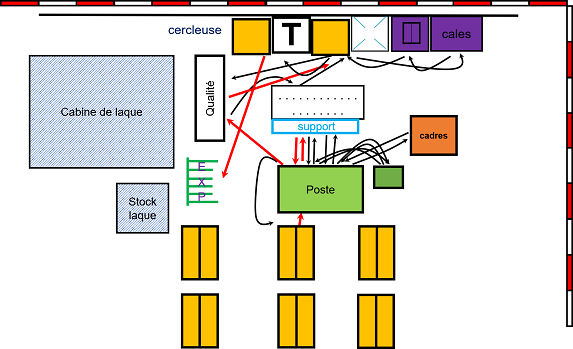
Elle propose de réduire les déplacements et les ports de charges grâce à une réimplantation complète de l’atelier. Les lourdes charges sont posées sur des chevalets à roulettes pour la manutention. Bilan : les distances de déplacements sont divisées par 2, de même que celles avec port de charges. La qualité s’est améliorée de 3% et le TRS de 5%.
Poursuivons dans l’observation plus dans le détail.
Analyse de déroulement
Comment se déroule un cycle de production ? Y a t-il un mode opératoire précis ? Y a t-il une variabilité de ce mode en fonction des opérateurs ? Que peut-on améliorer ?
Observer le poste c’est l’étudier, le critiquer et l’améliorer en utilisant des symboles standard :
symboles d'analyse du déroulement ;
symboles de flux et de destinations.
Cette analyse tracée au brouillon en observant le déroulement du procédé de fabrication permet d’obtenir un relevé rapide du mode opératoire réel d’un procédé de fabrication. Ce travail est proche du Genba pratiqué dans le Lean manufacturing (voir cours “Amélioration continue”).
Buts :
évaluer l’importance des opérations sans valeur ajoutée ;
prendre des décisions de type :
éliminer,
combiner,
permuter,
améliorer ;
relever le nouveau déroulement après modifications ;
évaluer les gains.
Symboles utilisés
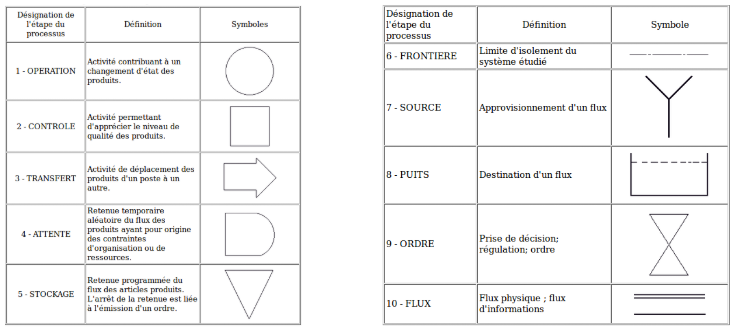
On distingue 2 états du déroulement du processus.
État stable : cette étape apporte une modification de la matière, attendue par le client.
État fugace : cette modification n’est conditionnée que par le processus.
Exemple : une passe d’ébauche en usinage est un état fugace. Une passe de finition est un état stable.
La manutention d’un stock vers un atelier est un état fugace. La manutention en juste-à-temps vers le client est un état stable. Pour un état stable, le symbole est noirci.
Exemple d’application
Prenons l’exemple du cycle du petit déjeuner. Grâce à cette méthode, nous pouvons le synthétiser de cette façon :
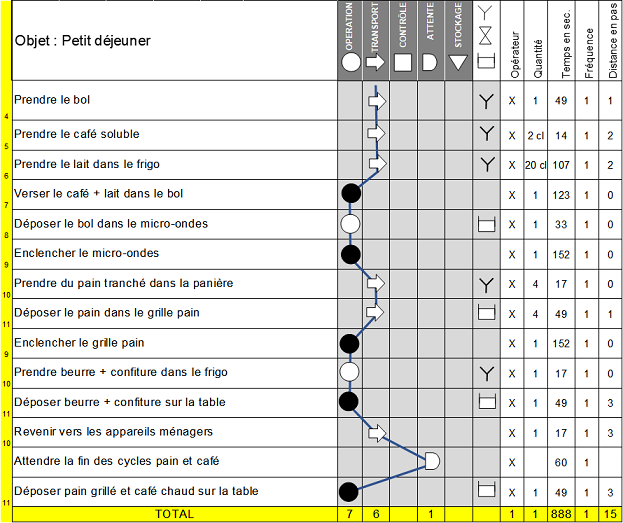
Ratio de tension
La production est créatrice de richesses grâce à la valeur ajoutée qu’elle produit. Il est naturel que l’on cherche un indicateur donnant la proportion de temps passé à cette transformation.
Pour cela, on calcule le temps de traversée (lead time) : temps entre l’entrée des matières dans le processus de fabrication jusqu’à leur sortie pour expédition. Le temps de valeur ajoutée est la somme des temps de transformation.
Le rapport :
Il est illustré par Cédric Facon dans son cours sur l’Amélioration continue. Partie II, quand on attend le rendez-vous d’un médecin avec des patients avant vous au secrétariat et dans la salle d’attente du médecin. Le ratio de tension est : 25 135 = 18,5 % .
Ce qui paraît peu, mais sans commune mesure avec les ratios industriels plus proches de 0,01 % !
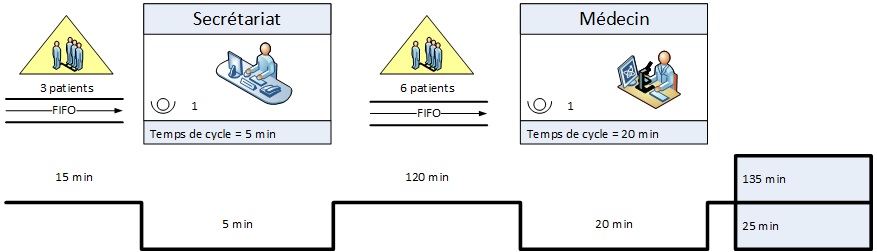
Créez une équipe performante
Une équipe performante est une équipe qui comprend les enjeux de son activité : opérateurs, chefs de secteurs, coordonnateurs de flux, magasiniers, manutentionnaires, techniciens, agents qualité : tous les partenaires directement en lien avec la production, les fournisseurs de service-support à la production.
Présentez tout d’abord à vos partenaires ce premier organigramme structurel vu en partie 1, puis les relations client-fournisseur en interne, leurs rôles, leurs responsabilités.
Les erreurs si fréquentes dans l’industrie ne sont pas dues à l’incompétence du personnel ou à leur volonté de saboter le travail. W. Edwards Deming constatait que dans 97 % des cas, les erreurs sont dues au système et non au personnel.
Il préconise, pour aller vers une qualité totale :
la formation et le développement professionnel : ce sont les clés de la réussite ;
à l’encadrement de créer une émulation dans l’équipe ;
de faire disparaître la “peur” : chacun doit se sentir libre de parler ;
de supprimer les obstacles à la fierté du travail : les efforts des employés doivent être valorisés.
Pour aller plus loin, vous pouvez consulter cette ressource sur les 14 points de Deming.
En tant que responsable, votre rôle est décisif. Soignez votre relationnel, en particulier la communication des faits (pas des opinions).
Pour cela, prévoyez un espace dédié et du temps, même si c’est 10 min par poste, où chacun peut prendre la parole. Favorisez la prise en charge des problèmes relevés. Établissez un roulement de pilotage de résolution de problème dans l’équipe.
Adaptez vos capacités à votre charge
Principal facteur de conflit au sein de personnel : la charge de travail, trop élevée, inégalitaire, pas assez lissée ! Une fois le CBN (calcul des besoins) terminé, la question est de savoir si la capacité de travail peut y faire face.
Définitions
Exemple : une équipe de 10 opérateurs doit produire 1000 pièces d’un temps unitaire de 0,05h (3mn) après un changement d’outil de 2h.
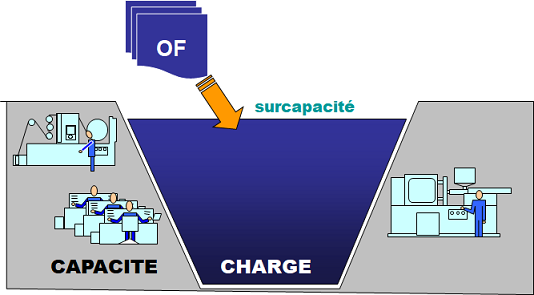
Capacité : volume d’heures de travail que peut fournir une équipe d’employés pendant une période donnée.
Nb de ressources x temps unitaire disponible :
Le temps unitaire disponible dépend de facteurs tels que :
taux d’allure entre employé accoutumé et nouveau venu ;
taux de performance des machines ;
taux de qualité de la production.
Charge : volume d’heures de travail affecté à une équipe sur une période donnée.
Quantité à produire x temps unitaire gamme + temps préparation
L’équipe est en surcapacité de :
Le temps unitaire gamme dépend de facteurs tels que :
méthode d’élaboration du temps : chronométrage, MTM (Method Time Measurement), observations instantanées.
Exemple de calcul d’effectif d’un atelier
Prenons l’exemple d’une chaîne d’assemblage de bicyclettes qui a une quantité à produire par mois de 8 400 unités.
temps unitaire Top = 0,42 h ;
temps de préparation Tp = 0 min ;
horaire : 8 h/j et 22 j/mois ;
taux de performance = 102 % ;
taux de marche = 85 % ;
taux d'absentéisme = 10 %.
Quel effectif faut-il dans cet atelier ?
Calcul de la charge mensuelle :
Calcul de la capacité réelle mensuelle par personne :
Effectif :
Calcul de performance d’une chaîne de fabrication
L’objectif de ce calcul est d’analyser l’équilibrage d’une chaîne de production et d’évaluer l’importance d’une perte d’équilibrage éventuelle. Nous y reviendrons dans la dernière partie, lorsque nous aborderons la gestion des postes “goulot d’étranglement”.
Données à collecter :
la charge hebdomadaire en pièces nb de produits finis (PF)/semaine ;
le temps opératoire par poste : Top ;
le temps opératoire le plus long de la chaîne : TM ;
le temps total de fabrication d'un PF : somme des Top ;
le temps de travail/poste : temps d'ouverture – temps de pause ;
le taux d'activité moyen/personne : taux de performance.
Objectifs de calculs :
le nombre de postes nécessaires sur la chaîne ;
le temps opératoire/poste : Top et Tm ;
la perte d'équilibrage en % de la chaîne.
Formules de calculs :
charge de l'atelier en heures : nb de PF x somme des Top ;
capacité de l'atelier en heures : temps de travail x taux d'activité moyen ;
nombre de postes, N : N = charge/capacité ;
temps opératoire moyen par pièce pour un poste : Tm = capacité/nb de pièces à produire ;
perte d'équilibrage de la chaîne : (N . TM - Somme Top)/N . TM.
Exemple
Prenons pour exemple ceci : nous devons concevoir une chaîne capable de produire 2 000 caméras/semaine.
Nous disposons des informations suivantes :
semaine de 40 h = 400 000 dmh (dix millième d’heure) ;
activité moyenne = 130 ;
somme des temps opératoires : Top = 1 843 dmh ;
Top d’un poste = 265 dmh.
Grâce à ces informations, nous pouvons en déduire les résultats ci-dessous :
Nombre de postes, N :
Temps opératoire moyen par poste, par caméra :
Recherche de l’équilibrage :
Tous les postes s'alignent sur le plus long Top, c’est-à-dire TM = 265 dmh, la cadence de sortie étant celle du poste “goulot”.
Perte d’équilibrage :
Cette perte moyenne peut être considérée comme négligeable.
Planifiez un plan de charge
Le calcul des besoins étant achevé, OF et OA sont prêts. La charge et la capacité sont connues. Vous souhaitez avoir un tableau de bord de votre plan de charge période par période (jour par jour…). En fonction de ce plan, vous procéderez au lissage de la charge ou de la capacité.
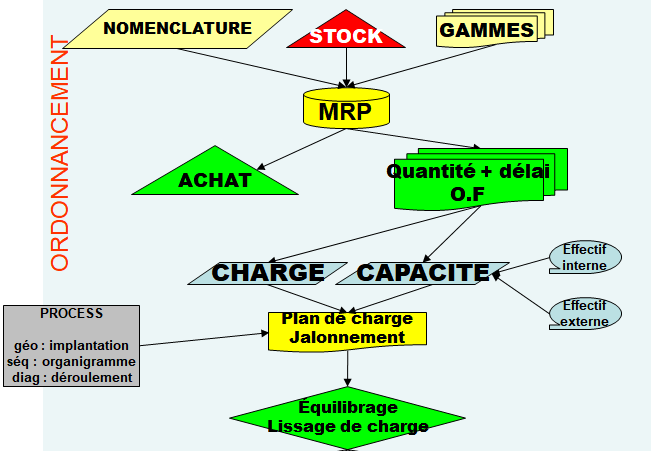
Mon exemple de lissage de charge est simple. L’objectif est la gestion des problématiques de déséquilibre entre charge et capacité.
Tableau de charge/capacité
Suite au calcul des besoins du MRP, vous renseignez les capacités calculées.
TABLEAU DE CHARGE / CAPACITÉ | ||||||
Jour n° | lundi | mardi | mercredi | jeudi | vendredi | samedi |
OF issus du CBN en nombre de pièces | 100 | 200 | 150 | 50 | 100 | 150 |
Temps unitaire en heures | 0,05 | 0,05 | 0,06 | 0,08 | 0,06 | 0,06 |
Temps de changement de série en heures | 2 | 2 | 0,5 | 0,5 | 1 | 0,5 |
CHARGE en heures | 7 | 12 | 9,5 | 4,5 | 7 | 9,5 |
CAPACITÉ en heures | 9 | 9 | 9 | 9 | 9 | 9 |
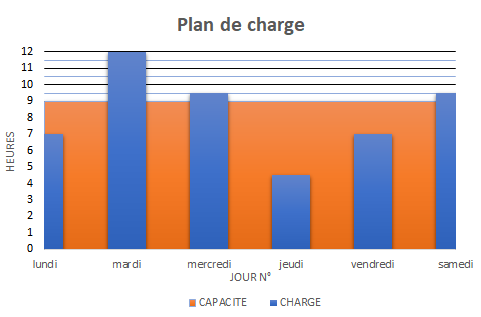
Techniques de lissage
TABLEAU DES DÉSÉQUILIBRES | ||||||
Jour n° | lundi | mardi | mercredi | jeudi | vendredi | samedi |
CHARGE en heures | 7 | 12 | 9,5 | 4,5 | 7 | 9,5 |
CAPACITÉ en heures | 9 | 9 | 9 | 9 | 9 | 9 |
DÉSÉQUILIBRES | -2 | +3 | +0.5 | -4.5 | -2 | +0.5 |
Vous constatez 3 surcharges dans la semaine : mardi, mercredi, samedi. Deux techniques sont utilisables pour procéder à l’équilibrage charge/capacité :
Lisser la charge.
Adapter la capacité.
1. Lissage de la charge
Option | Principe | Avantage | Inconvénient |
Lissage amont | Anticiper la production. Exemple : 2 heures de surcharge du mardi peuvent être anticipées le lundi. | Pour le client, c’est transparent | Coût de possession de stock |
Lissage aval | Retarder la production. Exemple : 3 heures de surcharge du mardi programmées le jeudi. | Pas de modification de la capacité de travail | Le retard peut être refusé ou sanctionné par le client |
2. Lissage de la capacité
Techniques classées de la plus court terme à la plus anticipée :
Option | Principe | Avantage | Inconvénient |
Heures supplémentaires | Augmenter le nombre d’heures ponctuellement | Réponse souple aux pics de charge | Ne peut pas être pratiqué à long terme |
Appel à l’intérim | Ajustement de la capacité par du personnel extérieur | Ajustement assez rapide | Coût élevé Méconnaissance du poste |
Sous-traitance | Externaliser la production | Pour le personnel, c’est transparent | Le fournisseur risque de s’approprier le marché |
Mise en place de 2x8 ou 3x8 ou SD | Ajustement par augmentation du personnel. Embauches. | Absorption des surcharges chroniques. | Nécessité de s’assurer de la durabilité du besoin |
Achat d’équipements supplémentaires | Ajustement par augmentation des ressources matérielles. Investissements | Absorption des surcharges chroniques. Équipements récents. Meilleures performances. | Anticiper sur le long terme Coût d’investissement |
3. Autres solutions de lissage
Il reste une troisième voie, celle de l’ingénieur-manager, plus longue à mettre en place mais pérenne. Elle concerne les 3 services créateurs de valeur ajoutée : production, maintenance, qualité.
Puisqu’il faut gagner du temps, l’objectif est de supprimer ou réduire les gaspillages de temps dont ces services ont la responsabilité :
production et qualité : surproduction, surstock, transports inutiles, traitements inutiles, mouvements inutiles, rebuts, temps d’attente. Ce sont les 7 gaspillages identifiés dans le Lean ;
maintenance : pannes, changement de série, microarrêts, sous-vitesse, rebuts, mise au mille. Ce sont les 6 causes de pertes identifiées par la TPM, “Total Productive Maintenance”.
Ces solutions sont de plus en plus primées par les entreprises car moins coûteuses, pérennes et génératrices d’un cercle vertueux de progrès grâce à un changement d’état d’esprit du personnel. De nouveaux services “Amélioration continue” se créent dans ce but depuis moins de 10 ans. Mais l’avancée est encore timide : 40 % des entreprises n’ont pas encore pris de décisions dans ce sens.
Nous verrons dans le prochain chapitre par quoi commencer.