Dans ce chapitre vous prendrez en main l’organisation de votre atelier. Vos documents de production sont prêts et à jour. Votre plan de charge est équilibré. Vos ressources humaines et matérielles sont disponibles.
Vous allez maintenant pouvoir choisir vos priorités et votre mode de jalonnement des opérations de production. Plusieurs choix s’offrent à vous. Je vous indique la meilleure voie pour piloter votre processus.
Préparez vos OF
Les OF, ordres de fabrication, sont la base des informations et consignes de production données aux opérateurs.
Bien entendu, tout oubli ou erreur entraîne des perturbations plus ou moins critiques. Vous devez consigner :
client :
nom, société, import/export,
classement ABC du client (exemple en CA) ;
planification :
date de début, date de fin prévisionnelles,
date de début, date de fin réelles ;
ressources humaines et techniques :
nom du ou des employés,
nom de l’équipement ;
ressources matérielles :
références matières premières, articles,
quantités prévisionnelles,
emplacements au magasin,
type de mise à disposition,
quantité redéposée en stock,
travaux,
désignation des tâches,
enchaînement des tâches,
temps alloué par tâche,
temps passé par tâche,
taille du lot de fabrication,
consignes qualité,
consignes sécurité,
EPI nécessaires ;
supports auxiliaires :
modes opératoires,
plans,
nomenclatures.
Cliquez ici pour voir un exemple d’OF d’une PME de peinture industrielle. Une fois rempli informatiquement, cet OF permet de calculer facilement le coût de revient de la production.
Choisissez votre technique de jalonnement
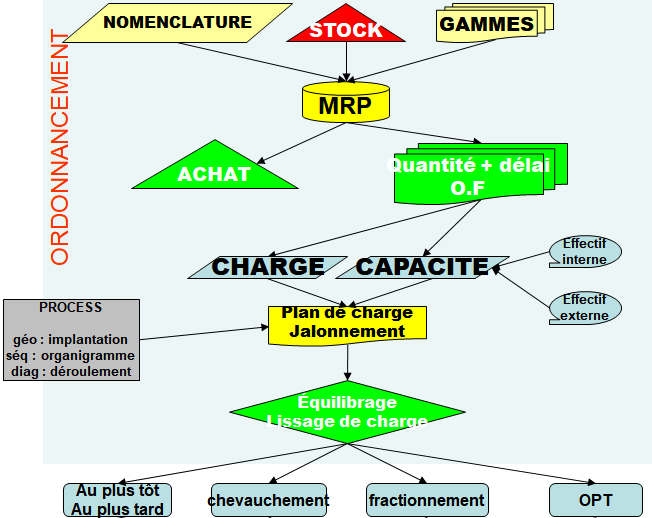
Une fois l’équilibre charge-capacité obtenu, il reste à ordonnancer (jalonner) les différentes tâches d’une fabrication sur un planning Gantt.
Si vous n’êtes pas familiarisé avec le Gantt, je vous invite à suivre le chapitre 2 de la partie 4 du cours "Pilotez la maintenance dans l'industrie du futur".
Exemple de planning Gantt ci-dessous. L’échelle est en heures. Les tâches sont au nombre de 8. Le chemin critique : A, D, E, H.
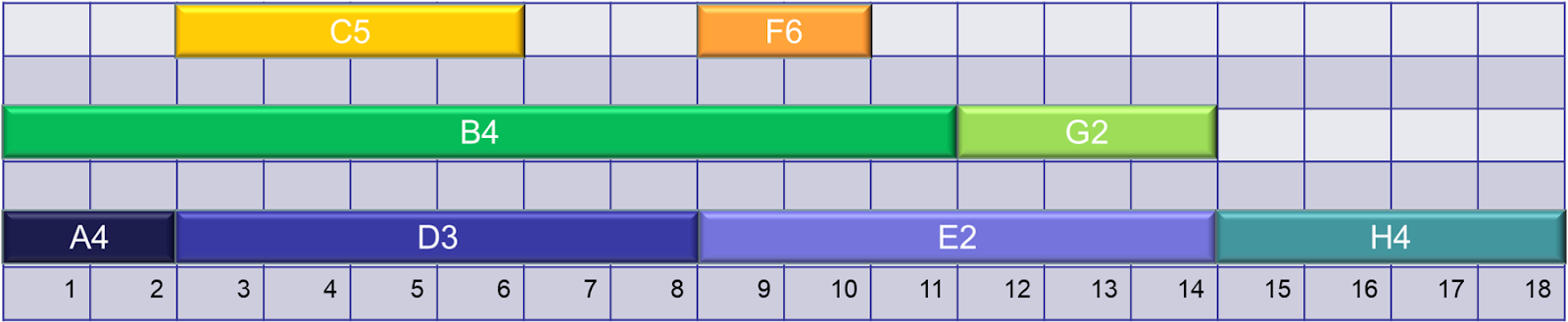
Les techniques de jalonnement sont : au plus tôt, au plus tard.
Jalonnement au plus tôt
Les tâches de fabrication sont planifiées dans l’ordre chronologique dès que les moyens de production sont disponibles :
avantage : méthode très simple ;
inconvénient : création de stocks.
Exemple :
Les OF n° 1, 2, 3, 4 sont arrivés dans cet ordre.
La fabrication de chaque OF passe par les postes de 1 à 6 dans cet ordre. La plupart des OF ne nécessitent pas de passer par tous les postes.
On considère que tous les postes sont disponibles à t = 0.
Postes | P 1 | P 2 | P 3 | P 4 | P 5 | P 6 | Délai livraison |
OF 1 OF 2 OF 3 OF 4 | / 1 h 6 h 5 h | 2 h 3 h 2 h 5 h | / 5 h / 3 h | / 3 h 4 h 8 h | 5 h 3 h 2 h / | 7 h 2 h 7 h / | 35 h 40 h 30 h 37 h |
Source : Des outils pour la gestion de production industrielle - AFNOR
Le jalonnement des tâches au plus tôt et l’identification des délais donne ce qui suit :
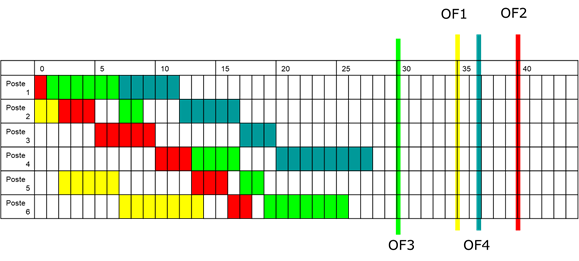
La durée de stockage des en-cours et produits finis est de 63 h, dont 5 h de stock d’en-cours (OF 1 et 3).
Jalonnement au plus tard
Pour réduire la durée de stockage, l’idée est de planifier les OF du plus urgent au moins pressé en partant de la date de livraison (date de fin) et en remontant le temps (rétroplanning), de la dernière tâche à la première :
avantage : stock réduit ; possibilité d’ordonnancer des urgences ;
inconvénient : risque de retard de livraison en cas de défaillance des ressources de production.
Avec le même exercice, l’ordre de priorité est : OF 3 (urgent), OF 1, OF 4, OF 2. Nous obtenons ceci avec le jalonnement au plus tard :
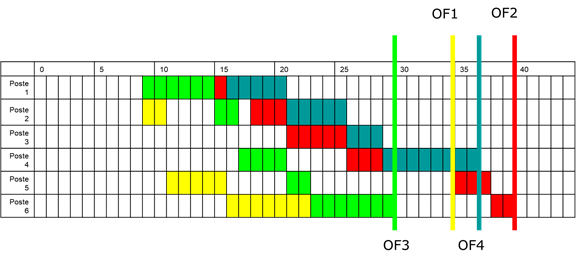
La durée de stockage des en-cours et produits finis est de 20 h, dont 8 h de stock d’en-cours (OF 2).
L’OF 1 n’est pas fractionné. Sa date de fin est 22 h au lieu de 35 h.
Il est aussi possible de combiner les 2 techniques. C’est-à-dire ordonnancer au plus tôt (très simple) et à partir de la date de fin, opérer un rétroplanning pour éventuellement combler des heures disponibles.
Exemple : Les OF rouge et vert sont ordonnancés en priorité. L’OF noir planifié dans les heures disponibles. Mais on constate un stock de son en-cours de 7 h.
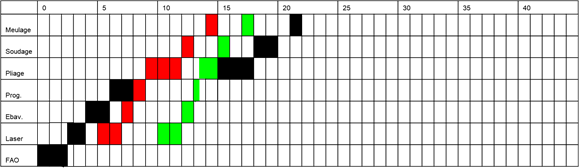
La technique consiste à opérer le rétroplanning de l’OF noir à partir de sa date de fin (22 h).
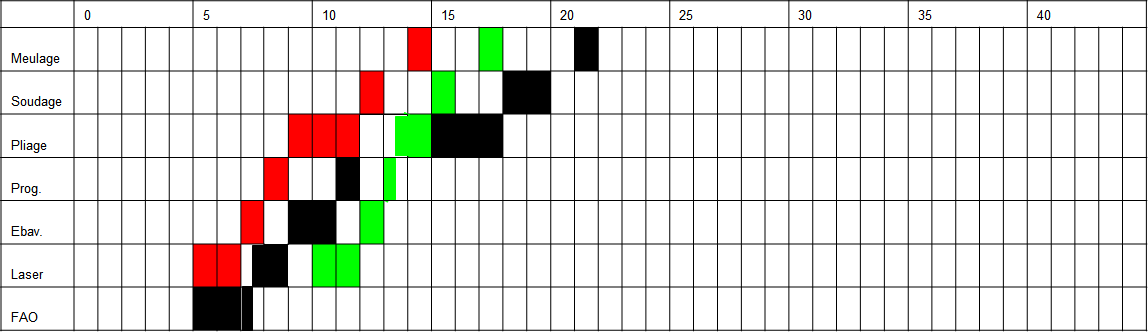
Le gain de stock en réduisant l’en-cours est de : 7 - 3 = 4 h.
Optimisez par chevauchement ou fractionnement
Deux techniques permettent de réduire les temps de fabrication. Pour les découvrir et mesurer leur efficacité, je vous propose de planifier les opérations d’usinage d’un lot de blocs-moteurs comportant une culasse et un chapeau.
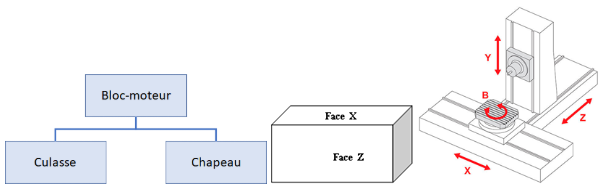
Les opérations d’usinage sont données ci-dessous :
Pièces | N° phase | Désignation | Postes | Tps de préparation (min) | Tps unitaire (min) |
CULASSE | 10 20 | Usinage face X Usinage Face Z, Y | Fr CN CU | 30’ 60’ | 5’ 30’ |
CHAPEAU | 10 | Usinage face X | Fr CN | 30’ | 10’ |
BLOC-MOTEUR | 10 | Assemblage | MO | 0’ | 20’ |
Abréviations : Fr CN Fraiseuse à commande numérique ; CU Centre d’usinage ; MO Main-d’œuvre.
La préparation correspond aux changements d’outils et réglages nécessaires à l’usinage. L’OF est de 24 blocs-moteurs. On considère que les 3 postes sont disponibles à t = 0 et que la culasse et le chapeau sont usinés sur la même machine Fr CN.
En respectant la chronologie d’usinages de la culasse et du chapeau puis de l’assemblage du bloc-moteur, et en calculant les temps nécessaires à l’ordonnancement des opérations par lot de 24, voici ce que nous avons :

La durée est de 23,5 h sans chevauchement des temps de réglages (en gris) de CU sur Fr CN. Le lot de culasses attend 1 heure le réglage du CU.
Nous pouvons remarquer que le régleur du CU peut sans problème changer d’outil une heure avant et réduire ainsi le temps total de fabrication du lot.

La durée est de 22,5 h avec chevauchement. Le régleur anticipe sa préparation pour pouvoir usiner dès que le lot de 24 sort de l’atelier de la Fr CN.
Chevauchement
Nous allons mettre en application cette technique de chevauchement pendant les opérations d’usinage.
Plutôt que d’attendre la fin de l’usinage sur Fr CN du lot de 24 culasses pour commencer l’usinage sur le CU, nous allons commencer l’usinage sur le CU quand la Fr CN a usiné 12 culasses (50 %). De même, nous commencerons à assembler quand le CU aura usiné 12 culasses.
Grâce aux chevauchements de la Fr CN et du CU, nous pouvons réduire l’ensemble à une durée de production totale de 15,5 h. Le gain est de 8 h, soit 34 %.

Fractionnement
Nous allons diviser (fractionner) le lot de 24 blocs-moteurs en 3, soit 3 lots de 8 et constater que cette technique est plus simple et très efficace. Ainsi, nous commençons par ordonnancer 8 blocs-moteurs, en profitant de notre connaissance du cas n° 2 pour faire chevaucher le réglage du CU. Nous arrivons au résultat ci-dessous :

Le premier bloc-moteur sort à 7 h 50 au lieu de 23,50 h. Nous pouvons maintenant continuer à ordonnancer les deux autres lots de 8. On constate des opérations rapides, et une opération lente, appelée “goulot”.
Le goulot est bien sûr le CU. Il ne s’arrête pas, alimenté par la Fr CN à la demande. On ne cherche pas à cumuler au plus tôt les opérations de la Fr CN. Cela provoquerait des stocks inutilement. Chaque lot de 8 s’imbrique dans le suivant, ce qui donne une durée de 15 h 50, avec l’avantage de livrer rapidement et en continu le client sans lui infliger des stocks lourds.
L'inconvénient est le changement d’outils fréquent sur la Fr CN.

Cette technique est applicable dans tous les cas sans restriction. Elle avantage le client mais demande des changements de séries rapides (voir technique du SMED). Son exploitation ultime amène à ordonnancer des lots unitaires, c’est-à-dire pièce par pièce.
Mesurez et maîtrisez votre file d’attente d’OF
Au début d'une période, des OF sont programmés Qe (ouverts mais non lancés) alors qu'une charge en cours de fabrication S va permettre d'évacuer des OF complets.
Pendant ce temps des OF nouvellement arrivés E s'accumulent en file d'attente.
Quelle sera la file d'attente Qs en fin de période ?
Comment réguler le délai de fabrication ?
Comment contrôler les en-cours ?
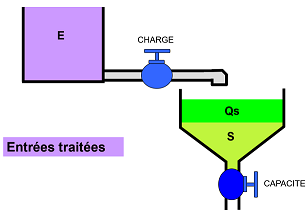
CHARGE : nombre d’heures de travail fonction du nombre d’OF entrés ;
CAPACITÉ : volume d’heures disponibles en ressources.
L’ouverture de la vanne de charge augmente les OF à traiter et surcharge la capacité.
L’ouverture de la vanne de capacité augmente la vitesse de traitement des OF en cours.
Ces décisions incombent au gestionnaire de production. Il peut vouloir servir plus de clients en même temps (charge) ou demander au personnel des heures supplémentaires ou appeler des intérimaires (capacité). Il régule ainsi l’équilibre charge-capacité.
Prenons un exemple :
Poste de charge : Fraiseuses Composition : 5 machines Temps requis : 8 h /j Nb de j/ semaine : 5 j /sem Capacité/ semaine : 200 h | Situation initiale :
|
Il est planifié 200 h d’OF par semaine. Les entrées réelles sont fluctuantes en fonction des besoins clients.
L’écart est la différence des deux, cumulée de l’écart précédent : négatif = moins d’entrées, positif = plus d’entrées.
Formule : Écart cumulé = Entrées réelles – Entrées planifiées + écart précédent
Exemple en S4 : 205 – 200 + 10 = 15
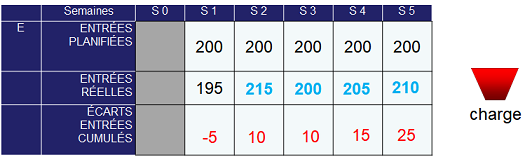
Puis il faut mesurer l’écart entre la capacité planifiée (heures supplémentaires) et le volumes d’heures réellement réalisées.
L’écart négatif = manque de personnel, positif = excès de personnel.
Formule : Écart cumulé = Sorties réelles - Sorties planifiées + écart précédent
Exemple en S3 : 215 – 220 – (–15) = -20
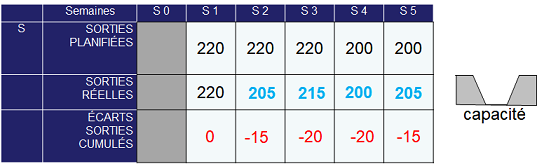
Vous pouvez maintenant prévoir semaine par semaine les en-cours planifiés et suivre en réel les en-cours réels.
En-cours planifié = Entrée planifiée – Sorties planifiée + en-cours planifié précédent
Exemple en S3 : 200 – 220 + 70 = 50
En-cours réel = En-cours planifié + écart des entrées – écart des sorties
Exemple en S4 : 50 + 15 – (–20) = 85

Un graphique de synthèse renseigné semaine par semaine permet de mettre à jour les décisions prises en première semaine.
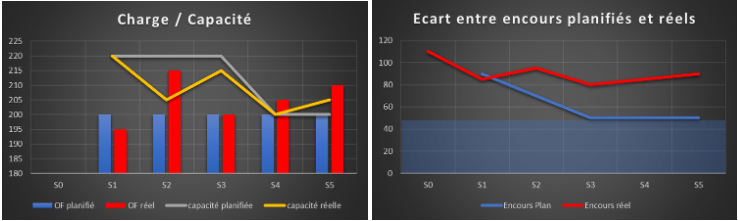
Les courbes de capacité montrent que la mise en place d’heures supplémentaires n’a pas été totalement efficace. De plus, les entrées d’OF (en bleu) ont été plus fortes que prévues (en rouge).
L’objectif de 50 h d’en-cours est ambitieux quand on part d’un en-cours en S0 de 110. Il aurait été réalisable sans les aléas observés précédemment (en-cours bleu).
Conclusion :
Les en-cours réels restent proches de 90 heures. Il faut soit relancer les heures supplémentaires, soit prendre des intérimaires.