Les défis de l’usine du futur
L’économie circulaire
Contrairement au schéma linéaire "extraction → transformation → consommation → déchets", l’économie circulaire désigne un concept économique dont l’objectif est de produire des biens et des services tout en limitant les rejets dans l’environnement, la consommation et le gaspillage des matières premières, de l’eau et des sources d’énergie.

Dans ce projet, l’industrie, en tant qu’acteur économique majeur, est présente dans les 5 piliers supérieurs : du recyclage à l’économie de fonctionnalité. Vous allez en découvrir quelques-uns.
Les économies du recyclage
On évalue le contenu énergétique d’un matériau en kWh : c’est la consommation d’énergie nécessaire pour produire une masse de ce matériau. Elle est, par exemple, de 31 500 KWh/tonne d’aluminium primaire produit en France (en 2010). On constate que le contenu énergétique des matériaux recyclés est largement inférieur à celui de ses productions originelles.
À l’heure où l’accès à l’énergie commence à être une préoccupation majeure, il est intéressant de comparer l’énergie dépensée pour extraire un métal natif du milieu naturel et celle pour le recycler. Le gain est de : aluminium > 90 % ; cuivre > 84 % ; acier > 60 %.
Par exemple, le contenu énergétique de l’aluminium recyclé est de 1 500 KWh/tonne au lieu des 31 500 KWh/tonne d’aluminium primaire ! De plus, les émissions de CO2 associées à la production primaire des métaux rares est une source gigantesque de gaz à effet de serre.
L’approvisionnement durable
La consommation des ressources de la planète atteint au plan mondial un niveau de croissance qui ne peut plus se prolonger sans dommages irréversibles, ou sans hypothéquer la disponibilité de ces ressources pour les générations futures. Au rythme actuel de croissance de la consommation, 183 milliards de tonnes de matières premières seront consommées dans le monde en 2050, contre 85 milliards de tonnes actuellement.
Les matières premières, qu’elles soient issues de la biomasse, minérales ou énergétiques, et qu’elles soient renouvelables ou non, ne doivent donc être exploitées qu’au regard de leur disponibilité et de leur impact sur l’environnement.
L’écoconception
L’écoconception est une méthode de conception d’un produit qui doit permettre, à performances égales, de minimiser ses impacts environnementaux, tout au long du cycle de vie, dans un processus d’amélioration continue et à coût maîtrisé. Elle se décompose ainsi :
1 - La démarche de R&D
On représente le processus d’innovation partielle par une succession de jalons qui servent de points de mesure de la maturité technologique, pour engager la poursuite de l’innovation. L’échelle de 1 à 9 (TRL – Technology Readiness Level) correspond aux niveaux de maturité, du plus faible (approche scientifique) au plus élevé (mise au point du produit).
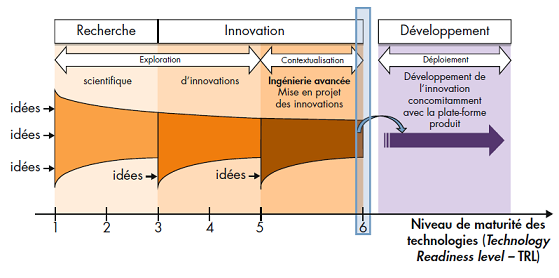
2 - La définition des exigences environnementales
Les exigences intrinsèques s’appliquent aux fonctions et aux composants du produit (ex. : réglementation sur les substances chimiques).
Les exigences extrinsèques s’appliquent au cycle de vie du produit, et en particulier à sa recyclabilité.
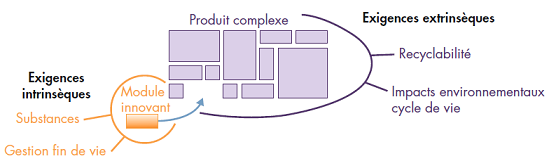
3 - Le référentiel d’écoconception
Il s’agit de définir une liste des exigences et de donner pour chacune le livrable correspondant et l’outil nécessaire pour fournir ce livrable.
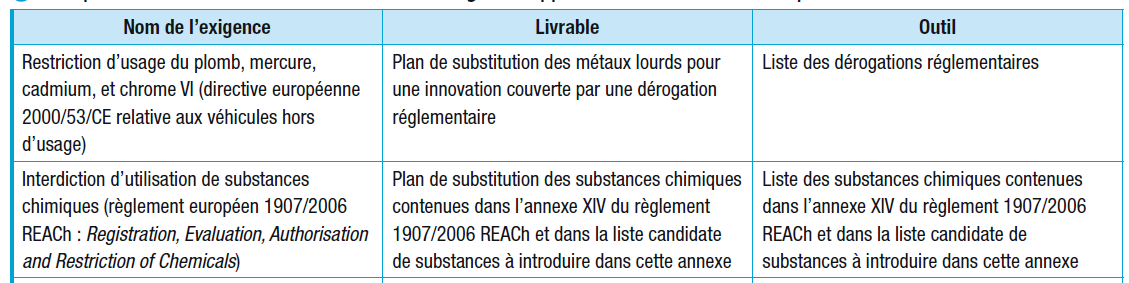
4 - La check list des exigences environnementales
La check-list est utilisée par les ingénieurs en innovation afin de contrôler la conformité de leur innovation, au regard des exigences environnementales définies par l’intégrateur environnemental et son équipe. Pour chaque exigence environnementale, l’expert associé doit concevoir une série de questions à poser pour aboutir à trois types de réponse :
Go : l’innovation est conforme à, ou n’est pas concernée par, l’exigence environnementale ;
Go avec livrable : l’innovation n’est pas conforme à l’exigence environnementale et un livrable est attendu afin de mettre l’innovation en conformité ;
No Go : l’innovation n’est pas conforme à l’exigence environnementale suite à l’identification d’un problème bloquant, par exemple un problème réglementaire.
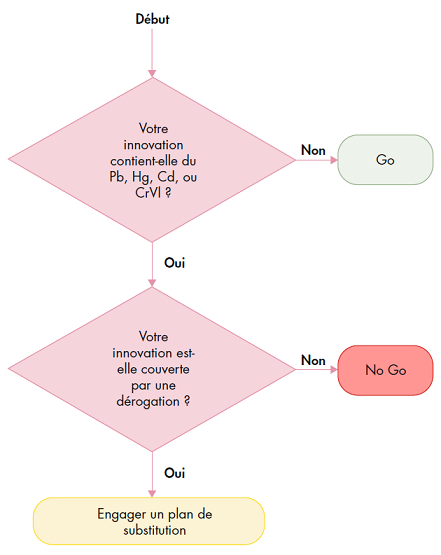
L’écoproduction
L’écoproduction ou écologie industrielle, c’est miser sur une économie sobre s’appuyant sur les concepts d’optimisation et de récupération des flux (énergies, matières première et eau), de cycle de vie ainsi que de gouvernance durable. Elle est basée sur 3 concepts :
La sobriété : comment faire mieux avec moins.
L’efficacité : comment réduire la quantité d’énergie pour répondre à un même besoin.
Le renouvelable : comment faire différemment en priorisant les énergies propres.
La sobriété
Certains secteurs industriels sont irrassasiables en terme d’énergie. À ce point gloutons qu’ils leur faut chercher des sites ou pays dans lesquels l’énergie est bon marché, au détriment de toute considération pour l’environnement. C’est ainsi que l’aluminium extrait en Australie est traité en Norvège, bien connue pour son énergie fossile, ou encore en Savoie, connue pour son réseau de conduites forcées d’eau et d’électricité “verte” peu coûteuse. D’un côté le minerai traverse et pollue la planète, de l’autre l’usine de traitement pollue totalement une petite vallée encaissée et perturbe durablement le biotope des versants montagneux sur lesquels les cascades ont été collectées.
L’efficacité énergétique
L’efficacité énergétique est le rapport entre l’énergie minimale nécessaire au fonctionnement d’une installation et l’énergie totale consommée. L’efficacité énergétique peut être passive (isolation…) ou active (système de mesure et de management de l’énergie, etc.). Dans la vision de l’usine du futur, les procédés géreront intelligemment plusieurs sources d’énergie (solaire, éolien, chaleur récupérée, etc.), et pourront dans certains cas en produire.
Sous la pression écologique, économique et réglementaire, les industriels vont de plus en plus intégrer l’optimisation de l’utilisation de l’énergie (consommation, production) dans leur process de production, mais également dans la gestion des « utilités » (air comprimé, gestion de l’eau de process…). Depuis 2015, les audits énergétiques sont obligatoires dans les entreprises de plus de 250 salariés.
Concrètement, l’entreprise doit :
récupérer son énergie (chaleur, cinétique...), la stocker et la réinjecter dans le réseau ;
augmenter les rendements par diminution des frottements mécaniques (sciences de la tribologie) ;
surveiller le comportement des procédés par analyse comparative et analyses algorithmiques (big data) ;
mesurer la performance et manager en temps réel l’énergie consommée.
L’économie de la fonctionnalité
En résumé
L’usine du futur demande une adaptation humaine et matérielle à moyen terme (d’ici 2050). Elle représente une rupture technologique comme celle de l’internet dans les années 90. L’usine 4.0 est avant tout une usine communicante. L’objectif est d’être en capacité de faire des choix fiables et rapides grâce à une panoplie de techniques de surveillance connectée à une intelligence artificielle et renseigné par vos retours d’expérience. Vous opterez bientôt pour des apprentissages du personnel par réalité augmentée, des machines connectées via des capteurs (d’usure, de comptage, de contrôle qualité…) à l’IA et des AGV nouvelle version, les AIV.
Pour vous préparer à cette révolution industrielle vous allez commencer à travailler avec vos partenaires sur la modélisation des flux de matières et d’informations et leurs flexibilités. Demain est déjà là, il s’agit de ne pas rater le train en marche !
De plus vos clients vous mettrons la pression sur le sujet ‘brûlant” de votre empreinte écologique industrielle. Nous avons vu comment vous pourrez vous associer à la démarche écologique de l’économie circulaire.