L’usine du futur doit s’adapter aux contraintes du marché : clientèle exigeante et volatile, concurrence exacerbée. Les usines actuelles manque parfois de “flexibilité” pour affronter cette guerre économique. Flexibilité ? où, comment et avec qui ?
Le changement est piloté par le client
Les choix de gestion
L’entreprise du futur sera d’autant plus compétitive qu’elle saura discerner, avant et mieux que ses concurrents, les besoins à venir de ses marchés, en termes de produits, de services et d’amélioration des processus. Elle peut choisir entre plusieurs gestions de la chaîne logistique (supply chain) :
gestion par affaire (engineer to order) : pour produits complexes conçus et réalisés à la demande ;
production à la demande (make to order) : pour produits coûteux ou petites séries ;
assemblage à la commande (assemble to order) : pour produits dont l’approvisionnement des composants est long ;
production sur stock (make to stock) : pour une production basée sur des prévisions type MRP ;
sur-mesure de masse (mass customization) : pour produits de consommation personnalisés.
Dans cette dernière approche, les exigences variées et changeantes des clients pilotent la production. C'est une nouvelle approche du consumérisme, à laquelle il faut répondre pour créer de la richesse partagée et générer des emplois. On passe à un marché de l'offre personnalisée (mass customization), qui nécessite une nouvelle organisation de la production.
Les immenses sites industriels destinés à fournir des produits standard laisseront la place à des sites de taille plus réduite, conçus pour fournir régionalement des produits et dotés de moyens de production adaptés à des séries plus modestes, pouvant répondre à des marchés de plus en plus volatils et imprévisibles. La logistique du futur constituera un des éléments en faveur de la réintroduction de sites de production en zone urbaine.
Cet enjeu implique de répondre aux besoins des clients par le développement d’un « marketing client » au lieu d’un « marketing produit ».
Les garanties
Les clients cherchent plus de garanties. Avec l’industrie 4.0, les notions de traçabilité et de gestion de flux deviennent essentielles. La traçabilité sera présente à toutes les étapes de la production et hors des usines, pour garantir la sécurité des consommateurs, optimiser l’organisation des sociétés et assurer la lutte contre les contrefaçons.
Comment répondre à la flexibilité ?
Il faut gagner en productivité, c’est-à-dire gagner du temps. Les idées nouvelles développées dans l’usine du futur sont :
Accélérez la mise sur le marché de produits innovants
En réduisant le temps de conception, de prototypage, des essais des nouveautés grâce à la réalité virtuelle appliquée aussi dans la conception des outils de fabrication tels que moule, matrice, gabarit… (PLM Product Lifecycle Management - Gestion du cycle de vie d’un produit).
Améliorez la fluidité de circulation des matières dans l’usine
en équipant les machines de production et les moyens de manutention de capteurs et d’IoT.
L’une des tendances est aujourd’hui de descendre encore plus bas dans les niveaux d’automatisation, même en dessous de l’automate. Il faut pouvoir automatiser le paramétrage à distance des capteurs, afin qu’il ne soit plus réalisé manuellement. Cela devient possible avec la technologie IO-Link qui apporte du numérique à ce niveau ;
en supprimant la laborieuse gestion par les OF papier ou même écran.
La ligne de production utilise des porte-outils intelligents équipés d’étiquettes RFID pour identifier la variante-produit souhaitée, et transmettre les matériaux et processus nécessaires en production, directement à la machine concernée. Chaque station lit ces étiquettes et affiche les informations pertinentes à l’écran à l’intention de l’opérateur, afin de réduire le temps de traitement et d’optimiser l’utilisation des ressources.
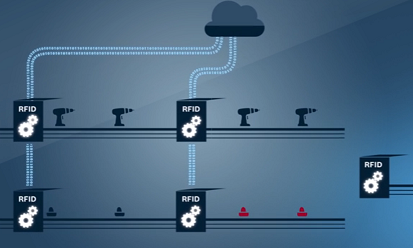
Au fait, pourquoi le “temps réel” nous ferait-il gagner du temps ?
Prenez un exemple simple : vous êtes dans le train et vous voulez profiter de chaque minute pour terminer un rapport sur votre PC. Combien de temps vous reste t-il avant l’arrivée ? Votre smartphone sur l’application SNCF vous répond :
il vous reste 23 min, mais avec le retard de 7 min, il vous signale l’arrivée dans 30 min, quai 1, puis 20 min d’attente pour le prochain train avec un départ quai 3. De plus, la personne qui vous attend est prévenue automatiquement par SMS de votre arrivée.
Toutes les informations dont vous avez besoin vous sont fournies triées et donc personnalisées. Rassuré, vous êtes en mesure de planifier “en temps réel” votre activité : confort, temps gagné, apaisement, qualité de vie et du travail, les employés de l’usine du futur communiqueront avec le même principe avec en plus la possibilité de choisir des options de production ;
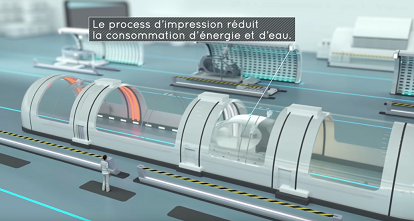
en réduisant le nombre d’intermédiaires, par exemple en assurant le transport au client final (drones) ;
en réduisant le nombre d’intermédiaires par exemple en assurant le transport au client final (drones).
en flexibilisant les machines.
Les deux principaux piliers d’une « flexibilité 4.0 » sont : un outil de production aisément reconfigurable, et l’exploitation d’un jumeau numérique pour tester ses possibles d’évolution. Pour réagir rapidement à de profondes réorientations sur ses marchés, l’entreprise doit pouvoir disposer d’un atelier polyvalent, facilement reconvertible pour d’autres applications. C’est également dans la même logique que des robots collaboratifs mobiles peuvent être déplacés dans l’usine et réinstallés en 48 h sur un autre poste, au gré des besoins.
Adaptez la machine à l’homme
les différents postes de travail s’adaptent automatiquement aux besoins, préférences morphologiques et compétences des opérateurs, grâce à l’utilisation d’un lecteur de puce intégré. Un récepteur placé à la station d’assemblage lit l’étiquette Bluetooth de chaque utilisateur et règle l’écran du poste de travail en fonction de son profil. L’éclairage de la station, la taille de la police ou encore la langue d’affichage s’adaptent instantanément. Même le niveau de précision des informations apparaissant à l’écran s’ajuste automatiquement en fonction de la qualification de l’utilisateur ;
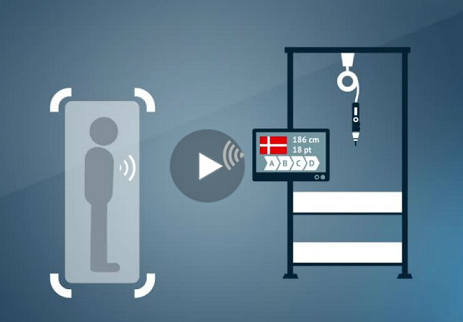
en automatisant la prise de décision avec l’intelligence artificielle (IA) ;
en faisant communiquer toutes ces informations entre elles afin de générer un flux de production optimal.
Les points faibles sont rapidement identifiés. Le système d’information de production collecte, filtre et affiche en continu les données de production, constituant ainsi une plateforme de communication pour les opérateurs et décideurs au sein du département Production. Cette plateforme permet de déclencher rapidement les processus de résolution nécessaires, avec une réduction des temps d’immobilisation et une hausse de la productivité à la clé ;
en améliorant l'apprentissage du personnel sur des métiers en évolution.
Regardez comment, dans cette vidéo, le constructeur est devenu leader technologique sur le marché d’éclairage solaire autonome. Pour conserver sa fabrication en France, il a conçu un atelier modulable construit en tubes métalliques. Un écran de “bord de ligne” permet aux opérateurs de connaître les objectifs de production, un 2e écran permet de simuler l’organisation pour optimiser l’activité et éviter les risques productifs. Enfin, chaque opérateur, avec des écrans de réalité augmentée, peut s’autoformer rapidement.
En résumé, voici un schéma synthétique de l’évolution logistique dans l’usine 4.0 :
une consigne est envoyée dans le système à partir de tests en réalité virtuelle et jumeau numérique,
la production et les flux de la Supply Chain 4.0 (robotique, exosquelettes, AGV, drones,…) sont analysés en temps réel,
l’intelligence artificielle et le deep learning régulent l’équilibre charge-capacité en fonction des aléas détectés.
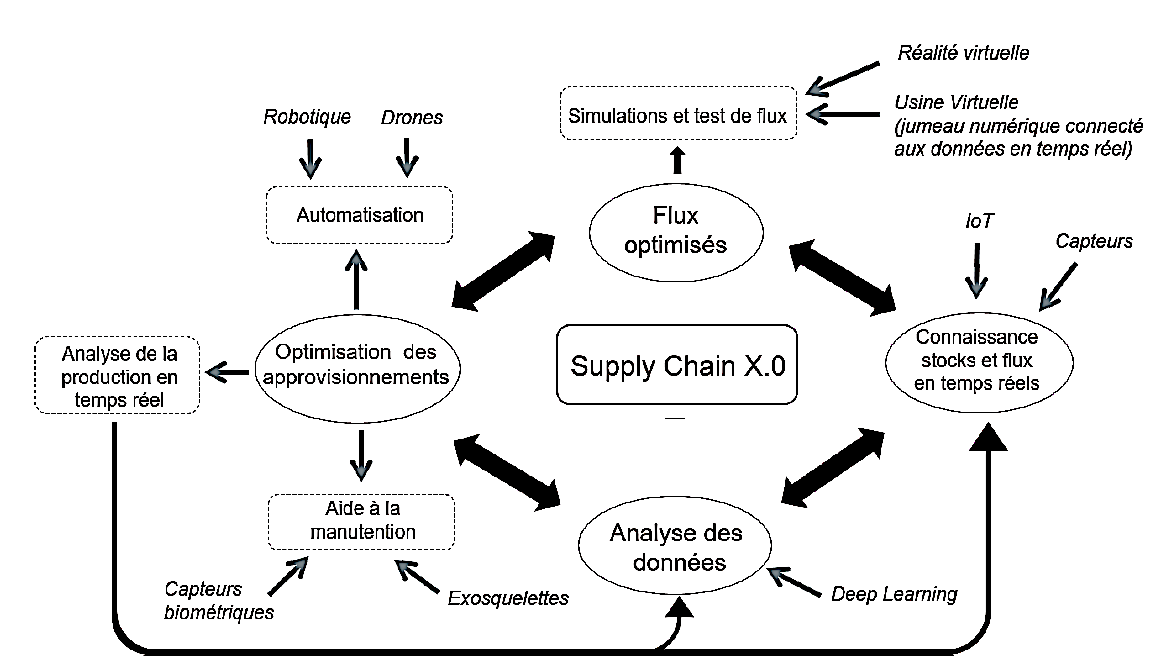
Comment assurer le “sur-mesure de masse” ?
Les séries courtes sont parfaites pour le “sur-mesure de masse”, mais comment raccourcir encore les changements de séries ? Alors que le SMED a déjà permis de diviser le temps par 15 par rapport au changement de version de type “artisanal” !
Il est possible d’abord d’essayer d’automatiser le plus possible la chaîne de production, ceci dans l’objectif de réduire les délais dus à la fatigue et aux erreurs de fabrications. Enfin, nous pouvons tenter de réduire le nombre de mouvements et la distance à parcourir pour chacun des salariés, leur permettant ainsi d’être plus productifs dans leurs tâches.