Organisez votre atelier en JAT
L’objectif premier des Japonais, quand ils ont mis au point le juste-à-temps, était de se libérer des stocks de matières, d’en-cours et de produits finis, tout en optimisant la satisfaction du client. Ainsi, le JAT privilégie d’abord le client.
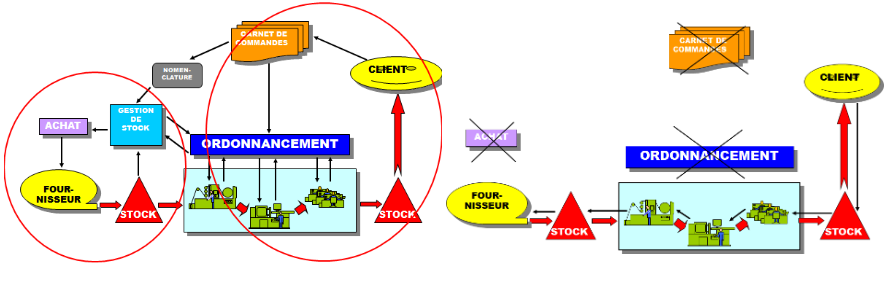
La gestion des flux et des OF est réalisée localement au niveau des opérateurs.
On parle de flux tiré, car l’ordre de fabriquer part de la demande du client final au poste final (flèches d’informations noires en sens inverse du flux de production), puis du poste final au poste précédent, etc.
On parle aussi de flux tendu car, contrairement au flux poussé, il n’y a plus de stock de réserve en cas d’aléa de fabrication.
Et enfin, nous parlons de juste-à-temps car le client est servi immédiatement selon son besoin.
Adoptez la gestion par le Kanban
Pour garantir ce service au client, l’opérateur a besoin d’indicateurs visibles à son poste : le tableau Kanban.
Pour approfondir la gestion par les Kanban, je vous invite à suivre ce chapitre du cours "Pilotez l'amélioration continue dans l'industrie du futur".
Le lissage de la production par Heijunka
Le Heijunka est une des techniques du toyotisme. Elle s’applique à une production répétitive.
Contrairement au JAT, l’objectif du Heijunka n’est pas de coller à la demande et d’éviter les stocks. Non ! L’enjeu est de lisser la production pour la rendre prévisible et régulière, réduire le stress des pics de charge et du besoin en heures supplémentaires. On gère la stabilité de la production et le “confort” du personnel. Techniquement, le Heijunka s’apparente au fractionnement vu précédemment.
Prenons l’exemple d’un atelier dont le temps d’ouverture est de 7 h/j, 20 j/mois. On y fabrique un produit en une heure sous 6 versions différentes, dont les volumes sont les suivants :
Bleu | Rouge | Orange | Vert | Jaune | Mauve | Total |
60 | 28 | 18 | 18 | 10 | 6 | 140 |
Nous pouvons facilement calculer une capacité de 140 h (7 h x 20 jours), ce qui correspond à notre charge.
Si je vous demandais de planifier traditionnellement les 6 versions, je suppose que vous auriez choisi de commencer par les grandes séries pour vous en débarrasser, mais aussi parce que vous aurez déjà accompli les ⅔ du travail avec bleu et rouge ! Il n’y a 66 % de chances que ces 2 versions soient réclamées dans le mois. Plus prosaïquement, pendant ce temps : vous êtes tranquille ! Chaque jour, 7 pièces sont produites.
Notre planning des couleurs est le suivant :
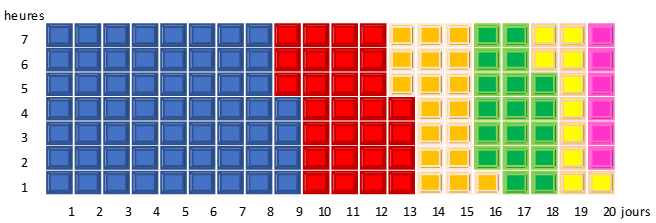
Avantage : votre équipe et vous, êtes “tranquille” pendant une petite dizaine de jours.
Inconvénient : vos clients vont devoir attendre pour avoir d’autres couleurs que du bleu.
Le client qui demande une couleur de chaque attendra même 20 jours s’il passe sa commande le 1er jour du mois !
Le ratio de tension est de :
Inversez votre planning : commencez par les séries courtes.
Que constatez-vous ?
Si vous inversons notre planning, avec d’abord les séries courtes, nous constatons que c’est déjà un peu mieux. L’attente ne sera “que” de 12 jours en commandant le jour 1… mais pas si la commande est passée le jour 2.
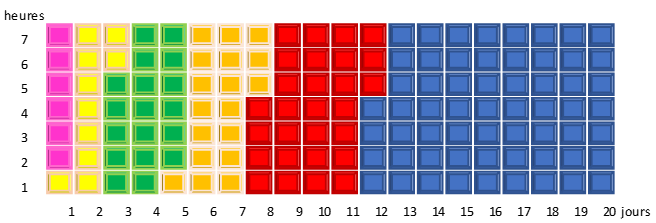
Donc, rien est réglé !
Fractionnons notre production comme nous l’avons vu au chapitre précédent "Pilotez un processus de fabrication". Au lieu d’étaler notre planning de couleurs sur 4 semaines, ordonnançons les 6 couleurs sur 1 semaine, tout en conservant les proportions de chaque couleur.
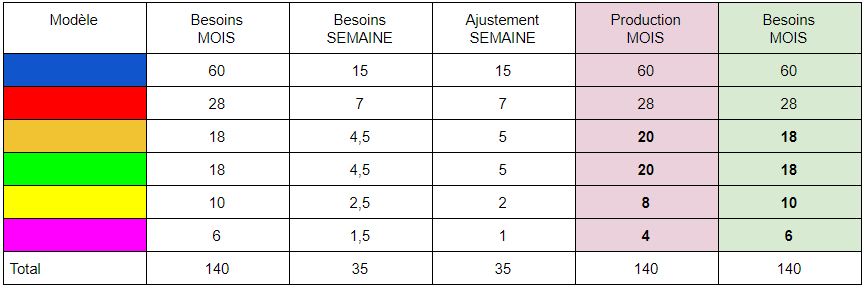
Sur les petites séries, l’ajustement SEMAINE pose un petit problème de décalage entre la “production MOIS” et les “besoins MOIS”.
En fin de mois, il y a un excédent de + 2 pour les modèles Orange et Vert et un déficit de – 2 pour les modèles Jaune et Mauve.
Il nous suffira d’ajuster la production, la dernière semaine du mois, pour parvenir aux besoins clients.
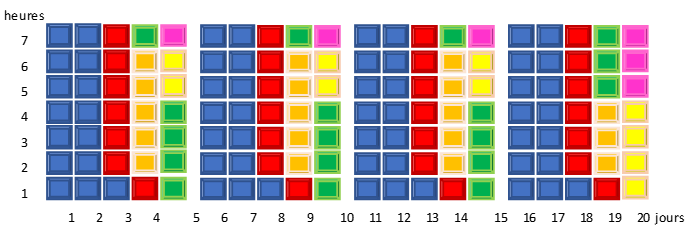
Avantage du fractionnement Heijunka : le client exigent attendra au minimum 3 jours et au maximum 5 jours pour avoir les 6 versions.
Le ratio de tension est de :
Puisqu’il est répétable, l’ordonnancement peut être affiché dans un tableau comme celui-ci, avec une case par heure. L’opérateur prend l’ordre de fabrication et l’exécute.
En résumé
Le quotidien du responsable de production est de manager les problèmes. Il doit donc former son personnel aux outils standards de résolution que nous avons traités : QQOQCP, Pareto, diagramme spaghetti, 5 "pourquoi", calcul de rentabilité…
Pour affiner l’ordonnancement des tâches et réduire les délais de fabrication, nous avons vu différentes méthodes plus pertinentes que le simple jalonnement au plus tôt ou au plus tard. Il s’agit des techniques de chevauchement, de fractionnement ou de la gestion par les goulets d’étranglement dont le heijunka est une variante.
Vous êtes arrivé à la fin de ce cours, félicitations ! N'oubliez pas de réaliser les exercices de fin de partie pour valider les compétences suivantes :
s'approprier les processus métier de l’activité Production ;
utiliser les principaux outils de la production ;
appréhender les technologies de l’industrie du futur liées à la production ;
piloter la démarche grâce aux outils de la production.
Très bonne continuation !