Dans le monde de l’entreprise, on se remet constamment en question, essentiellement dans un but économique. La perfection n’est que très rarement atteinte, un processus peut, dans 99 % des cas, être amélioré.
Bien que notre processus de fabrication ait été qualifié, il n’est pas parfait et l’on peut très souvent trouver des axes d’amélioration. Mais avant de le perfectionner, il faut pouvoir l’évaluer et identifier les leviers d’amélioration.
Mesurez le temps
Pour évaluer un processus, nous pouvons commencer par mesurer le temps de cycle de production. Une première méthode est le chronométrage.
Le mode opératoire doit être sous contrôle et chaque opérateur doit utiliser les mêmes méthodes. Il s’agit de mesurer le temps de chaque séquence, une séquence pouvant être définie par un top de début et un top de fin donnant le relai à une autre séquence.
Si l’on prend les résultats du chronométrage de notre processus :
| Nombre opérateurs | Temps de cycle théorique (secondes) | Changements de fabrication (min) | Taux de rendement (%) | Temps de cycle réel par PF (secondes) |
Tirage | 3 | 7,2 | 10 | 40 | 18 |
Collage manuel | 6 | 12 | 15 | 90 | 13,3 |
Découpe/ poinçonnage | 2 | 9,6 | 180 | 50 | 19,2 |
Décorticage | 2 | 4,5 | 0 | 25 | 18 |
Pliage | 2 | 9,2 | 60 | 60 | 15,4 |
Encollage/ repliage | 4 | 9 | 10 | 80 | 11,25 |
Mise en boîte conditionnement | 8 | 12 | 10 | 80 | 15 |
Dans notre cas, nous avons :
un temps de cycle théorique de 63,5 secondes ;
et un temps de cycle réel de 110,15 secondes, soit un écart de 47 secondes donc 73 % de plus.
De manière simplifiée, et sans rentrer dans le détail des opérations, nous avons déjà un écart important entre le temps de cycle théorique et le temps de cycle réel !
Dans une situation où les tâches sont répétitives, il est possible d’utiliser le simogramme pour évaluer le processus. C’est en effet un outil qui permet de représenter graphiquement l’organisation temporelle des différentes tâches ou différents cycles de fabrication.
On distingue 3 types de tâches :
Temps manuel (Tm) : pour une tâche effectuée par un opérateur simple, on indique le code de la tâche et la durée, la longueur de la barre est proportionnelle à la durée.
Temps technologique (Tt) : pour une tâche effectuée par une machine seule (exemple : impression dans notre cas, mais cela peut être un four).
Temps technico-manuel (Ttm) : pour une tâche effectuée par un opérateur sur machine (exemple : une action de soudage, de meulage).
Temps manuel fréquent (Tmf) : par exemple des contrôles périodiques qui vont être représentés hachurés, en indiquant la fréquence.
Prenons l’exemple d’un potier :
Tâche | Type | Libellé | Durée (cmin) |
---|---|---|---|
I | Tm | Préparation de l’argile | 28 |
II | Tm | Tournage de la pièce | 136 |
III | Tm | Ébavurage de la pièce | 32 |
IV | Tm | Mise au four | 12 |
V | Tt | Cuisson | 720 |
VI | Tm | Sortie du four | 24 |
VII | Tmf | Approvisionnement en argile (toutes les 6 pièces) | 52 |
En représentation graphique, cela donne :

C’est l’étape V (qui correspond à la cuisson) qui est la plus longue. Bien heureusement, le potier n’attend pas devant son four pendant tout le temps de la cuisson.
On peut donc focaliser sur les améliorations à cette étape.
Un troisième mode d’évaluation des processus est l’utilisation de la méthode dite "d’observations instantanées". Cette méthode va nous permettre de mesurer un évènement : par exemple les pannes d’une machine. C’est une méthode qui demande de la préparation. Il faut :
Bien établir le sujet de l’étude : le phénomène observé (quoi), les acteurs impliqués (qui), le périmètre (où), le nombre d’observations (combien), la manière de réaliser les observations (comment).
Bien définir les états de ce qui sera observé : « en panne/en fonctionnement », c’est une étape importante.
Préparer l’outil de relevé des observations (feuille de bâtonnage, smartphone…). Les horaires d’observation seront prédéfinis, de manière aléatoire, sur l’ensemble des plages où le phénomène est susceptible de se produire. Les horaires ne doivent pas être répétitifs d’un jour sur l’autre (pour limiter tout biais). Il est possible de construire un circuit afin de réaliser plusieurs observations sur le parcours.
Réaliser les tournées aux heures prévues, en effectuant une observation ponctuelle à chaque fois.
Dépouiller les résultats.
Cette méthode statistique peut montrer des phénomènes de panne fréquents.
Lorsque nous chronométrons notre processus, nous nous apercevons que les séquences n’ont pas la même cadence. Intéressons-nous à cette notion : voyons quel outil nous permettrait de nous mettre à la cadence idéale.
Takt time et équilibrage des postes
Remontons notre process et reprenons nos engagements vis-à-vis du client :
Notre client attend un camion de 1 836 produits par jour (34 palettes de 54 produits).
Nos horaires d’ouverture : 8 heures-16 heures = 25200/7 heures de travail effectives par jour soit 7*3600= 25200 secondes.
Nous devons produire : 1836 PF toutes les 25200 secondes, soit 25200/1836=13,73 soit un PF toutes les 13,7 secondes.
C’est ce que l’on appelle le takt time, c’est-à-dire la cadence à laquelle notre client a besoin de son produit. Si toutes les phases de notre processus sont calées sur ce rythme, nous sommes sûrs de pouvoir livrer notre client et de satisfaire ses exigences.
Le principe est donc d’équilibrer nos postes de manière à atteindre ce fameux takt time :
Poste | Cadence réelle | Cadence théorique | Takt time |
Tirage | 18 | 7,2 | 13,7 |
Collage manuel | 13,3 | 12 | 13,7 |
Découpe/poinçonnage | 19,2 | 9,6 | 13,7 |
Décorticage | 18 | 4,5 | 13,7 |
Pliage | 15,4 | 9,2 | 13,7 |
Encollage/repliage | 11,25 | 9 | 13,7 |
Mise en boîte conditionnement | 15 | 12 | 13,7 |
On voit bien que les postes ne sont pas équilibrés. De plus, 5 sur 7 sont au-dessus du takt time et 2 sont en dessous... Alors que les valeurs théoriques sont bien en dessous du takt time. Cet objectif est donc tout à faire atteignable !
Le but de l’équilibrage de poste est d’arriver à 13,7 secondes par poste :
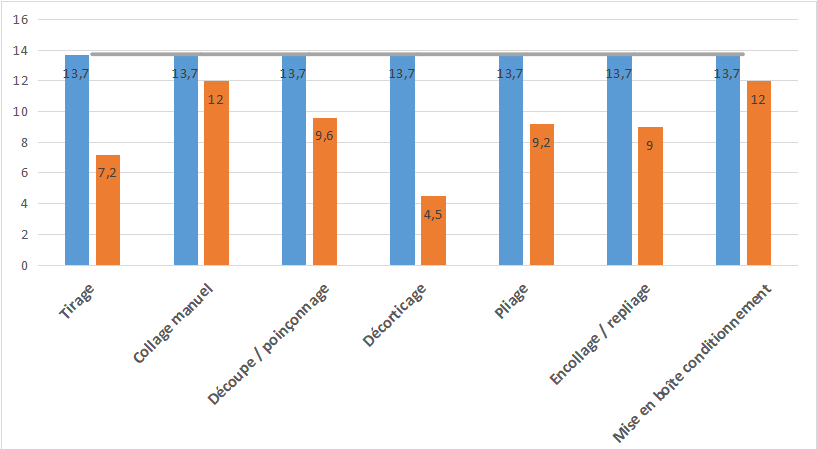
On reste au-dessus du temps théorique, mais on a la cadence adéquate pour servir le client.
Voyons quels peuvent être les leviers pour équilibrer les postes de travail.
Ergonomie et implantation
Dans l’optimisation de nos processus et en continuité avec l’équilibrage des postes de travail, nous pouvons revoir l’implantation et l’ergonomie des postes de travail.
Dans le monde de l’entreprise, on distingue deux principales implantations :
en ligne (ou à la chaîne) : les opérations se succèdent (essentiellement pour les moyennes et grandes séries) ;
en îlot de production : organisation plus flexible ou « agile », pour des petites et moyennes séries.
On peut comparer les différents paramètres de ces implantations dans le tableau ci-dessous :
Paramètres | Îlots | Lignes |
Définition | Ensemble d’opérations réalisées sur un petit nombre de postes, organisés en unités autonomes | Ensemble d’opérations réalisées le long d’une ligne ou chaîne de production |
Autonomie | Très importante | Très faible à inexistante |
Taille des lots de production, des séries | Petite à moyenne | Moyenne à grande |
Clés de succès | Répartition des charges et ressources, formation, motivation | Équilibrage des capacités et gestion des flux |
Points forts de l’organisation | Flexibilité, productivité locale et per capita, autonomie des personnels. Réduction des gestes « prendre-reposer ». | Volumes et cadences, gains d’échelle, productivité globale. Facilité de formation. |
Vitesse et importance des flux | Faibles localement, mais compensées par l’effet de « réseau » | Importantes |
S’exprime en nombre d’unités et/ou en temps total de production pour chaque lot/série | À considérer en fonction de la fréquence et de la durée des changements de lots, de séries | |
Points faibles de l’organisation | Duplication des moyens, nécessité de formation et de délégation | Impact de l’absentéisme, des changements de séries, des retards d’approvisionnement |
Réserve de progrès, gisement de gains | Capitalisation et mutualisation des bonnes pratiques développées dans certains îlots | Réduction des temps de changement de série via le SMED |
Surface nécessaire | Faible | Importante |
Stocks et encours globaux | Faibles | Importants |
Mode d’approvisionnement | Multiple et répété à chaque îlot, en petites quantités | Kitting et lots importants mis à disposition auprès des lignes |
Coût d’infrastructure | Très faible : simples tables | Important : convoyage et automatismes |
Ce tableau peut vous servir d’aide à la décision dans vos projets d’aménagement d’ateliers futurs !
Vous voyez tout de même que l’implantation en îlots présente de nombreux avantages, notamment dans la circulation des flux et des informations.
Le travail et les postes de travail doivent aussi être adaptés à l’humain, c’est pourquoi les contraintes ergonomiques sont à prendre en considération pour les aspects :
Humain : avoir des conditions de travail sans mauvaises conséquences sur la santé de nos salariés. Prendre aussi en considération d’éventuels soucis personnels afin d’adapter les postes de travail.
Motivation et satisfaction : un salarié dont on aura pris en considération les contraintes, que l’on aura écouté sera d’autant plus motivé et impliqué dans son travail. Il pourra lui-même proposer des axes d’amélioration.
Productivité : c’est en quelque sorte la résultante, un salarié bien installé et motivé sera plus productif.
Il existe également des formations « gestes et postures » qui peuvent être obligatoires, notamment aux postes où il y a des déplacements de charges. De nombreux outils existent pour soulager les efforts (tels que les chariots élévateurs, les postes de travail à hauteur réglable, etc.).
Sur notre processus, nous avons donc vu que l’on pouvait jouer sur l’humain en positionnant les postes de la manière la plus adaptée.
Lors d’un déroulement de processus, une des étapes avec le moins de valeur ajoutée et qui peut prendre beaucoup de temps, c’est le changement de série ou de fabrication. Voyons quels outils nous avons en notre possession pour optimiser ces temps.
SMED : Single Minute exchange of Die
Pour imager cette méthode, on fait souvent référence au temps de changement des roues des voitures de compétition en formule 1 qui a été réduit à un temps minimal malgré toutes les opérations qu’il y a à réaliser !
La mise en œuvre de cette méthode se fait en 4 étapes :
Supprimer les réglages : utilisation de rondelles fendues d’épaisseurs connues intercalées entre deux plans pour éviter un réglage manuel avec mesure.
Réduire les temps de réglage : par exemple, positionner, hors production, les dispositifs à une valeur estimée proche de la valeur à atteindre, au lieu de partir d’une position extrême, et effectuer une longue modification jusqu’à la valeur cible.
Réduire les temps des autres opérations : se poser la question de la bonne utilité de chaque opération : par exemple a-t-on vraiment besoin d’une vis de 12 cm ? Une visse de 8 cm ne suffirait-elle pas et ne serait-elle pas moins longue à visser ?
Standardiser les processus de changement de série : la standardisation passe par une documentation précise des procédures.
Instructions techniques
Pour standardiser les processus, il est indispensable de bien les documenter à l’aide de gammes, mais aussi d’instructions techniques. Les IT sont des "notices explicatives" dans le domaine de la maintenance également.
On doit pouvoir retrouver des trames standards, quel que soit le processus. Ainsi, si un opérateur passe de l’îlot A à l’îlot B, il ne sera pas perdu.
Vous avez donc pu voir qu’un processus est toujours « améliorable ». Il est important, pour rester compétitif, de le remettre en question et d’être en constante recherche du mieux, voire du meilleur.
Un outil de l’amélioration continue très puissant qui permet de déceler des « gaspillages », c’est la VSM (pour value stream mapping). Son but est de cartographier un processus, d’identifier les « gaspillages », puis d’analyser leur cause pour proposer des solutions. Cela peut passer par une réorganisation d’un atelier, par exemple.
Ainsi, pour résumer, l’activité que vous piloterez ne s’arrêtera pas à « industrialiser », mais aura aussi dans son panel les actions d’amélioration. Il est donc essentiel d’avoir une bonne connaissance des outils de l’amélioration continue.
Le plus central est la "Roue de Deming" ou « PDCA » pour :
Plan : prépare, planifier ce que l’on doit réaliser.
Do : développer, réaliser, mettre en œuvre (phase de test).
Check : vérifier et contrôler que cela fonctionne.
Act : agir, déployer, dans le cas d’une amélioration, à la suite de la détection d’une anomalie ; illustre bien l’état d’esprit dans lequel nous devons être lors d’un développement industriel au sein d’un service Méthodes.
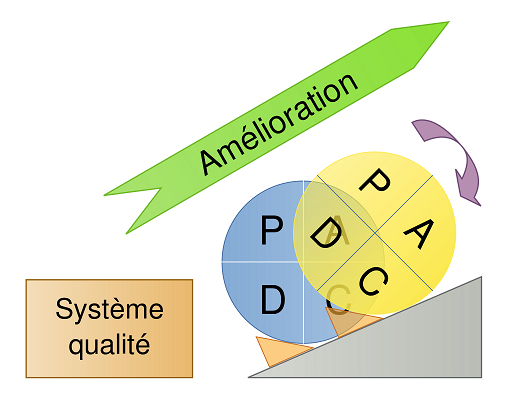
Notre processus d’industrialisation passe par plusieurs phases, mais il peut très souvent être amélioré !
En résumé
Cette partie vous a permis d’appréhender les différentes phases nécessaires à l’industrialisation d’un produit.
Le service Méthodes a, comme vous avez pu le constater, de nombreuses tâches à réaliser afin de mener à bien un projet d’industrialisation. Le schéma ci-dessous résume et synthétise les différentes actions à mener par le service Méthodes pour la réalisation d’un projet d’industrialisation.

Certaines de ces étapes, comme le développement des outillages, sont de plus en plus réalisées à l’aide d’innovations technologiques. Je vous invite à découvrir les technologies du futur ainsi que leur application dans vos futures missions dans la troisième partie de ce cours.