Bienvenue dans la deuxième partie du cours ! Maintenant que vous avez un bon aperçu de l’activité Méthodes, je vous propose de vous mettre dans une situation d’industrialisation concrète.
Vous êtes responsable méthodes de la société McQuiGame : cela vous dit quelque chose ? Eh oui, c’est le fameux restaurateur dont nous parle Cédric Facon, dans la deuxième partie de son cours "Pilotez l’amélioration continue dans l’industrie du futur" ! Pour rappel, ce restaurateur japonais souhaite diversifier son activité et se lance dans la fabrication d’un jeu de société qui consiste à fabriquer des petits sushis et makis.
McQuiGame livre un entrepôt qui gère la distribution vers les grandes surfaces et les magasins spécialisés. Vos commerciaux ont bien travaillé et ont réussi à décrocher un super contrat. Cependant, il va falloir respecter les délais de livraison, et ce avec la bonne quantité et bien sûr une qualité irréprochable.
Le client veut recevoir 1 camion par jour de 34 palettes, chaque palette contenant 54 boîtes de jeu. Il faudra donc prévoir 20 livraisons. Si vous honorez cette première commande, vous pouvez espérer en avoir d’autres rapidement.
Vous avez participé aux premières réunions de lancement du nouveau produit ; vous travaillez en mode ingénierie simultanée de manière à mieux appréhender les contraintes de chacun.
Votre équipe design a imaginé et créé les graphismes et autres images. Votre bureau d’études a étudié la faisabilité, et moyennant quelques ajustages de machines que vous allez définir, le projet est tout à fait réalisable en théorie.
Maintenant, c’est à vous de jouer !
Décidez des technologies
Voici de quoi est composé votre produit fini :
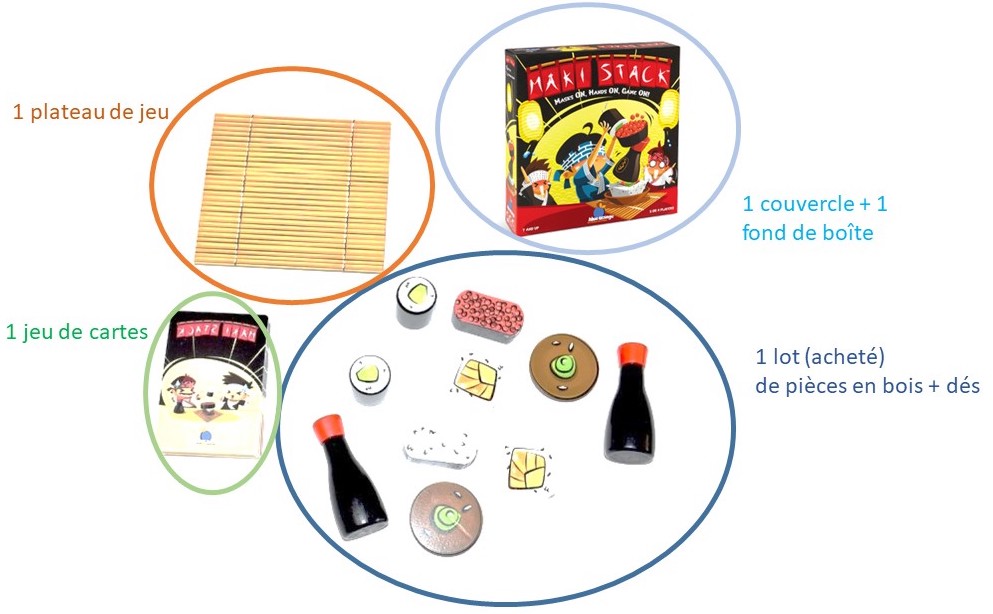
Tout d’abord, vous réfléchissez à ce qui doit être fabriqué sur site ou sous-traité. Votre cœur de métier est l’imprimerie, vous avez un excellent sous-traitant de pions et dés à 5 km de votre usine. Vous ne disposez pas de moyens industriels aujourd’hui pour fabriquer ce genre de produit, vous décidez donc sous-traiter le lot de pièces en bois et les dés.
Tout le reste du produit fini sera fabriqué en interne.
Votre commande est suffisamment importante pour envisager de la moyenne/grande série. Voici la nomenclature du produit :
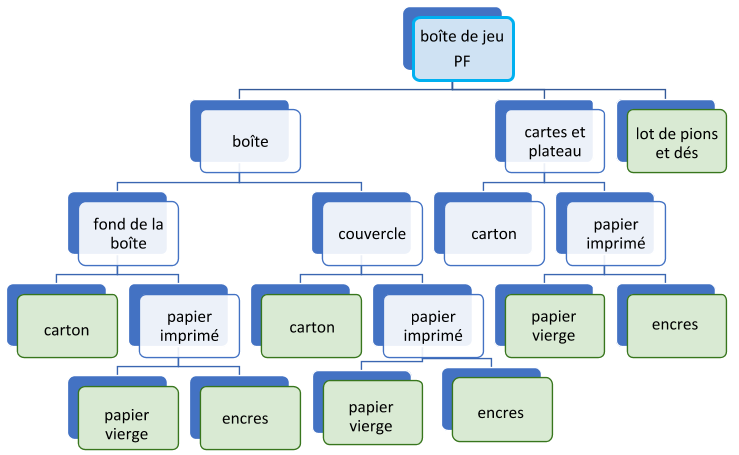
Il faut "descendre" jusqu’au niveau que nous considérerons comme "matière première", c’est-à-dire les composants que nous achèterons. Ce niveau est représenté en vert sur le schéma. Cela nous permet aussi de définir les différentes opérations pour passer d’un niveau à l’autre et de définir ainsi le process de fabrication et nos gammes de fabrication.
Nous achèterons notre matière première comme suit :
lots de pions : achat fournisseur de pions ;
rames de papier vierge : achat fournisseur de papier ;
encres et colle : achat fournisseur de produits.
S’agissant d’un type de production que nous effectuons régulièrement, nous allons pouvoir utiliser les mêmes outils industriels (machines) moyennant des adaptations d’outillage.
Notre usine dispose de :
une zone de tirage : impression sur imprimantes offset ;
une zone de punchage/poinçonnage qui prédécoupe des formes qu’il faut ensuite décortiquer manuellement ;
une zone cartonnerie/pliage où se font l’encollage et le pliage.
Nous avons donc identifié la nomenclature et les produits finis, semi-finis et la matière première. Nous avons également déterminé qu’il allait s’agir d’un process standard utilisant notre parc machine existant.
Nous allons donc passer à l’établissement du processus. Nous pouvons identifier :
l’imprimante (imprime, vernis sous poudre) ;
la plieuse colleuse ;
la machine à puncher qui prédécoupe des formes qu’il faut ensuite décortiquer manuellement ; c’est intéressant pour les produits de petite taille.
Il va à présent falloir définir le processus de fabrication de chaque composant semi-fini, puis remonter jusqu’au produit fini. Nous allons donc nous baser sur les machines existantes dans notre usine et les adapter au besoin avec des outillages.
Définissez le processus de fabrication
Détaillons les processus pour chaque élément du projet.
Fabrication de la boîte (couvercle et fond de boîte) :
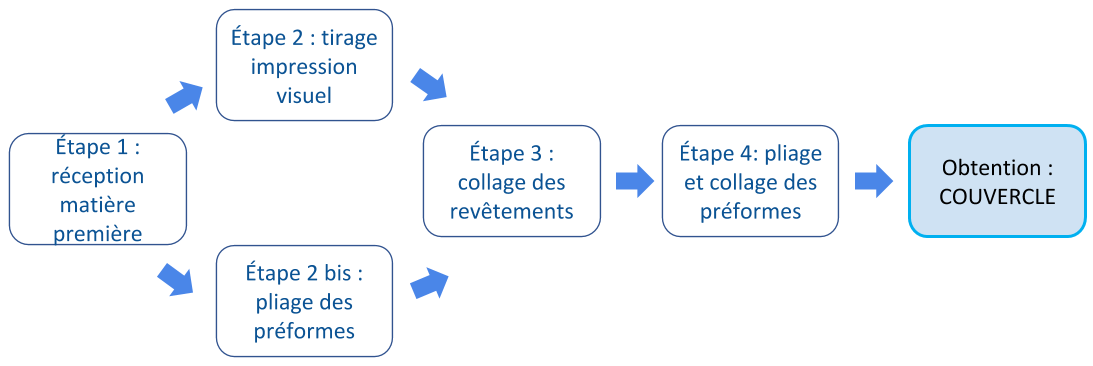
La production du fond de boîte est similaire, on passe par les mêmes étapes que pour la fabrication du couvercle. Les dimensions et la symétrie sont toutefois différentes.
Fabrication des cartes et du plateau de jeu :

Le processus sera le même pour le plateau : avec une impression du visuel et des empreintes de prédécoupe différentes. Il y a donc un changement et une adaptation d’outillage nécessaire. Une fois les produits semi-finis fabriqués, il restera à les assembler.
Le schéma qui suit synthétise et simplifie nos flux de production globale :
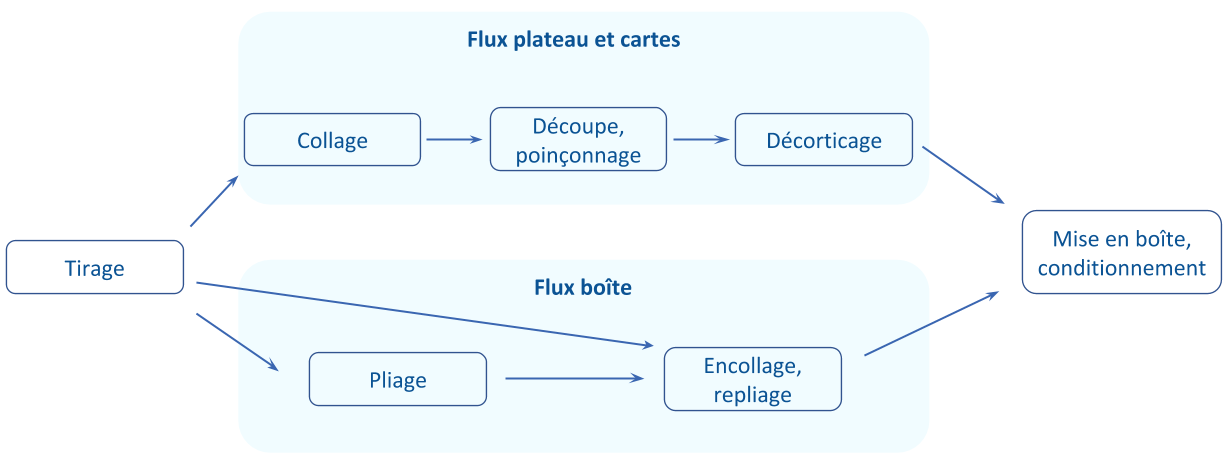
Voyons ce que cela donne en configuration "usine". Voici le flux de production :
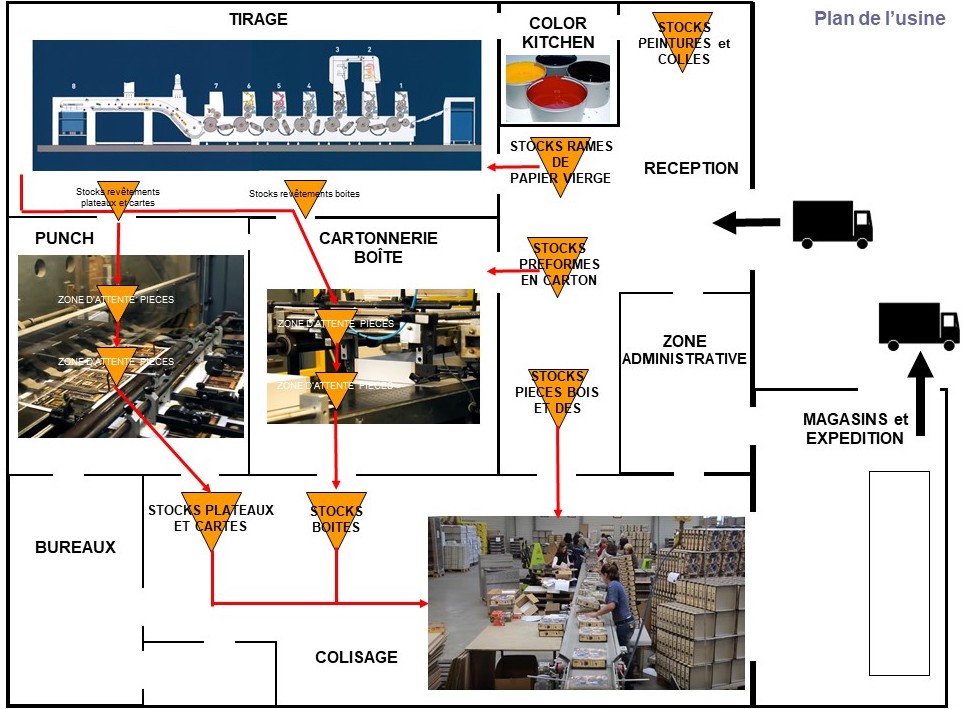
Il ne faudra pas oublier d’introduire des contrôles tout au long du processus et en fin d’étape. Nous mettrons une étape de contrôle tous les 100 tirages par le biais d’un œil optique pour vérifier les éventuelles variations de couleur.
Les autres contrôles pourront s’effectuer en sortie de processus avec un contrôle visuel et dimensionnel effectué statistiquement, surtout pour les premières productions.
Maintenant que nous avons établi nos processus de fabrication, il nous faudra les documenter. Chaque étape est accompagnée d’une gamme de travail qui devra être la plus précise possible. Généralement, une gamme comprend les informations suivantes :
le libellé ou la référence de la gamme ;
sa version ;
le produit fabriqué ;
ses dates d’application ;
des plans ou d’autres documents liés ;
les tailles de lot de fabrication, de transfert ;
des EPI éventuellement nécessaires ;
un poste de charge ou une ressource ;
des outillages nécessaires ;
des schémas ou des plans ;
un temps alloué ;
tout élément qui semble important à la réalisation de la tâche (exemple : s’assurer que l’étape d’avant a bien été réalisée).
Les gammes se doivent d’être le plus exhaustives possible, puisqu’elles servent de document de base pour les utilisateurs.
Afin de compléter nos gammes et d’appréhender au mieux nos coûts de production, il va maintenant falloir valoriser les temps.
Valorisez nos processus en temps et en coût
Reprenons notre processus de production simplifiée. Nous avons 7 principales opérations qui constituent notre processus de fabrication :
tirage ;
collage manuel ;
découpe poinçonnage ;
décorticage ;
pliage ;
encollage/repliage ;
et enfin mise en boîte/conditionnement.
Une manière simple d’évaluer le temps et d’estimer le temps à allouer à chaque opération est de chronométrer par le biais de ce que l’on nomme la « chrono-analyse ».
Avant de commencer une séance de chrono-analyse, le mode opératoire doit être parfaitement défini et les opérateurs doivent utiliser les mêmes méthodes. Le cycle doit être décomposé en sous-éléments homogènes et mesurables appelés séquences ou éléments de travail.
Chaque séquence a un top de début et un top de fin uniques qui permettent de démarrer et d’arrêter la prise de temps :

Dans notre cas, et pour ne pas alourdir les explications, nous nous intéresserons aux gros postes du processus (nous n’entrerons pas dans les sous-processus).
Pour avoir notre temps d’opération, nous devons prendre en considération :
le temps de cycle théorique (temps nécessaire à la production d’une unité) ;
le taux de rebut (pièces non conformes sur une heure) qui va se traduire par un "taux rendement", c’est-à-dire le taux de pièces conformes.
On en déduira :
la cadence réelle (en pièces par heure) ;
puis le temps de cycle réel pour le produit fini ;
et enfin, le nombre d’opérateurs pour en déduire le coût main-d’œuvre.
Exemple : poste « tirage »
Notre produit fini se compose de 4 éléments à imprimer :
le couvercle de boîte ;
le fond de boîte ;
les cartes ;
et le plateau.
Par expérience, nous savons que cette machine nécessite la présence de 3 opérateurs. On a un temps de cycle théorique de 1,8 seconde par feuille, soit 4*1,8 = 7,2 s pour notre produit fini.
Après une heure de chronométrage et à la suite du contrôle des produits réalisés, nous avons :
nombre de feuilles imprimées : 3600/1,8 = 2000 feuilles imprimées ;
nombre de feuilles bonnes : 800 ;
ce qui nous donne TR = (800/2000) * 100 = 40 %.
On a donc une cadence réelle de 800 p/h, soit une cadence de produit fini de 800/4 = 200 p/h.
On a donc un temps de cycle de 3600/200 = 18 secondes.
Le temps de changement de fabrication est de 10 min.
De cette analyse pourra découler le coût main-d’œuvre pour ce poste, en multipliant le temps main-d’œuvre par le taux horaire, puis par 3 (car il y a 3 opérateurs). Pour une heure de fabrication, nous avons en réalité un coût MO : 3 x 1 h x taux horaire en euro.
Nous effectuons les mêmes chrono-analyse et contrôle des produits en fin de chaque étape de production.
Le tableau ci-dessous synthétise les résultats des étapes de production :
| Nombre opérateurs | Tps de cycle théorique (secondes) | Changements de fabrication (min) | TR % | Tps de cycle réel par PF (secondes) |
Tirage | 3 | 7,2 | 10 | 40 | 18 |
Collage manuel | 6 | 12 | 15 | 90 | 13,3 |
Découpe/ poinçonnage | 2 | 9,6 | 180 | 50 | 19,2 |
Décorticage | 2 | 4,5 | 0 | 25 | 18 |
Pliage | 2 | 9,2 | 60 | 60 | 15,4 |
Encollage/ repliage | 4 | 9 | 10 | 80 | 11,25 |
Mise en boîte conditionnement | 8 | 12 | 10 | 80 | 15 |
Nous avons donc :
un temps de fabrication réel de : 18+1303+19,2+18+15,4+11,25+15 = 110,15 s ;
un temps de fabrication théorique de : 7,2+12+9,6+4,5+9,2+9+12 = 63,5 s.
En temps main-d’œuvre, cela donne : (3+6+2+2+4+8)*(18+13,3+19,2+18+15,4+11,25+15) = 2974 s, soit 49 min ! contre 28,6 min en théorie.
Les coûts machines sont donnés généralement par le service Finance et au niveau des méthodes, nous fournissons les temps de production... que l’on essaie d’améliorer. Vous voyez que l’on peut faire mieux ! Soyez patient, nous y reviendrons dans le dernier chapitre de cette partie.
Pour fabriquer des produits de qualité et à temps, il nous faut de la matière première de qualité. Il est donc très important d’avoir des fournisseurs fiables. Nous verrons dans le chapitre suivant comment se fait le choix des fournisseurs.