Nous avons donc une production de boîtes qui fonctionne bien en théorie ! :euh:
On a défini le process, identifié les fournisseurs, fabriqué nos outillages et même pensé à mettre des détrompeurs ! Il va falloir maintenant passer en production.
Formez les opérateurs et autres acteurs
Pour chaque nouvelle industrialisation, l’étape de formation est indispensable. Elle peut se faire de manière théorique, puis sur le terrain, ou uniquement sur le terrain s’il s’agit d’une situation purement opérationnelle.
Dans le cas d’une formation sur le terrain uniquement, je préconise tout de même de commencer par rassembler toutes les personnes à former de manière à expliquer le projet d’industrialisation, les enjeux pour l’entreprise. Chaque salarié est directement impliqué dans le développement et la vente de nouveaux produits. Il est important de communiquer sur ce sujet afin que chacun puisse adhérer le mieux possible.
Ensuite peut avoir lieu une formation sur le terrain. On peut donc vérifier que nos gammes de travail sont lisibles et compréhensibles de tous. C’est aussi l’occasion de les modifier au besoin.
Il est toujours préférable de formaliser au minimum les sessions de formation en situation de travail. N’hésitez pas à vous rapprocher de vos services Ressources humaines et Formation, qui ont généralement à disposition un modèle pour capitaliser et enregistrer les actions de formation et valider de ce fait les opérateurs sur les produits.
Prenons la gamme de travail "décorticage" : l’opérateur devra scrupuleusement la suivre et l’action devrait en théorie être réalisée parfaitement. Si les indications ne sont pas claires ou si l’opérateur hésite, c’est qu’il faut revoir la gamme.
L’opérateur doit aussi intégrer l’importance du port des "Équipements de Protection Individuels" qui doivent être mentionnés sur les documents de travail. Par exemple, le port de gants pour éviter les coupures avec le carton lors du décorticage.
Présérie
Avant de lancer une production à proprement parler, nous devons « tester » notre processus de production. Pour ce faire, nous allons lancer une présérie, c’est-à-dire une petite production qui nous permettra de vérifier que toutes les étapes de la production sont conformes.
Cela nous permet de tester :
notre matière première ;
nos documents (gammes) ;
la formation des opérateurs ;
nos machines ;
nos outillages ;
nos détrompeurs ;
et bien évidemment, la qualité de notre produit fini.
Pour résumer, c’est le résultat de tout le travail que nous avons effectué ! C’est en quelque sorte le verdict !
L’objectif est bien sûr d’avoir le produit voulu avec le moins d’arrêts et le moins de rebuts possible.
AMDEC et plans de surveillance
L’AMDEC pour Analyse des Modes de Défaillance, de leurs Effets et de leur Criticité est un outil qui permet d’évaluer les risques d’arrêt de production et/ou de rebut d’un processus.
C’est un exercice que l’on effectue collectivement en alliant des points de vue complémentaires (par exemple fabrication, conception, qualité, opérateurs). Le but est d’identifier tous les modes de défaillance, c’est-à-dire toutes les observations de dysfonctionnement tout au long du process et d’évaluer leur criticité.
Pour évaluer la criticité, nous pouvons utiliser les critères suivants :
fréquence ou probabilité d’apparition ;
gravité ;
probabilité de non-détection.
La criticité ou l’Indice de Priorité du Risque (IPR) sera le produit : C=FxGxP. Plus la criticité est élevée, plus le mode de défaillance est critique.
Prenons des exemples simples pour illustrer le système d’évaluation des critères :
Note F | Fréquence ou probabilité d’apparition | Note G | Gravité | Note D | Probabilité de non-détection |
10 | Permanent | 10 | Mort d’un homme, catastrophe environnementale | 10 | Aucune probabilité de détection |
5 | Fréquent | 5 | Conséquences financières ou économiques | 5 | Un système de détection est en place, mais n’est pas infaillible |
1 | Invraisemblable | 1 | Pas grave | 1 | Le système de détection est infaillible |
Généralement, en dessous d’une criticité de 100 (quand on cote de 1 à 10), les entreprises ne mettent pas forcément en place des actions correctives, car elles estiment que le processus n’est pas en danger.
On peut aussi présenter son évaluation sous le format ci-dessous avec le critère "Fréquence", évalué de fréquent à invraisemblable, et le niveau de gravité coté d’insignifiant à catastrophique :
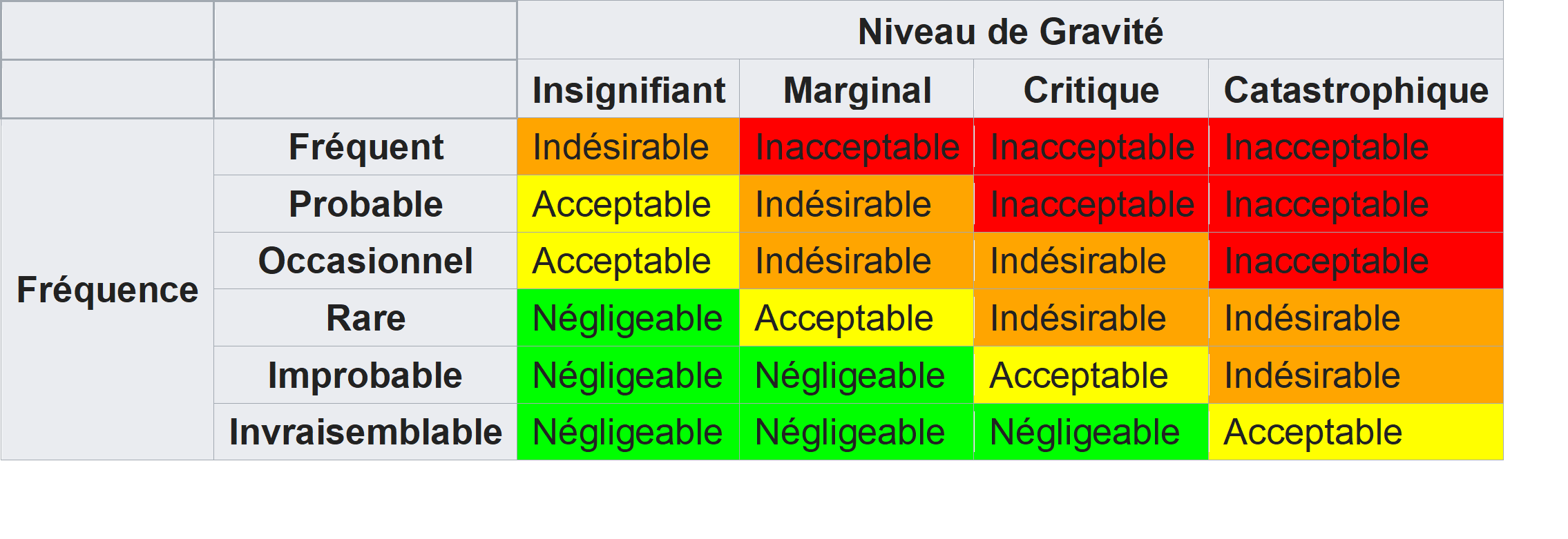
Cet outil a vraiment pour objectif d’identifier des process à risque afin d’y apporter des solutions.
Pour apporter une solution à un problème, il faut d’abord en identifier les causes. Ensuite, nous pouvons mettre en place une solution dont l’efficacité devra être vérifiée.
Si le mode de défaillance est critique, on peut envisager de mettre en place un plan de surveillance spécifique sur ce mode, c’est-à-dire une surveillance renforcée et une attention particulière pour détecter et résoudre le problème jusqu’à ce que le défaut n’apparaisse plus pendant un certain temps (jugé suffisant pour lever la surveillance).
Par exemple, si notre découpeuse tombe souvent en panne et que le constructeur préconise une maintenance trimestrielle, nous pouvons tout à fait proposer une maintenance mensuelle plus légère afin de limiter les pannes.
Le plan de surveillance sert donc à mettre sous contrôle des modes plus défaillants et à anticiper de ce fait les pannes. Cela n’exclut pas de rechercher les causes racines et de résoudre le problème.
L’analyse fonctionnelle permet de bien cibler l’AMDEC qui va mettre en évidence des modes à mettre sous contrôle via des plans de surveillance. Cela est aussi un complément de la maintenance.
Ramp-up et démultiplication du process
À la suite de la production de présérie, de l’analyse AMDEC, de la mise en place d’un plan de surveillance, notre processus de fabrication de boîtes de jeux est enfin qualifié !
Nous allons pouvoir nous lancer dans la grande série. Nous commencerons par des cadences petites et moyennes avant d’atteindre la cadence de croisière. Les premiers lots feront l’objet d’une attention plus particulière. Puis nous augmenterons les fréquences et les quantités jusqu’à atteindre graduellement notre objectif de production.
Le projet est clos quand nous nous sommes assurés que les premiers lots sont satisfaisants en qualité, qu’ils ont été produits dans les temps initialement prévus (ou retouchés en cours d’avancée du projet) et qu’il n’y a plus de retouches de gammes à faire.
Une fois la production lancée, le travail du service Méthodes ne s’arrête pas là. Passons donc au chapitre suivant pour la phase d’optimisation !