Levez le rideau sur les acteurs de la maintenance
Les figurants, premiers acteurs : les opérateurs (production)
Ce service Maintenance dont on constate maintenant les nombreuses responsabilités ne peut pas, seul, assurer toutes ses activités ! En effet, certaines machines sont sollicitées 24 h/24. Il faudrait passer quelques minutes à chaque poste pour contrôler chaque machine, comme on le ferait pour notre voiture avant un long voyage ?
Pour analyser le temps de ce contrôle par un technicien, prenons ce cas concret :
Une entreprise possède 50 machines sur 9 000 m² étalées dans 4 ateliers. Elle produit en 3 x 8. Il y a 6 techniciens de maintenance.
Le contrôle prend 5 min / machine. Le déplacement entre machines est de 20 m en moyenne. Le temps de mise à disposition de la machine par l’opérateur pour le technicien est de 5 min.
Parmi ces propositions, laquelle est correcte ? (une seule bonne réponse)
Il faut 2 heures à un technicien pour assurer ce contrôle.
Il faut un demi-poste de technicien.
Il faut détacher un technicien à temps complet pour chaque poste de 8 h.
Il faut deux techniciens à temps complet pour chaque poste de 8 h.
Réponse : Il faut détacher 1 technicien par poste dans le meilleur des cas (3e réponse).
(5 min de contrôle + 5 min pour les aléas) x 50 machines = 500 min de temps de contrôle.
(20 mètres x 50 machines) à une vitesse de déplacement de 5 km/h = 12 minutes de déplacement.
Temps total = temps de contrôle + temps de déplacement
500 + 12 = 512 min soit 8,5 h.
Donc il risque même de bâcler le travail avec 7,5 h effectives en poste...
Cela représente 3 techniciens embauchés uniquement pour des contrôles quotidiens basiques ! Chaque opérateur passera 1 % de son temps en contrôle de base quand la maintenance y consacrerait 50 % de son effectif.
Par conséquent, la maintenance a besoin de déléguer une partie de son activité aux opérateurs. La production est donc un acteur capital ! Les opérateurs sont de fait affectés à la maintenance 1er et 2e niveaux :
Niveaux | Actions | Outils |
Niveau 1 |
| Modes opératoires Outils de nettoyage |
Niveau 2 |
| Modes opératoires Outils de démontage Pièces de rechange à proximité gérées par la maintenance |
L’acteur principal : les techniciens (maintenance)
Le technicien, lui, joue plusieurs rôles :
diagnostiqueur ;
réparateur polyvalent : électricien, mécanicien, automaticien ;
planificateur ;
méthodiste ;
gestionnaire de stock.
Mais paradoxalement, il est le plus illustre lorsqu’il se fait discret. Moins on le voit, plus il est efficace ! Son rôle consiste à tout anticiper pour éviter d’apparaître sur scène.
Il est affecté à la maintenance de 3e et 4e niveaux :
Niveaux | Actions | Outils |
Niveau 3 (technicien) |
| Outillage complet Appareils de mesure et de diagnostic GMAO |
Niveau 4 (équipe technique) |
| Idem Autres moyens spécialisés |
L’acteur précieux : le constructeur
Il joue un rôle spécifique :
Niveau | Actions | Outils |
Niveau 5 |
| Spécifiques au constructeur |
Maintenant que les acteurs sont désignés, choisissons le scénario. Ils sont nombreux et pas tous de la meilleure qualité !
Optez pour le bon scénario
Maintenant que les acteurs sont placés, il faut choisir le bon scénario !
En effet, il existe plusieurs politiques de maintenance :
la maintenance corrective : c’est le scénario le plus simple, sans besoin de talent, il est vite appris mais risque de laisser le public sur sa faim, désenchanté voire très mécontent ;
la maintenance préventive : ce scénario est éblouissant, mais il demande un gros investissement des acteurs et un engagement sans faille. Celui-ci va émerveiller le public ;
vous pouvez aussi opter pour des scénarios intermédiaires, plus ou moins brillants...
Nous allons détailler ces scénarios dans ce chapitre. Commençons par les scénarios les plus nuisibles pour l’entreprise. Ceux qui rendent le public de la production très mécontent !
La maintenance corrective : le pompier entre en scène
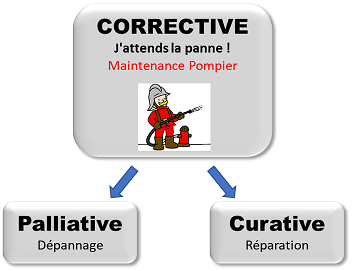
La maintenance palliative
Ce type de maintenance est la plus coûteuse sur le long terme, mais aussi la plus simple à mettre en place. Elle engendre une spirale infernale :
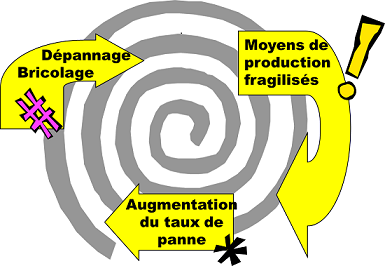
La conséquence de ce type de maintenance est la dégradation accélérée de l’équipement. Ce graphique représente les courbes de dégradations naturelles des composants d’une machine en fonction du temps :
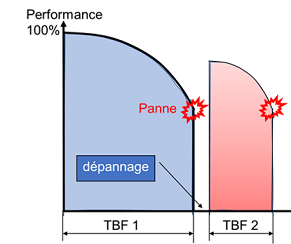
Pour ce graphique :
TBF 1 : le composant est monté neuf et fonctionne jusqu’à sa casse ;
TBF 2 : le composant n’est pas remplacé, mais une action palliative l’a remis en service.
Pourquoi a t-on recours au dépannage ?
Parce que le temps de dépannage est court. L’objectif est de redémarrer au plus vite. On privilégie le court terme.
Il se peut aussi qu'on ne possède pas de pièces de rechange.
Sur les courbes de dégradation, le TBF 2 est nettement plus court que le TBF 1. Pourquoi ?
Le palliatif n’élimine pas la cause de la panne, mais pallie le problème provisoirement. Le composant n’est pas remplacé, ou la cause de la panne n’est pas éliminée. L’équipement ne revient pas à son niveau de performance initial.
Par exemple, remplacer une roue crevée par une roue de secours. C’est de la maintenance de niveau 1 ou 2. La cause de la panne n’est pas éliminée, mais la conséquence est nettement plus supportable grâce à une mesure de secours.
Dans ce cas, la maintenance doit gérer, elle-même, un stock de consommables à proximité du poste de travail pour éviter des pertes de temps à l’opérateur.
Parmi ces exemples, quels sont ceux qui sont des mesures de secours dans un véhicule ? (plusieurs réponses possibles)
Pare-brise feuilleté.
ABS.
Ceinture de sécurité.
Climatisation.
Airbag.
3e feu stop.
Habitacle indéformable.
Renforts latéraux.
Réponse : 1, 3, 5, 7, 8.
Les mesures de secours permettent de réduire la gravité de l’effet de l’accident, mais ne l’évitent pas.
La maintenance curative
Il s’agit d’éliminer la cause première de la panne par un diagnostic et le remplacement éventuel de la pièce incriminée. Cela nécessite une gestion de stock judicieuse : ni trop de stock, ni rupture.
Le temps de réparation est plus long, mais le TBF de la pièce remplacée sera équivalent à sa valeur de départ, car la pièce est neuve.
Parmi ces propositions, quelle est celle qui définit le coût d’une intervention de maintenance corrective ? (une seule réponse possible)
Temps de correctif x taux horaire technicien + Prix des pièces de rechange.
Temps de correctif x taux horaire technicien + Temps de correctif x taux horaire opérateur inoccupé.
Temps de correctif x taux horaire technicien + Temps de l’arrêt x taux horaire opérateur inoccupé + Prix des pièces de rechange + Temps de l’arrêt x taux de pertes de production.
Temps de correctif x taux horaire technicien + Temps de correctif x taux horaire opérateur inoccupé + Prix des pièces de rechange + Temps de correctif x taux de pertes de production.
Réponse 3 : dans cette équation, le coût de pertes de production est largement supérieur aux autres.
Mais, vous l’avez compris, notre client, la production, n’a que faire des pompiers. Il ne veut voir personne perturber son activité !
C’est pourquoi il faut passer à la maintenance préventive !
La maintenance préventive
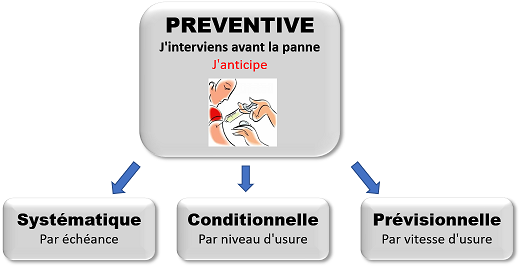
Le préventif systématique
Le préventif systématique, c'est comme un carillonneur qui revient sur scène à intervalle régulier, pour vous avertir de remplacer la pièce usée par une neuve. Le plus souvent, ses alertes sont déclenchées au bout d’une période temps définie. Mais ce peut être aussi après un nombre de pièces fabriquées, de cycles ou de km. La vidange d’un moteur est un cas classique de préventif systématique défini dans le carnet d’entretien du constructeur.
Comment obtenir cette échéance concrètement ?
Méthodes d’obtention des échéances | Avantages | Inconvénients |
Consignes constructeur | Simple | Ne tient pas compte des contraintes spécifiques de production : milieu agressif, efforts mécaniques, bourrages… Dossiers parfois inexploitables ou manquants |
Expériences des techniciens | Réaliste. En rapport avec les contraintes de production | Peut être coûteuse si le technicien prend en compte la durée de vie la plus courte |
Calcul de la moyenne de temps de bon fonctionnement (TBF) | Réaliste. En rapport avec les contraintes de production. Bonne précision | Nécessite une bonne traçabilité des interventions correctives : date, pièce remplacée, cause… |
Méthode par la loi de Weibull | Très précise | Méthode plus complexe |
Méthode de la MTBF : Moyenne des TBF, temps de bon fonctionnement.
Prenons un exemple, la pièce défaillante de la machine tombe en panne en moyenne toutes les 29 h.
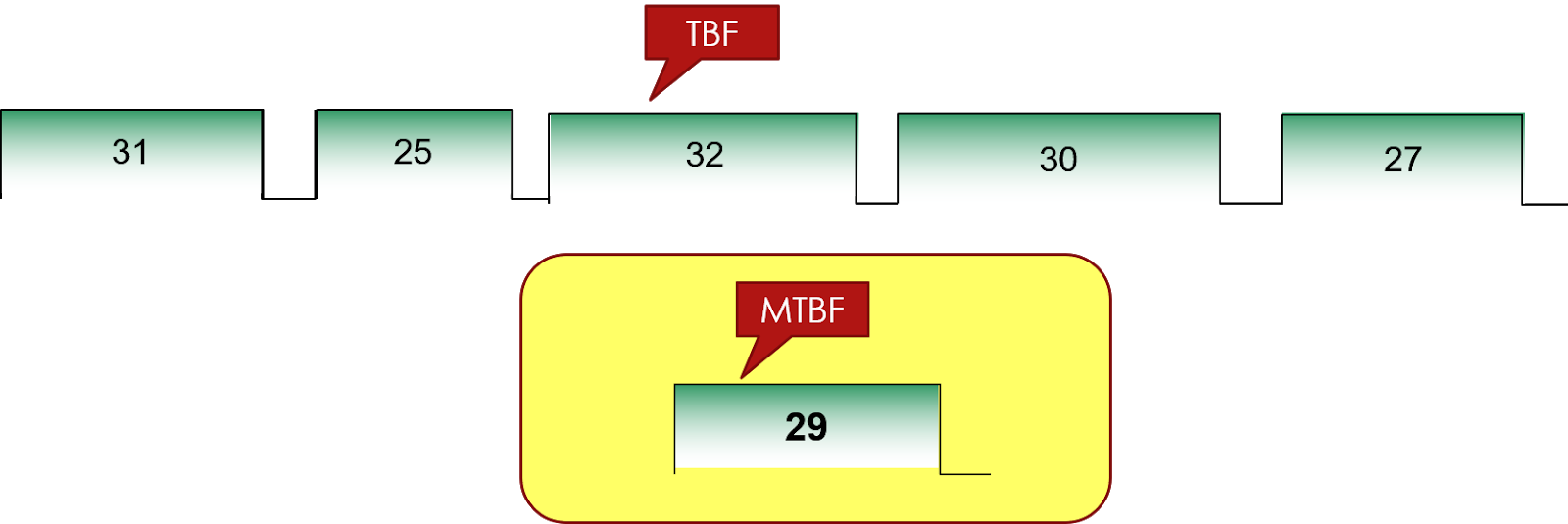
L’objectif est de remplacer la pièce avant sa MTBF, soit 29 h dans ce cas.
De façon générale, l’échéance de remplacement d’une pièce usée est : k x MTBF, avec k un coefficient entre 0, 5 et 1. Plus on s’approche de la MTBF, plus le risque d’apparition de la panne est grand.
Qu’allez-vous gagner avec le préventif systématique, par rapport au correctif ?
Pour le comprendre, il faut penser que les pannes d’une machine ne tombent pas obligatoirement après le même temps de fonctionnement. Il faut donc avoir recours… aux statistiques !
Admettons que la distribution statistique des pannes suive une loi normale dont la moyenne est la MTBF. Cette loi donne la répartition des fréquences d’apparition des pannes, en fonction de la durée de fonctionnement de la machine ou de la pièce.
Prenons le cas où nous avons un écart type de 20 h et d’une étendue de 260 - 140 = 120 h. La durée de vie sans panne la plus courte recensée dans la GMAO est de 140 h, soit moins de 6 jours en moyenne, et la plus longue de 11 jours. La plus grande fréquence d’apparition des pannes se situe autour de la moyenne des temps de fonctionnement, c’est-à-dire la MTBF :
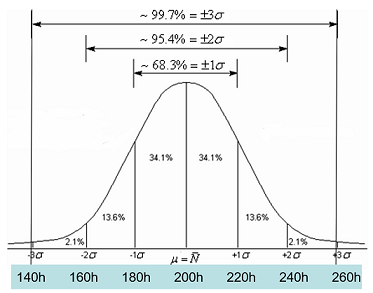
La machine fonctionne en 3 x 8 h pendant 300 j / an.
Avec une MTBF de 200 h et un écart type de 20 h, quel est le risque en % de tomber en panne si :
la pièce la plus fragile est remplacée toutes les 200 h ?
la pièce la plus fragile est remplacée toutes les 160 h ?
Réponse :
À t = MTBF = 200 h, on aura eu 50 % de risque d’avoir déjà eu une panne.
À t = 160 h, on aura seulement 2,1 % de risque d’avoir eu une panne.
On constate qu’en moyenne une panne provoque 100 € de coût direct et 400 € de coût indirect.
Quel serait le coût annuel prévisible de correctif ?
Réponse :
La machine tombe en panne au bout de 200 h en moyenne. Il faut chercher le nombre de pannes par an (soit une toutes les 200 h), et le multiplier par le coût total de 500 € :
[(300 j x 3 x 8 h) 200 h] x (100 € + 400 €) = 18 000 €.
Dans le cas où vous remplacez préventivement la pièce usée à 160 h par une pièce neuve, quel est le coût de maintenance sachant que, au cours du préventif, vous pouvez supprimer le coût indirect en intervenant hors production, et que le coût de remplacement est de 100 € ?
Réponse :
Calcul du coût de préventif avec un risque de 100 - 2,1 = 97,9 %
([(300 x 3 x 8 h) 160 h] x 100 €) x 0,979 = 4 405 €
Calcul du coût de correctif avec un risque de 2,1 %
([(300 x 3 x 8 h) 160 h] x 500 €) x 0,021 = 472 €
Coût total annuel
4405 + 472 = 4877 €, soit près de 4 fois moins cher que le correctif !
Vous venez de découvrir une première source de profit de la maintenance ! L’inconvénient de cette méthode, c’est le remplacement sans réfléchir de pièces qui peuvent sembler encore en bon état. En les remplaçant à 160 h, les pièces capables de tenir 260 h sont seulement à 62 % de leur durée de vie ! Nous pouvons donc aller encore plus loin.
Le préventif conditionnel
Pour réduire les coûts de remplacement systématique, il faut installer des capteurs capables de mesurer l’usure de la pièce. Et ainsi la remplacer au dernier moment.
Dans l’exemple ci-dessus, vous pouvez constater que 50 % des pièces dépassent les 200 h de fonctionnement, alors qu’elles vont être remplacées à 160 h ! C’est un coût superflu qui peut être éliminé à condition (on parle de préventif conditionnel) de détecter l’usure.
Prenez un roulement vital pour une ligne de production, coûteux et difficile d’accès. Son coût indirect est élevé, c’est pourquoi le préventif est privilégié. Si le coût direct est également élevé, il vaut mieux opter pour la méthode conditionnelle.
Comment trouver le capteur adéquat ?
Avant de lire la suite, prenez un instant pour lister les types d’usure possibles sur une machine.
Paramètres d’usure | Capteur | Fiable et peu coûteux > Choix |
Bruit | Sonomètre | D’autres bruits peuvent être captés > Non |
Jeu | Pied à coulisse | Pas d’intérêt, il faut démonter le roulement > Non |
Surcharge mécanique | Ampèremètre | D’autres surcharges mécaniques peuvent perturber le signal > Non |
Vibrations | Accéléromètre | Trop coûteux et avec un besoin de compétences > Non |
Chauffe | Thermostat | Fiable et peu coûteux > Oui |
Il suffit de calibrer le thermostat au seuil de température maximum admissible pendant le fonctionnement du roulement.
Quel est le gain du préventif conditionnel par rapport au systématique ?
Reprenons l’exemple précédent : une machine fonctionne en 3 x 8 h pendant 300 j / an, avec une MTBF de 200 h et un écart type de 20 h.
Grâce à un certain nombre de capteurs, vous êtes alerté des risques de pannes dans une plage de 140 h à 260 h suivant la distribution Normale de l’historique des pannes, donc en moyenne à 200 h.
Vous remplacez les pièces concernées, en temps masqué (hors production), avant qu’elles ne provoquent une perte de production.
Coût indirect = 0 € ; coût direct = 100 €.
Quel est le nouveau coût de maintenance avec ce préventif conditionnel ? Quel est le gain ?
Réponse :
L’ensemble des pièces a une durée de vie moyenne de 200 h sans panne. Elle sont remplacées juste avant leur panne entre 140 h et 260 h, soit en moyenne à 200 h.
([(300 x 3 x 8 h) 200 h] x 100) = 3 600 €
Le gain est de : 4 877 - 3 600 = 1 277 €, soit ¼ du coût du systématique.
Bilan des coûts comparés :
CORRECTIF | SYSTÉMATIQUE | CONDITIONNEL |
18 000 € | 4 877 € | 3 600 € |
100 % | 27 % | 20 % |
Bravo ! Vous avez réussi à faire 80 % d’économie tout en fiabilisant la machine.
Vous procédez en suivant ces étapes : Démontage - Relevé d’usure - Tracé de la courbe d’usure - Décision de remplacement - Remontage éventuel.
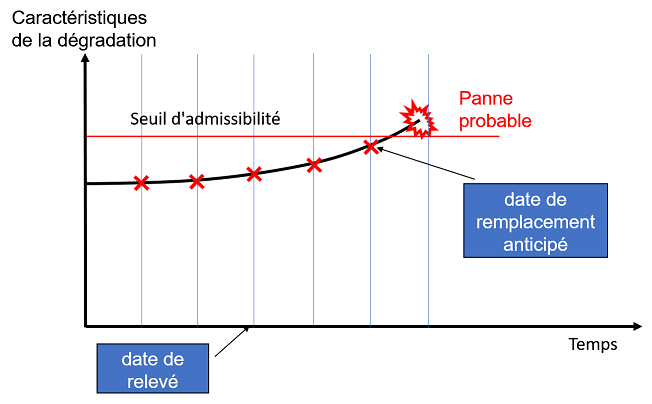
Par anticipation, vous prévoyez la date à laquelle l’usure dépassera le seuil d’admissibilité. Et vous remplacerez la pièce avant la panne et au dernier moment.
Le préventif prévisionnel ou prédictif
C’est un dérivé du conditionnel. L’objectif est de pouvoir maîtriser la date ultime de remplacement de la pièce d’usure.
Par exemple, vous constatez une alerte du circuit de freinage ou de la température du moteur sur votre tableau de bord. Quel est votre délai pour réparer ? Inconnu ! Mais il faut faire vite.
Dans l’industrie, sur vos machines, si vous remplacez vos capteurs “tout ou rien” par des analogiques, vous pourrez enregistrer et visualiser la progression de la dégradation. Et ça change tout : moins de stress, moins d’urgence. Vous pratiquerez une maintenance “intelligente” et peu coûteuse à long terme, mais plus complexe et longue à mettre en place.
Les scénarios sont bouclés. Vous avez fait votre choix. Mais avant de lancer aux acteurs “Action !”, vérifiez bien que vos acteurs aient tous leurs accessoires.
Faites le bilan de vos accessoires
La démarche 5S
Il faut voir la démarche 5S, ou O-R-D-R-E, comme un escalier de 5 marches :
1er S | Ôter l’inutile | Débarrassez-vous de tout ce qui encombre depuis longtemps, ce qui ne sert plus, ce qui traîne dans les coins, les armoires, les PC. Soyez sûr de vous. Ne jetez pas ce qui sert rarement à d’autres. |
2e S | Ranger | Chaque ustensile utile doit avoir une place définie ; sinon, créez-la et marquez-la. 20 % des objets nous servent 80 % du temps. Rangez-les près de vous. |
3e S | Décrasser Détecter | C’est le moment de faire le “grand ménage” du sol au plafond, sous et sur les machines. Apprenez aux opérateurs à détecter les anomalies techniques pendant le nettoyage, et à les signaler ou les supprimer : déchets, casses, dégradations, éléments manquants... |
4e S | Rendre évident | Pour être efficaces, les actions 5S doivent être un réflexe pour tous les participants. Utilisez le management visuel, les codes couleurs, les standards de nettoyage, de rangement, le fléchage. |
5e S | Être respectueux | Évaluez l’évolution de l’état de l’atelier avant et après le 5S, par un audit interne noté selon une grille de critères pour chaque S. Définissez un planning d’audits. Respectez rigoureusement ce planning. Diffusez vos résultats pour donner envie. |
Le 5S est un excellent accessoire pour la maintenance. En effet, une panne n’arrive jamais sans prévenir. Elle est provoquée par l’imbrication de 30 causes de micro-arrêts, eux-mêmes issus de quantités d’anomalies :
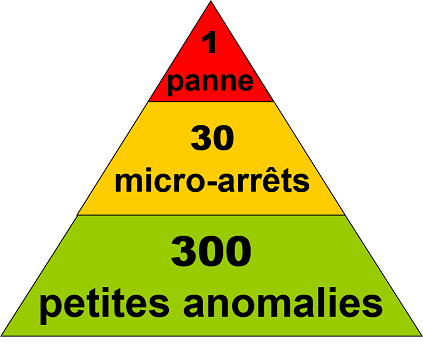
Les anomalies sont des petites fuites, des rayures, des bavures, des sifflements, des crasses… Rien qui n’empêche de fonctionner. En s’accumulant, elles provoquent des micro-arrêts que l’opérateur gère par du palliatif. S’il ne les comptabilise pas par bâtonnage, la maintenance n’en saura rien. Et la panne tant redoutée survient “tout naturellement”.
Le 5S, et particulièrement le 3e S, attaque la base de la pyramide de manière simple et indolore.
Apprenez au personnel de production et de maintenance à communiquer pour mémoriser, analyser et améliorer :
les anomalies, par des étiquettes sur les anomalies observées ;
les micro-arrêts, par le bâtonnage des causes de micro-arrêts ;
les pannes, par des demandes de travaux écrites.
Développez la MN1
La maintenance niveau 1, la MN1, s’intègre dans le principe du 5S. Ce sont des standards de contrôles quotidiens des organes vitaux de la machine. Faites-les concevoir par des équipes de maintenanciers et d’opérateurs, à l’aide des dossiers machine. La périodicité d’application de la MN1 ne doit pas excéder la semaine.
Veillez à répondre aux questions QQOQC pour remplir correctement votre fiche de contrôle MN1 (cliquez ici pour afficher l'image) :
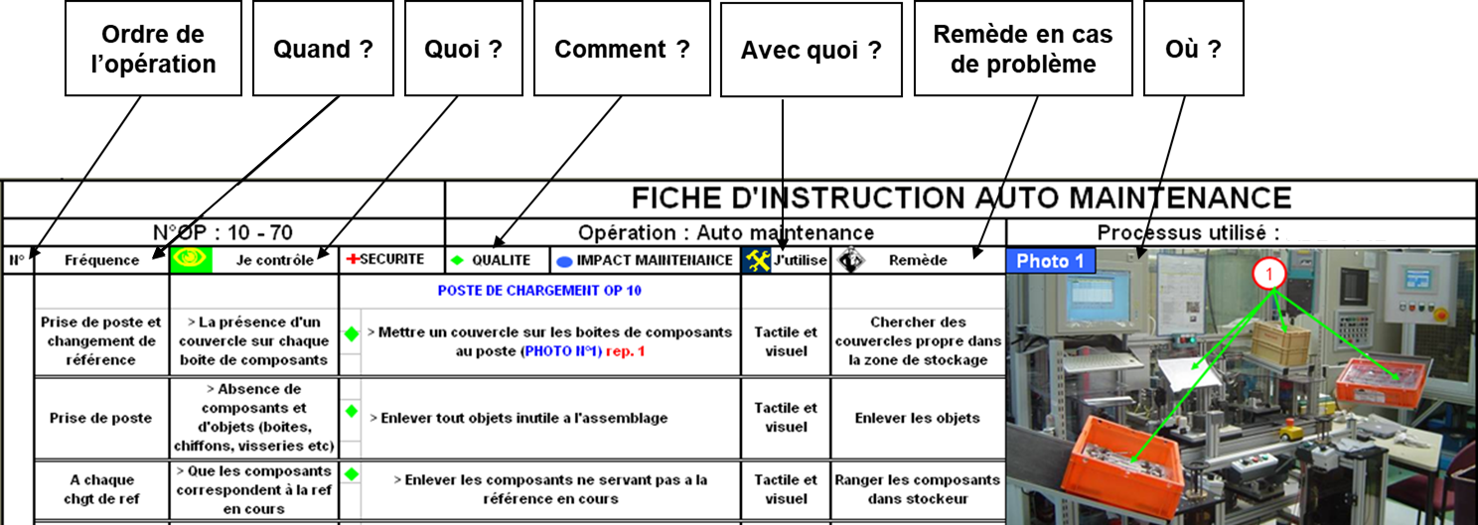
Standardisez le nettoyage (cliquez ici pour afficher l'image) :
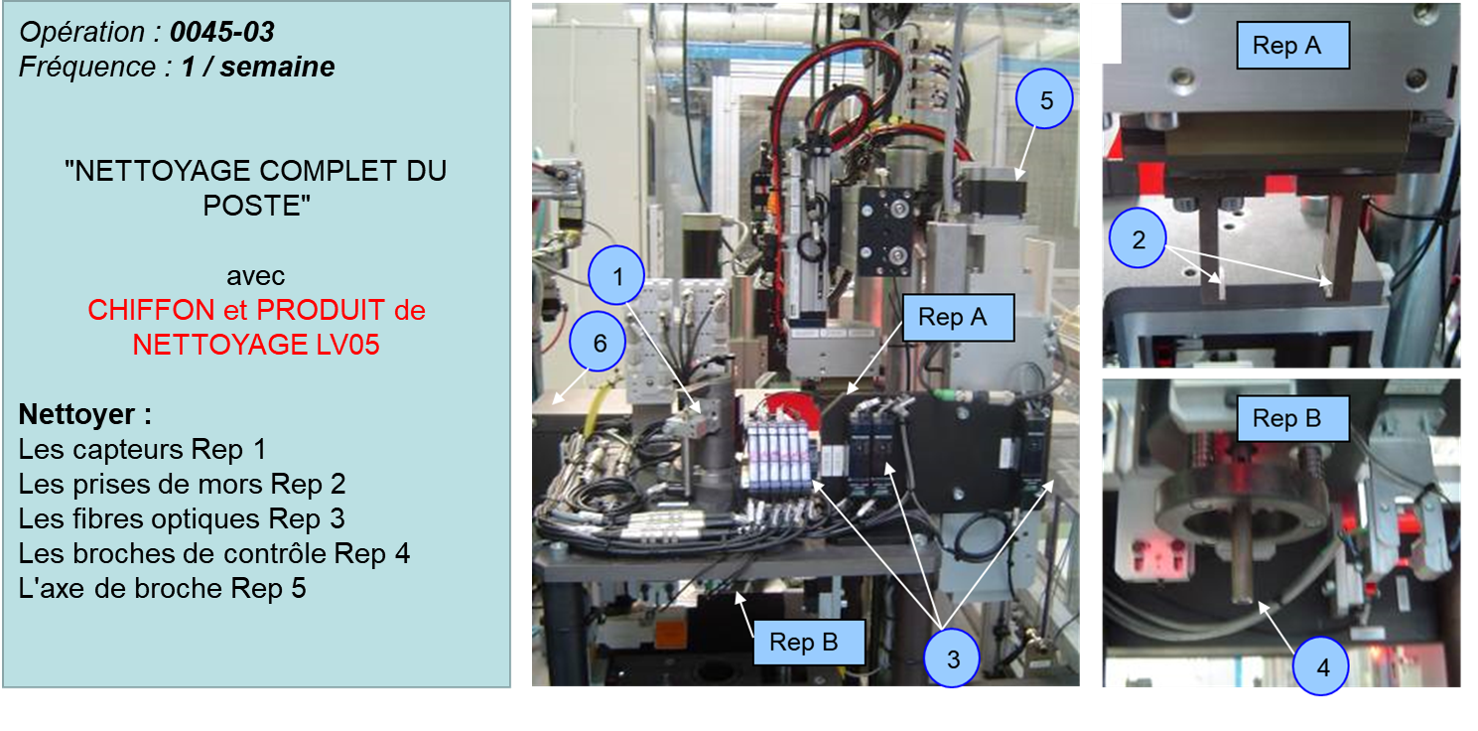
Facilitez le diagnostic pour les opérateurs
L’objectif est toujours de gagner du temps ! Plutôt que d’appeler le technicien pour un oui ou pour un non, demandez-lui de préparer un organigramme de dépannage simple. Il ne sera appelé qu’après une routine de contrôles, sans succès, réalisées par l’opérateur.
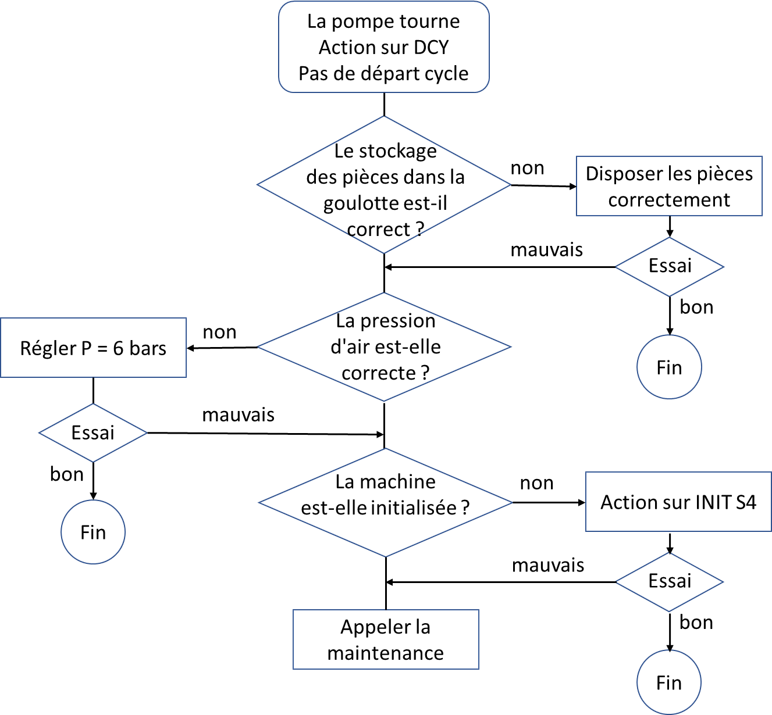
Organigramme de dépannage du départ cycle (DCY)
Que doit faire l’opérateur s’il constate une pression de 4 bars ?
Que doit faire l’opérateur s’il constate que la machine n’est pas à l’état initial ?
Réponses :
Régler le régulateur de pression à 6 bars.
Appuyer sur le bouton S4.
Vous avez maintenant une idée claire de vos moyens d’action, et vos acteurs sont prêts pour entrer en scène. Il est temps de connaître l’état de votre parc machines, sa performance, son rendement. Contrairement à ce que vous pensez, cette évaluation est très simple. Pour cela, rendez-vous dans le chapitre suivant.
Vous avez découvert les différentes politiques de maintenance et lesquelles privilégier. Passons aux indicateurs qui permettent de mesurer la performance du parc machine !