La maintenance en France génère annuellement 21 milliards d'euros de dépenses dans l'industrie (2,3 % de la production en valeur), dont 7 milliards d'euros sous-traités et 12 milliards dépensés en produits et composants industriels en maintenance et travaux neufs. La maintenance industrielle, c’est 213 000 salariés dans tous les secteurs de l'industrie, 20 000 recrutements par an, dont 70 % au niveau techniciens et agents de maîtrise. Cela donne le vertige et permet de mieux comprendre les enjeux de la digitalisation !
Les 4 métiers « qui montent » sont : techniciens de maîtrise de maintenance d'équipements industriels, agents de maîtrise de maintenance d'équipements industriels, techniciens méthode en maintenance, techniciens de maintenance de parc éolien. Le premier retour sur investissement qu’attendent les industriels en s’équipant 4.0 est celui de la maintenance (pour 66 % des interrogés).
Dans l’usine du futur, la maintenance est donc le premier service impacté ! Découvrons quelques-unes de ces innovations.
Qu’est-ce que la fabrication additive va apporter à la maintenance ?
La maintenance a régulièrement besoin de fabriquer des pièces pour remplacer une pièce cassée, pour reconcevoir une pièce d’origine mal dimensionnée ou pour compléter son stock. Aujourd’hui, ces besoins sont souvent sous-traités chez un usineur, ce qui allonge les temps d’arrêts de la machine et pousse la maintenance à les “bricoler”, avec le risque de dégrader les performances de la machine dépannée. Posséder, dans son atelier, des machines capables de fabriquer des pièces sur mesure est un atout déterminant pour la maintenance et pour l’usine.
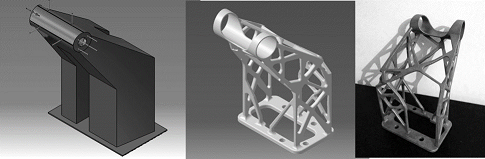
La fabrication additive est un procédé de fabrication de pièces en volume, par ajout ou agglomération de matière. Un concepteur dessine l'objet 3D grâce à un outil CAO. Le fichier 3D obtenu est traité par un logiciel spécifique, qui organise le découpage en tranches des différentes couches nécessaires à la réalisation de la pièce. Le découpage est envoyé à l'imprimante 3D qui dépose ou solidifie la matière couche par couche, jusqu'à obtenir la pièce finale.
Les matières travaillées sont le plastique, le métal (aluminium, acier, titane, platine), les céramiques et même le verre.
Les techniques qui permettent de travailler le plastique et le métal sont les suivantes :
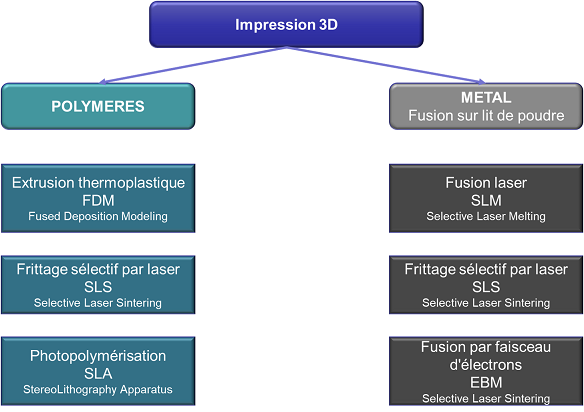
L’intérêt du 3D en maintenance
Ces procédés permettent d’envisager une véritable révolution en maintenance pour la création de pièces détachées, de supports de composants, la fabrication rapide de pièces cassées, la réalisation de prototypes industriels, la microproduction :
rapidité d’obtention ;
gain de poids des pièces fabriquées, jusqu’à 60 %, ce qui permet de prévoir un allègement global de plus de 20 % ;
réduction du nombre de pièces à assembler par soudure de près de 90 % avec pour impact, entre autres, une amélioration de la fatigue au vieillissement des pièces ;
possibilité d’intégrer dès la fabrication des tubulures internes, et de faciliter les échanges thermiques et le passage de fluides divers ;
possibilité de réaliser des pièces unitaires et spécifiques (telles que de l’outillage), permettant d'accroître l’agilité de l’entreprise, ainsi que des gains de production de plus 6 mois par rapport à des procédés classiques ;
mais surtout, la fabrication additive permet d’envisager des pièces qu’il n’était tout simplement pas possible de réaliser par des moyens traditionnels !
Les compétences nécessaires
La fabrication additive, notamment métallique, nécessite donc de mobiliser un nombre très important de compétences et de connaissances :
connaissance des différentes technologies à disposition ;
connaissance approfondie des sciences des matériaux ;
conception innovante pour la fabrication additive ;
maîtrise des processus de sécurité et de protection des biens, des personnes et de l’environnement ;
maîtrise des machines.
Les machines intelligentes
On entend par machines intelligentes, les équipements capables d’intégrer des informations et de les utiliser, afin de répondre à une fonction donnée. La complexité des informations et des besoins traités qualifient le degré d’intelligence de l’équipement.
Parmi les fonctions ainsi spécifiquement traitées sont répertoriées :
l’adaptation rapide au changement de production : flexibilité au produit et au volume, polyvalence, modularité (par rapport à la SMED vue dans la partie 1 du cours) ;
la capacité à réaliser plusieurs opérations ;
la communication entre équipements ;
l’optimisation de cycle de vie de l’équipement ;
l’optimisation de l’interface ou interaction opérateur ;
l’optimisation de consommation d’énergie et matière ;
les boucles d’autoadaptation ;
la capacité de s’adapter à son contexte pour garantir la sécurité de son action.
Ces équipements intègrent des aspects mécanique, électronique et informatique. Il en existe plusieurs familles :
robots collaboratifs, y compris cobots ;
équipements multifonctions ;
équipements pilotés à distance ;
machines de fabrication additive, y compris les imprimantes 3D ;
machines autoadaptatives.
Les enjeux et avantages des machines intelligentes
Encore une fois, l’enjeu est l’adaptation à la fois à la demande, à l’environnement et à l’évolution du process avec agilité ; la machine intelligente permet d’automatiser/moderniser les process industriels, en se positionnant au service de l’homme.
Sur le plan technologique, la machine intelligente permet :
l'intégration des réseaux de capteurs, des réseaux de machines et des opérateurs :
gestion des flux,
gestion reconfigurable, optimisée en temps réel des tâches homme-machines,
usine collaborative et mobile : perception, connectivité ;
la capacité à s’adapter, tout en conservant un environnement de sécurité (optimisation des fonctions de sécurité des machines : temps de réponse des contrôleurs de sécurité, distances d’arrêt de sécurité, utilisation sûre des données de localisations… ; capteurs de localisation) ;
les opérations de contrôle : moyens de mesure multispectraux permettant d’identifier en temps réel l’ensemble des métriques liées aux contraintes de l’environnement industriel, pour ne pas pénaliser les performances de la production ;
les opérations de contrôle : systèmes de reconnaissance de mesure et de pilotage en temps réel ;
la capacité à traiter et utiliser les informations afin de répondre à une fonction de correction ordonnée : de la fonction d’avertissement et/ou de constatation vers la fonction de « correction » en temps réel du process (mise en oeuvre d’une action corrective en temps réel).
Sur le plan numérique, la machine intelligente permet :
des équipements de production plus « communicants » : meilleures capacités d’échanges et de traitement des informations ;
une communication systémique avec les lignes de fabrication ;
de meilleures interconnectivité des équipements de production et interaction machine-machine ;
une acquisition des données en temps réel ;
un reparamétrage automatique de l’équipement et une activation automatique de l’outillage.
Sur le plan économique :
flexibilité, polyvalence, gain de temps, confort de l’homme ;
gain de productivité sur le process ;
maintenance prédictive et usine autoréparatrice, correction en temps réel du process ;
capacité à développer des pièces plus complexes et qualitatives.
Sur le plan de la transformation de l’entreprise :
manufacturing avancé ou gestion optimisée de la production industrielle ;
management en mode réseau.
Sur les plans environnemental et sociétal :
diminution de la pénibilité, baisse des TMS ;
cohabitation homme-machine, coaction homme-machine ;
écoconception renforcée des procédés, utilisation plus efficace des ressources et de l’énergie, conception intégrant toutes les phases de la vie de l’usine.
Réalité virtuelle et réalité augmentée
Qu’est-ce que la réalité virtuelle ?
La réalité virtuelle consiste à reproduire artificiellement une expérience sensorielle, qui peut inclure la vue, le toucher, l'ouïe et même l'odorat. Elle permet d'une part à l’utilisateur d’être pleinement immergé et de réaliser diverses simulations de la réalité, mais aussi, d'autre part, de préparer et d'entraîner les techniciens avant qu'ils interviennent sur l'installation. C’est l’outil idéal pour une télémaintenance.
Les moyens peuvent être des CAVE (Cave Automatic Virtual Environment : projections stéréoscopiques 3D sur 3 à 5 faces d’un cube), des murs d’immersion, des casques, voire des systèmes plus complexes. Différents moyens informatiques existent pour le développement des contenus, tels que Unity, par exemple, qui est aujourd’hui le logiciel le plus utilisé et par ailleurs gratuit. Cependant, l’usage de ce type de logiciel nécessite des compétences en développement informatique. Son utilisation est donc limitée à des ingénieurs lors de cas d’usages industriels.
Ces logiciels permettent la visualisation directe de maquettes 3D, voire la superposition de simulations techniques et scientifiques avec la machine “réelle” :
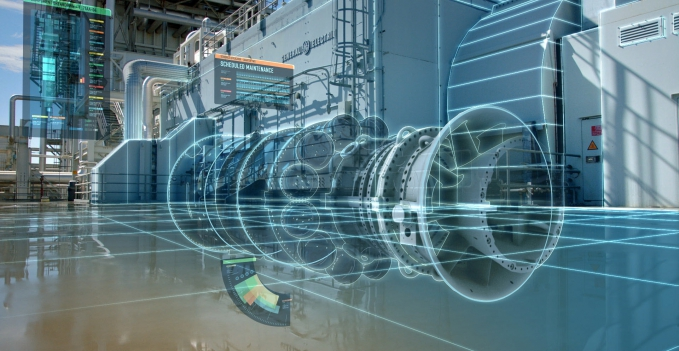
Qu’est-ce que la réalité augmentée ?
Contrairement à la réalité virtuelle, la réalité augmentée permet d’ajouter des informations dans notre champ visuel. En superposition au monde réel, des visuels se juxtaposent à l’environnement visible. Par exemple, pour des opérations de maintenance : en pointant un équipement avec un outil de réalité augmentée, les procédures adéquates vont apparaître dans le champ de vision de l’opérateur. Ainsi, il pourra intervenir rapidement en suivant les informations affichées.
Vous avez découvert les impacts des innovations de l'industrie 4.0 sur la maintenance. L'enjeu de l'industrie du futur sera également de collecter et gérer les données. C'est ce que nous allons voir dans le chapitre suivant !