Évaluez le bon équilibre entre correctif et préventif
L’objectif de ce chapitre est économique ! Vous allez économiser sur les stratégies de maintenance, sur les machines vieillissantes et même sur les stocks. Commençons par les stratégies de maintenance !
Dans certains cas, votre intuition vous pousse à réviser vos choix entre le préventif et le correctif : le préventif n’est pas forcément la solution la plus économique. Ces cas sont ceux de machines à fonctionnement intermittent ou aux coûts directs et indirects faibles et sans risques humains. Il s’agit donc de comparer le coût du préventif et celui du correctif pour une même machine.
Quel est le bon équilibre entre préventif et correctif ? Faut-il systématiquement privilégier le préventif, quel que soit l'équipement de production ?
Pour comparer 2 coûts aussi différents, il faut utiliser la même unité de temps : un coût horaire ou journalier (même base de temps). Dans les 2 cas, ce coût horaire est l’équivalent du montant que vous devriez placer chaque heure pour vous “payer” une panne ou une opération préventive. Ce coût horaire, cumulé (correctif) ou décumulé (préventif) en fonction du temps passé, permet d’évaluer la meilleure périodicité de préventif avec le risque économique le plus faible, dans le cas ou la panne s’est déjà produite.
Coût du préventif en fonction du temps
Vous connaissez le coût, CP, d’un remplacement systématique de pièces :
Coût des pièces + coûts de la main-d’œuvre (dans le cas d’arrêt programmé ou hors production) + coût de la perte de production dans le cas d’un process continu.
Ce coût est parfaitement prévisible. L’inconnue est la fréquence de ces interventions.
Le coût moyen de préventif décroît en fonction du temps. Si vous exécutez l’opération la première heure, elle coûte CP ; mais la deuxième heure son coût horaire moyen est CP / 2…
Plus vous attendez pour exécuter ce préventif, plus son coût horaire moyen diminue. CP horaire moyen = CP / t.
Cependant, plus vous attendez plus vous risquez de subir du correctif !
Exemple :
Courbe du coût moyen de préventif en fonction du temps.
Si CP = 1 000 €, au bout de 50 h, le coût horaire est : 1 000 / 50 = 20 € / h.
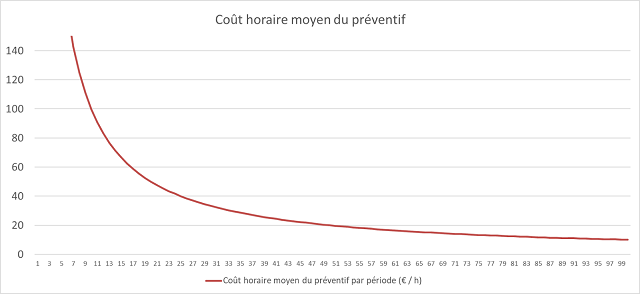
Coût de correctif en fonction du temps
Quand le taux de défaillance est-il constant ? Qu’est-ce la courbe en baignoire ?
Le taux de défaillance d’une machine ou d’un composant mécanique, électrique ou électronique évolue en fonction de sa période de fonctionnement selon ce modèle : la courbe en baignoire.
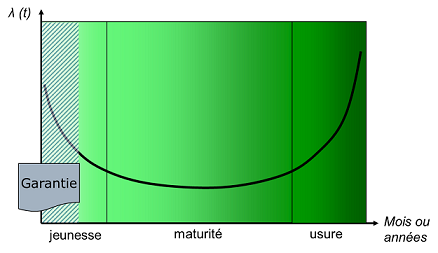
Le taux de défaillance diminue au cours de la période de jeunesse. Les défauts de conception, de matière, de fabrication s’ils apparaissent, sont éliminés par rodage, déverminage et améliorations. Cette période est couverte par une garantie constructeur.
Le taux de défaillance est constant au cours de la période de maturité (la plus longue).
Le taux de défaillance augmente au cours de la période d’usure.
Nous allons considérer dans ce qui suit, que l'équipement se situe dans sa période de vie utile à taux de défaillance constant.
Calcul du coût d’une défaillance
Connaissant la MTTR (moyenne des temps techniques de réparation), le coût moyen des pièces de rechange calculé sur une dizaine de pannes (ou plus, si possible), le taux horaire du technicien, de l’opérateur inoccupé et de la perte de production, vous en déduisez les coûts direct et indirect, et donc le coût total d’une défaillance de la machine concernée.
Calcul du coût horaire moyen d’une défaillance
On utilise le taux de défaillance , nombre de défaillances par heure. Ce taux assimilable à une vitesse de défaillance est constant dans notre cas. C’est-à-dire que chaque heure, la dégradation augmente de la même valeur . Plus le temps de fonctionnement de la machine augmente, plus elle se dégrade. À la deuxième heure, la dégradation est 2 fois plus élevée qu’à la première.
On appelle CD, le coût d’une défaillance. Le coût horaire moyen de la défaillance est : . Pour une MTBF de 1 000 h, le taux de défaillance = 1 / MTBF soit 0,001 déf / h.
Si CD = 1 000 €, le coût horaire appliqué à :
la première heure est : 1 000 x 0,001 x 1 = 1 € ;
la deuxième heure est : 1 000 x 0,001 x 2 = 2 € ;
la troisième heure est : 1 000 x 0,001 x 3 = 3 €.
On en déduit le coût horaire moyen de ces 3 premières heures : (1 + 2 + 3) 3 = 2 €
Il est ensuite possible de comparer les coûts horaires moyens du préventif et du correctif. Prenons un exemple :
coût d’une révision préventive : 1 000 € ;
coût d’une panne : 1 000 € ;
taux de défaillance : 0,001 déf / h.
On peut donc calculer les valeurs suivantes et les représenter sur un graphique :
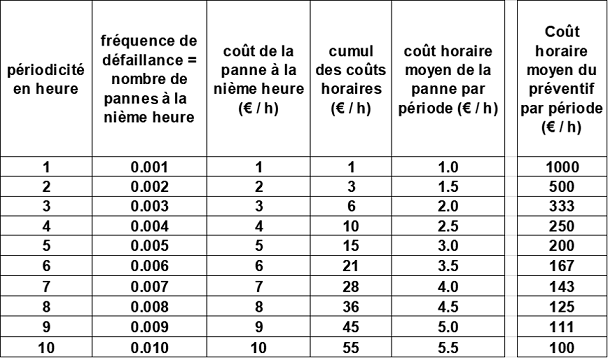
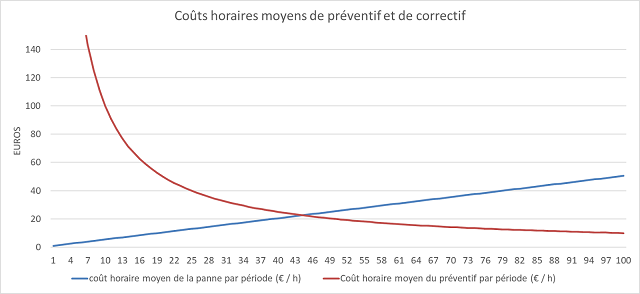
Les coûts horaires sont identiques à la 45e heure, soit près de 20 € / h. C’est la période optimale pour réaliser l’intervention préventive. Au delà, la dégradation aura un impact plus important sur le coût du correctif. À 100 h, le coût horaire moyen de correctif sera de 50 €.
Décidez de l’âge de retraite de vos machines
Nous venons d’obtenir la meilleure périodicité économique des interventions préventives. Est-il possible de trouver la durée de vie économique d’une machine ? Eh oui ! Vos machines aussi ont le droit de partir en retraite. Mais c’est vous qui décidez quand.
Pour déterminer l’âge de retraite de vos machines, il y a deux méthodes :
Rechercher l’année à partir de laquelle les coûts moyens de maintenance augmentent inexorablement.
Rechercher l’année où vous faites les recettes maximum avec cette machine.
Mise en retraite quand ma machine me coûte trop cher
Chaque année, vous allez calculer la somme des dépenses annuelles (main-d’oeuvre et pièces détachées), auxquelles vous ajoutez toutes celles des années précédentes. Prenez aussi en compte la valeur d’achat et éventuellement, si vous la connaissez, la valeur de revente.
Pour l’année n, vous aurez :
Investissement cumulé de l’année n = Va + (dépenses) -
= valeur d’achat
= valeur de revente de l’année n
(dépenses) = cumul des coûts directs de maintenance
L’investissement dans cette machine va augmenter chaque année. Mais plus vous gardez la machine longtemps, plus elle est rentable. À moins que les coûts directs soient tels, qu’elle vous coûte en moyenne de plus en plus cher chaque année. Pour le constater, calculez le coût annuel moyen de maintenance : . C’est-à-dire, divisez le cumul des dépenses année n par le nombre d’années, c’est-à-dire n.
= [Va + (dépenses) - ] x 1/n
À quelle année devriez-vous vous séparer de cette machine ?
Calculons le coût annuel moyen de maintenance de cette machine en fonction des années :
Il faut ensuite tracer la courbe avec ces valeurs de Cma et trouver le point de la courbe le plus bas :
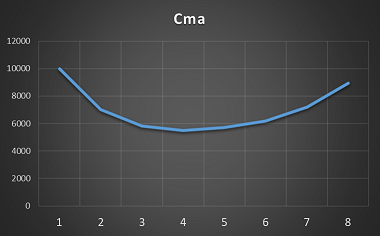
Il aurait donc fallu revendre cette machine juste après la 4e année, car son coût moyen annuel de 5 500 € commence à augmenter.
Mise en retraite quand les recettes de ma machine diminuent
Cet indicateur est plus intéressant, car il prend en compte la marge annuelle que la machine génère en produisant des biens vendables. Il s’agit du LCC pour Life Cycle Cost (coût du cycle de vie). Ce paramètre analyse les dépenses cumulées calculées comme précédemment, et les recettes cumulées :
pour les dépenses, il faut penser à toutes celles qui concernent la machine : coût de maintenance, coût de pertes de production, coût des énergies, coût des opérateurs ;
pour les recettes, il s’agit du chiffre d’affaire cumulé apporté par la vente des produits fabriqués chaque année.
Prenez le cas de cette machine achetée 200 000 € en 2015 :
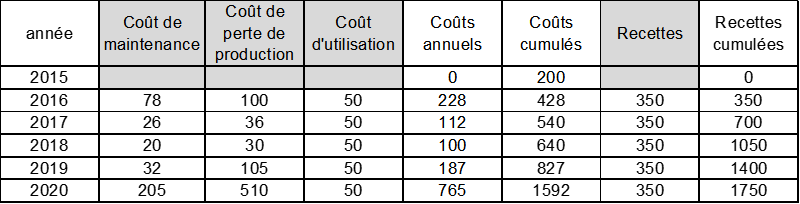
Pour tracer les 2 courbes, vous utilisez les montants de la colonne Coûts cumulés et ceux de la colonne Recettes cumulées.
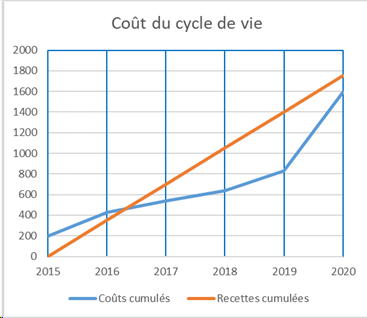
Les 2 courbes se croisent une première fois en 2016 quand la machine est amortie. Elle se croiseront après 2020 quand la machine cessera d’être rentable. Entre-temps, elle connaît une rentabilité maximale en 2018. Mais en 2019, c’est le moment de la revendre.
Grâce à ces 2 méthodes, vous avez réduit fortement les dépenses d’investissement et de maintenance. Il reste des dépenses de maintenance incontournables : le stock de pièces de rechange.
Optimisez vos stocks
Gérer des stocks, c’est conserver une quantité de pièces, achetées à une certaine date, dans un espace limité, durant un temps limité par des sorties de magasin. C’est donc gérer des entrées et des sorties de pièces, tout simplement comme on le fait chez nous pour des paquets de pâtes, du pain ou du fromage.
Alors, quelles sont les contraintes ?
Le type de pièces à acheter : de faible ou de forte valeur.
La quantité : ni trop élevée, ni trop faible, pour éviter des ruptures ou des surstocks entraînant dans les 2 cas des pertes.
L’achat : le budget est limité. C’est même la contrainte majeure !
L’espace : il est limité pour chaque lot de pièces stockées.
Le temps de stockage : plus il est long, plus la somme d’argent immobilisée dans ces pièces est indisponible pour des besoins plus rémunérateurs.
Les entrées et les sorties : si elles ne sont pas ou mal comptabilisées, il est totalement inutile d’espérer gérer les stocks !
Passons en revue quelques-unes de ces contraintes. Commençons par les entrées/sorties.
D’une manière simple, on peut les représenter comme une suite de variations en dents de scie des quantités stockées, en fonction du temps. Une quantité de pièces est commandée et entre au magasin. Elle en sort à l’occasion de besoins successifs de maintenance, renseignés par le compte rendu d’intervention et les bons de sortie matériel.
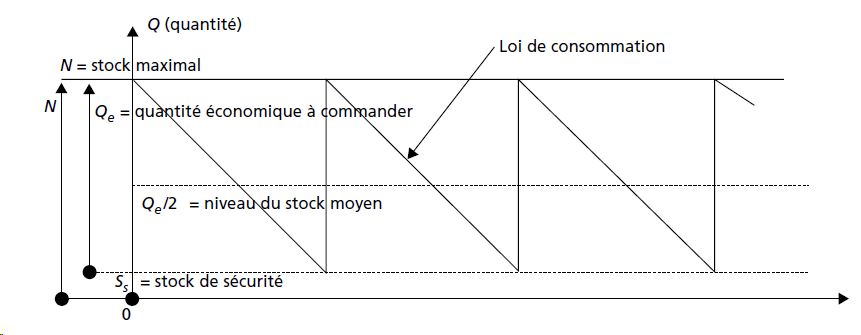
Contrainte n° 1 : chaque entrée doit être inscrite dans le logiciel de stock. Elles ne sont pas si nombreuses, donc accessibles à tous. Mais ce sont surtout les sorties qu’il ne faut pas oublier d’enregistrer, sinon toute gestion sera impossible. Cela demande une grande rigueur de toute l’équipe (cela passe notamment par les comptes rendus d’intervention que nous avons vus dans la partie 3).
Contrainte n° 2 : de quelle pièce s’agit-il ? Quelle est la quantité à commander ?
Ces 2 caractéristiques sont à gérer simultanément :
les pièces de faible valeur (visseries, raccords, huile...), les consommables en général peuvent être commandés par lots régulièrement, en fonction des moyennes de consommation enregistrées précédemment, pour éviter des ruptures plus coûteuses que des surstocks passagers ;
Les pièces de valeur moyenne et de consommation stable sont gérées à partir d’un calcul de “quantité économique” obtenu par la formule de Wilson. Cette méthode optimise le coût d’immobilisation de capital stocké, et celui du temps administratif passé à commander et réceptionner les commandes.
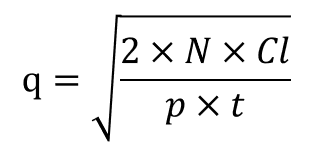
N = consommation annuelle des pièces
Cl = coût de passation de commande (frais administratifs, etc. ; toutes dépenses proportionnelles au nombre de commandes)
p = prix de la pièce
t = taux de possession de stock (intérêts du capital immobilisé, frais de stockage, locaux, assurances…). C’est le manque à gagner par rapport aux intérêts acquis si ce capital était investi dans un équipement de production.
Prenons un exemple :
un article acheté au prix p = 3 € ;
de consommation annuelle N = 600 ;
le coût de passation de commande d’un lot est Cl = 15 € ;
le taux de possession est t = 15 %.
La quantité à commander est q = 200 pièces. Sachant que la consommation est de 600 pc / an, la commande s’effectuera tous les 4 mois.
Contrainte n° 3 : à quel moment faut-il commander ?
La méthode du point de commande permet d’éviter les ruptures en cas de consommations fluctuantes.
Quelle que soit la pente des consommations, la commande est passée au même niveau de stock : le stock d’alerte Sa. La commande est déclenchée à la date où l’on dépasse le stock d’alerte. Ce stock restant correspond à ce qui est consommé pendant le délai de livraison d.
Sa = Qs x d
Qs = quantité journalière consommée
d = délai de livraison en jours
Par exemple, si la consommation annuelle est N = 600 pièces pendant 50 semaines et le délai d’approvisionnement est de ½ semaine, le point de commande sera déclenché au stock d’alerte :
Sa = 600 x 0,5 / 50 = 6 pièces.
Exercice
Votre consommation moyenne en lubrifiant est de 800 litres par an (50 semaines) approvisionnés par fûts de 50 litres en 1 semaine.
Le temps passé et les frais par commande vous coûtent : Cl = 50 €.
Le taux de possession du stock est de : t = 10 %.
Le prix d’un litre de solvant est de : p = 5 € / litre.
Déterminer le nombre de fûts à commander. Calculer le stock d’alerte (ou point de commande). Si vous ne commandez jamais plus que la quantité économique trouvée en (1) et que les livraisons arrivent quand les fûts sont vides, quelle est la valeur moyenne annuelle du stock ?
Réponse
En appliquant la formule de Wilson : la quantité à commander = 400 litres soit 8 fûts.
Le point de commande se situe au stock d’alerte, Sa = 800 x 1 / 50 = 16 litres.
La valeur moyenne annuelle du stock de lubrifiant est de : (400 / 2) x 5 € = 1 000 €.
Conclusion de la partie 4
Vous serez jugé sur l’économie que vous faites faire à l’entreprise. Les indicateurs graphiques de TRS, MTBF, MTTR… sont là pour vous guider. Vous savez aussi agir sur votre personnel, vos machines et votre stock : gagner du temps, éviter les investissements inutiles, limiter l’argent immobilisé.