Il est temps de valoriser ce que vous avez appris dans la partie précédente. Comment ? Vous allez découvrir comment engager l’équipe Maintenance, le service Production et même toute l’entreprise dans des démarches que tout le monde attend. De cette façon, vous obtiendrez un parc machines éclatant et fiable. Ce sera une grosse charge de travail, mais vous gagnerez en assurance et en prestige.
Adoptez une démarche ambitieuse : la TPM
TPM est l’abréviation de Total Productive Maintenance. En français, cela signifie “maintenance totale productive”. Cette démarche peut être définie en détaillant chacun de ses termes :
total : associer tous les services ;
productive : pénaliser le moins possible la production ;
maintenance : prévenir les pannes, nettoyer, réparer et y consacrer du temps.
La TPM est une démarche longue mais complète et efficace, qui engage toute l’entreprise avec l’idée que l’excellent état des machines permet d'accroître le rendement global des installations, la qualité et la sécurité.
Elle agit sur les indicateurs de performance d’une entreprise :
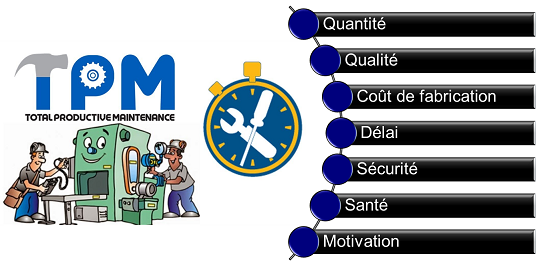
Le planning de mise en place de la TPM s’étale sur plusieurs mois, voire plusieurs années. Tous les services doivent y participer. Cette démarche nécessite notamment une forte implication de la direction et un pilotage de type “gestion de projet”.
Voici un exemple de feuille de route pour la mise en place d’une démarche TPM :
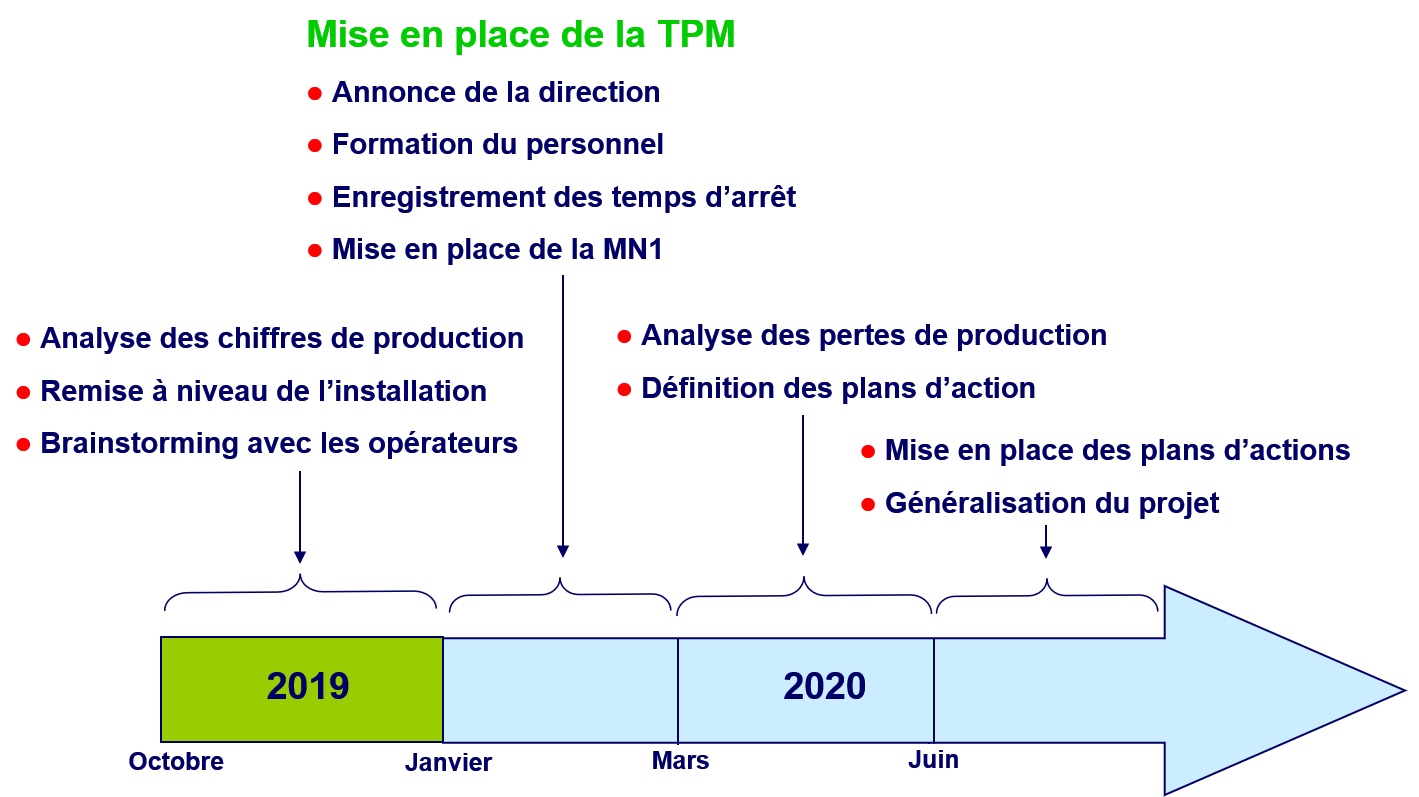
Découvrez les 8 piliers de la TPM
La TPM est une méthode exigeante, inventée au Japon dans les années 1960. Elle est présentée habituellement par 8 préceptes ou “piliers”, dont le premier est l’élimination drastique des causes de pertes, on parle également de “gaspillage”.
Les quatre premiers piliers ont pour objectif d’améliorer l’efficience du système de production. Les quatre suivants permettent d’instaurer les conditions idéales à la performance industrielle.
Éliminer les 6 causes de pertes.
Appliquer l’automaintenance.
Appliquer la maintenance planifiée.
Améliorer les connaissances et savoir-faire.
Gérer les nouveaux projets et capitaliser les savoirs.
Maîtriser la qualité.
Améliorer l’efficience des services connexes.
Éliminer tous risques d’accident.
Pour parvenir à instaurer cette démarche, les clés du succès sont :
le choix judicieux du secteur “pilote” ;
la motivation des participants ;
l’informatisation et la simplification des remontées d’informations ;
le management participatif ;
les encouragements réguliers de la direction.
Vous avez l’appui de votre direction pour engager l’entreprise dans cette démarche ? Bravo ! Vous êtes passé chef de projet. Vous allez avoir besoin de tout votre sens du relationnel et de votre ténacité pour conduire ces changements. Vous serez guidé dans votre démarche tout au long de cette partie.
Terminons ce chapitre par un court quiz, prenez quelques minutes pour y répondre avant de regarder les réponses en-dessous. Nous reviendrons sur ces éléments dans les chapitres suivants !
Pour réussir votre démarche TPM :
La démarche 5S permettra de répondre à 80 % des problèmes rencontrés. OUI/NON
La formation technique des opérateurs est indispensable. OUI/NON
La remise en état des machines est indispensable. OUI/NON
Il est préférable de commencer par un atelier pilote. OUI/NON
La TPM associe le personnel des services :
Production et Maintenance.
Production, Maintenance et Qualité.
Tous les personnels techniques de l’entreprise.
Tous les personnels de l’entreprise.
La MN1 est exécutée par les personnels des services :
Production et Maintenance.
Production.
Maintenance.
Maintenance et Qualité.
Réponses
NON / Le 5S est un outil de progrès de base en TPM, mais il n’est pas suffisant pour atteindre l’objectif.
OUI / Une partie de la maintenance est déléguée aux opérateurs qui doivent recevoir une formation technique de base.
OUI / Il est improductif d’appliquer une maintenance préventive sur des machines déjà dégradées.
OUI / Il faut cibler d’abord un atelier dont les machines sont vitales pour l’entreprise et se dégradent par manque de maintenance.
4) La TPM associe tous le personnel de l’entreprise. C’est une démarche globale.
2) La MN1 est exécutée par la production. C’est une maintenance déléguée.
Commençons par le premier pilier de la démarche TPM : la chasse aux gaspillages. À tout de suite dans le chapitre suivant !