Les solutions de supervision avancées dans le process
Vous l’avez compris, l’usine du futur doit rendre les machines “transparentes”, ou plutôt communicantes. Mais comment remplacer l’œil, l’oreille, le toucher, le nez du technicien quand il s’agit de capter ces sensations à l’intérieur de la machine, comme le fait l’opérateur en maintenance de niveau 1 à l’extérieur de la machine, en marche et à l’arrêt ?
C’est un défi que les capteurs connectés de contrôles non destructifs, CND, peuvent résoudre dès aujourd’hui. Les CND permettent de mesurer l’état de fonctionnement de systèmes industriels, les niveaux d’usure. Ils facilitent ainsi la prédiction de maintenance, qui devient alors conditionnelle. En tant que générateurs de données, ils sont associés à d’autres types de capteurs. L’ensemble des mesures doivent alors être compilées et analysées par IA (intelligence artificielle), pour réaliser des prédictions de maintenance à réaliser.
Voici les principaux capteurs qui, demain, équiperont toutes les machines pour les rendre communicantes.
La thermographie
Selon la définition de l’AFNOR, la thermographie est la technique permettant d'obtenir, au moyen d'un appareillage approprié, l'image thermique d'une scène observée dans un domaine spectral de l'infrarouge.

La tomographie
Il s’agit d’un système d’imagerie qui permet de reconstituer le volume d’un objet, à partir d’un grand nombre de mesures réalisées par tranches. Cette famille de techniques permet de réaliser des contrôles métrologiques particulièrement précis, et surtout d’inspecter l’intérieur d’une pièce ; et notamment sa structure métallurgique.
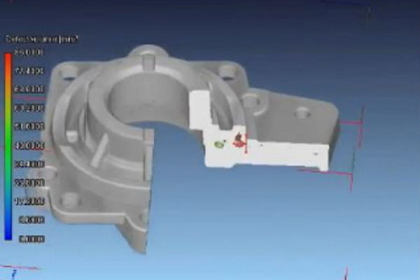
L’émission acoustique
Cette technique repose sur l’émission d’ondes élastiques transitoires dans un matériau. Elle permet de suivre l’évolution dynamique d’un défaut d’une structure, et donc de suivre la détérioration de celle-ci. Cette technique est particulièrement avantageuse, car elle peut s’effectuer sans arrêt de fonctionnement (et donc de production), tout en apportant un diagnostic global.
Le CND par ultrasons
Cette technique permet de mettre en évidence des défauts internes à une pièce, par l’émission d’ultrasons et l’analyse de leur réflexion ; les ondes interagissant avec les défauts rencontrés.
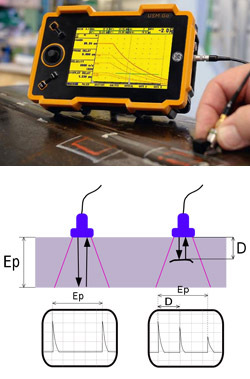
L’analyse vibratoire
Il s’agit d’une technique permettant de réaliser des prédictions de maintenance sur des machines tournantes. Le principe consiste à réaliser une mesure initiale d’une machine, qui en constitue sa signature. De nouveaux relevés sont réalisés à intervalles réguliers, et sont comparés à l’analyse initiale. Toute variation sera le signe d’un problème potentiel, tel qu’un desserrement de vis, par exemple.
La métrologie optique - Mesure par laser
Ces méthodes reposant sur les propriétés de la lumière présentent l’avantage d’être rapides à réaliser, et souvent faciles à mettre en oeuvre. Les mesures par laser permettent, par la précision de ce dernier, de réaliser des contrôles d'alignement, de rectitude, de niveau, d'angles, d'épaisseur, d'apparence, de déplacement, de vibrations. Ces mesures peuvent s’appliquer à la reconnaissance dimensionnelle d’un outil de coupe et détecter la moindre usure, déclencher son échange automatique en fonction d’une consigne, et asservir la machine en cas de casse.
Intégrez et exploitez les Big Data
L’inflation exponentielle de capteurs et objets connectés entraîne la création d’une quantité tellement massive de données, que les bases de données classiques ne peuvent les gérer. Les enjeux du Big Data consistent à être en capacité de gérer, de qualifier et d’utiliser en un temps très court l’ensemble des données disponibles.
Évidemment, tous les domaines industriels sont intéressés par le Big Data, source d’informations inépuisable, tant pour déduire des comportements machines ou humains, prédire des défaillances, que permettre la traçabilité unitaire des produits. L’objectif est de créer un écosystème informationnel en capacité de permettre à l’industriel d’améliorer ses processus, et d’accroître sa performance.
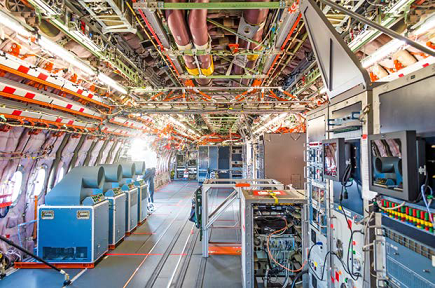
Comment passer d’une maintenance prédictive à une maintenance proactive ?
Le métier le plus impacté par la digitalisation de l’industrie est la maintenance. Celle-ci est au cœur de la performance industrielle, car elle permet d’optimiser la production par une maximisation de la disponibilité du moyen.
Cette optimisation est réalisée par le triptyque maintenabilité - disponibilité - fiabilité. Pour cela, il s’agit de réduire le taux de pannes, d’agir uniquement lorsque cela est nécessaire et de diminuer les temps de maintenance.
Les objectifs et les moyens d’y parvenir sont les suivants :
Réduire les coûts
Pour cela, plusieurs leviers existent :
rendre les opérateurs et techniciens plus efficaces lors de la maintenance elle-même ;
optimiser la gestion des stocks ou la gestion des obsolescences ;
digitaliser les outils de production et les équipements de surveillance, avec l’implantation de capteurs.
Accroître la maintenabilité
Il s’agit ici de faire en sorte que la maintenance de l’équipement soit toujours possible et surtout, optimisée. Pour cela, la maintenance devra être prise en compte dès la conception des systèmes (pilier n° 5 de la TPM). L’obsolescence des pièces ou leur usure pourront être contrôlées via des capteurs ou des contrôles non destructifs.
Le développement de la maintenance prédictive par la captation de données en continu des systèmes à maintenir, puis l’analyse par des algorithmes d’intelligence artificielle, permettent la mise en oeuvre d’une maintenance prédictive et conditionnelle particulièrement fiable. Ainsi, le responsable Maintenance devra intégrer les technologies du Big Data, du Data Scientist, ainsi que l’intelligence artificielle.
Prévenir les risques professionnels et réduire la pénibilité
L’utilisation de moyens comme les exosquelettes permettent une réduction de la pénibilité lors des actions de maintenance :
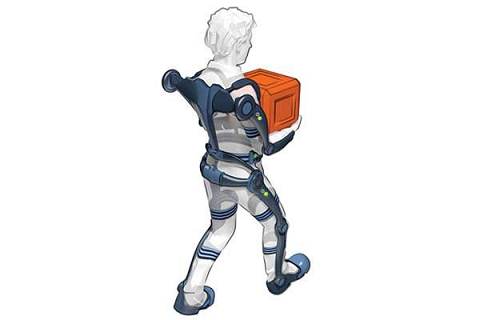
Évolution du métier de la maintenance
Le poids de l’industrie est passé de 18 % à 12 % du PIB (produit intérieur brut), et nos machines vieillissent : de 17,5 ans d’âge moyen en 1998 à 19 ans en 2013. Dans le même temps, le parc machines se contracte de près de 7 %, passant de 414 000 machines à 388 000, malgré une pénétration accrue des machines à commande numérique. Mais le déclin n’est pas une fatalité. Des opportunités sont devant nous !
Maintenance plus prédictive et durable
Les données collectées sont analysées en temps réel, selon une modélisation multiphysique. L’analyse de l’évolution de ces données, des historiques, des retours d’expérience et des modèles multiphysiques est opérée par une intelligence artificielle, afin de prévoir les usures ou casses futures.
Maintenance plus efficiente et optimisée : automatisée et assistée
Prenons le cas d’interventions de maintenance en milieu sensible, comme par exemple les milieux hyperbares (sous-marins, tunnels, caissons), les environnements hautement inflammables ou explosifs (ATEX), soumis aux rayonnements ionisants (nucléaires, médical…) ou encore exposant à des risques CMR (cancérigène, mutagène et reprotoxiques).
Il est évident que ces opérations sont toujours délicates à réaliser, tant en phase de préparation que d’exécution. Ainsi, les outils technologiques peuvent être utilisés à de multiples niveaux et moments du processus :
formation des opérateurs via la réalité virtuelle, afin de réduire les risques lors de l’action elle-même tout en optimisant les gestes ;
préparation de l’opération de maintenance via des simulateurs ;
assistance méthodologique ou physique de l’opérateur sur le site ;
téléopération. Il est à noter le développement possible de l’analyse et de la prise de décisions à distance. Un centre de contrôle permet d’assurer, en optimisant, la maintenance à distance de nombreux équipements.
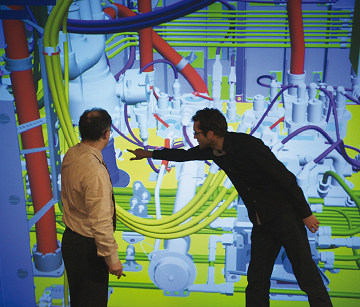
Conclusion de la partie 3
L’usine 4.0 est avant tout une usine communicante. L’objectif est d’être en capacité de faire des choix fiables et rapides, grâce à une panoplie de techniques de surveillance, connectée à une intelligence artificielle et renseignée par vos retours d’expérience. C’est là que la GMAO joue son rôle. Mettez-la en service rapidement, et développez-la pour qu’elle soit prête, elle aussi, à entrer dans le futur.