Mesurez l’efficacité d’un équipement grâce au TRS et au TRG
Les indicateurs de performance sont nombreux, mais il n’y en a qu’un qui englobe les autres : le taux de rendement synthétique.
Taux : il s’exprime en %, donc est compréhensible par tous.
Rendement : il est une image de la performance. Très intéressant quand il s’agit de mesurer les progrès suite à un plan d’action.
Synthétique : il englobe toutes les défaillances des services de l’entreprise.
C’est comme si vos moyens de production avaient des fuites !
Mais qu’y a t-il dans ces gaspillages ? Quelles sont les actions à entreprendre pour progresser ?
Le calcul du TRS
Il existe 3 types de gaspillages : | Ils se calculent indépendamment par : |
1. Les arrêts de production. | 1. Le taux de marche : TM. |
2. Les ralentissements de cadence. | 2. Le taux de performance : TP. |
3. Les produits non conformes. | 3. Le taux de qualité : TQ. |
Tous ces gaspillages se mesurent en temps perdu. Ce qui nous amène à définir les temps :
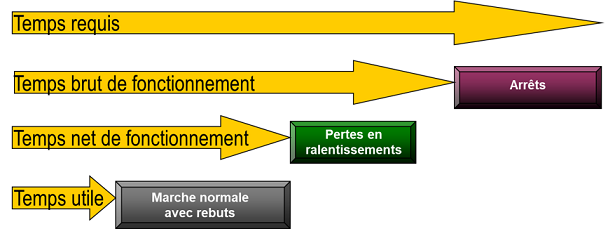
Les 3 taux se calculent comme suit :
taux de marche = TbF / TR ;
taux de performance = TnF / TbF ;
taux de qualité = nombre de pièces OK / nombre total de pièces produites.
Le TRS est le produit des 3 taux : TRS = TM x TP x TQ, mais aussi plus simplement : TRS = TU / TR. C’est-à-dire le rapport entre le temps produisant de la valeur ajouté à pleine cadence et le temps alloué pour ce travail.
Prenez l’exemple d’une production de bouteilles :
le temps de production demandé, c’est à dire l’OF, est de 7 h ;
au cours des 7 h, la production subit 1 h d’arrêt ;
La quantité produite est de 300 bouteilles, dont 6 non conformes ;
La transformation de granulés plastique en bouteille doit prendre 1 min : c’est la cadence nominale.
Le rendement est-il correct ? Sinon, quelles sont les marges de progression ? Et dans quels domaines ? Remplissez les flèches de temps et appliquez les formules.
Réponse : en remplissant les flèches de temps, on constate :
7 h de temps requis ;
6 h de temps brut de fonctionnement : 7 h - 1 h ;
5 h de temps net de fonctionnement : 300 bouteilles x 1 min / bouteilles = 300 min = 5 h ;
6 min de temps perdu à produire des bouteilles non conformes : 6 bouteilles x 1 min.
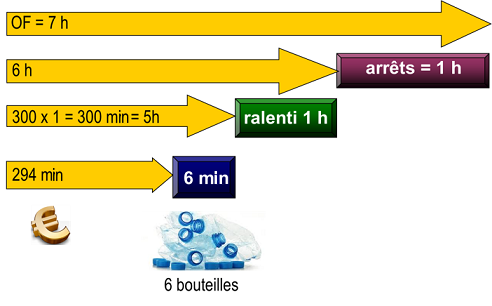
Les 3 taux sont :
taux de marche, TM = 6 / 7 = 0,86 = 86 % ;
taux de performance, TP = 5 / 6 = 0,83 = 83 % ;
Taux de qualité, TQ = 294 / 300 = 0,98 = 98 % ;
TRS = TM x TP x TQ = 70 %.
Conclusion : il y a de fortes marges de progression, en particulier dans le domaine des ralentissements de la machine (TP = 83 %).
Les 6 causes de pertes
Les 6 causes de perte de rendement mobilisent les 3 services créateurs de valeur ajoutée : Production, Maintenance, Qualité.
Prenons un exemple que vous avez dû observer si vous êtes déjà parti en vacances au ski : les remontées mécaniques ! En bas des pistes, il est indiqué la capacité théorique du télésiège : 960 personnes / heure soit 16 personnes / min.
Toutes les 15 secondes, vous devriez avancer ! Il n’en est rien. Une observation attentive donnerait plutôt 150 personnes / heure en moyenne.
Alors, où sont les causes de pertes ?
PERTES | TYPE | CAS DU TÉLÉSIÈGE |
Panne | Arrêt involontaire | Panne d’électricité Déréglage Casse de matériel |
Changement de fabrication | Arrêt volontaire | Fixation de supports de VTT en été |
Micro-arrêt | Non performance involontaire | Arrêts courts lors de la montée d’un débutant en snow |
Ralentissement | Non performance volontaire | Réduction de vitesse pour faire descendre des piétons non skieurs |
Non qualité | Non qualité involontaire | Le skieur qui chute et se blesse en descendant |
Perte au démarrage | Non qualité volontaire | Des sièges partent à vide ou sont incomplets |
Dans le cas de remontées mécaniques présentées ci-dessus, quel serait le TRS pendant la saison ?
Réponse : TRS = en moyenne 150 / 960 = 15 %.
Sachant que la saison de ski dure 5 mois et la saison de VTT 2 mois, quel serait le TRG ?
Réponse : TRG = TRS x (5 + 2) / 12 = 9 %. L’investissement des installations est rentabilisé sur 9 % de son temps.
Heureusement, dans l’industrie les solutions aux causes de pertes sont connues, et leurs méthodes assez simples à appliquer.
Les leviers d’amélioration
Vous l’avez peut-être remarqué, la moitié des pertes est de type volontaire et même programmé. Ne vous étonnez pas, dans ce cas, que personne avant vous, n’ait pensé à les combattre. On a tendance à oublier qu’un arrêt planifié d’une heure pour un changement de fabrication est équivalent à une panne d’une heure subie par l’entreprise.
Les pertes de rendement volontaires
Ces 3 causes de pertes sont mesurables en partie grâce aux 3 taux desquelles elles relèvent : TM, TP, TQ. Vous pouvez donc définir une priorité. Pour chacune d’entre elles, une distribution statistique, et donc une moyenne et un écart type peuvent être calculés. Vous pouvez à nouveau définir la priorité d’actions. Des solutions “clés en mains” existent. Nous les verrons dans la partie suivante. Pour les mettre en place, prévoyez un groupe de progrès pluridisciplinaire impliqué, et suivez attentivement leur progression.
Les pertes de rendement subies
Les pannes, les micro-arrêts et les rebuts ne sont pas une fatalité. Ces pertes sont dues à une combinaison de non-actions, de laisser-faire, d’anomalies qui entraînent par chaîne causale des conséquences graves. Comme vous l’avez découvert avec la démarche des 5S, des méthodes d’inspection simples permettent d’améliorer pas à pas.
Les données à rassembler
En résumé, pour obtenir le TRS, il vous faut 5 données : TR, somme TA, q, Tu, qb.
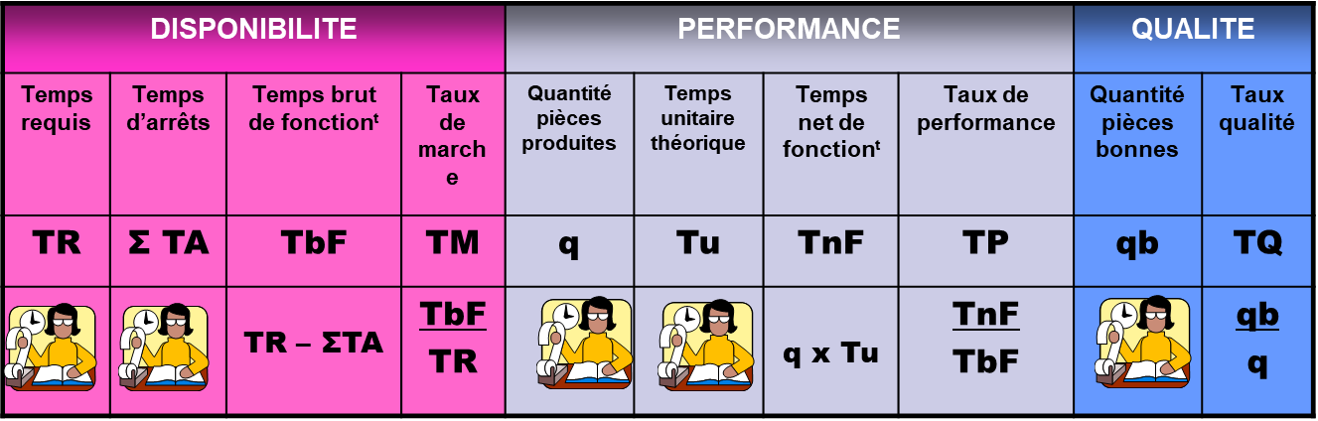
Conclusion de la partie 1
Maintenant vous connaissez :
la position du service Maintenance dans l’entreprise et ses missions ;
les moyens humains de la maintenance et ses relations avec les autres services ;
les méthodes de maintenance, de la plus simple et coûteuse à la plus performante et rentable ;
les accessoires de travail de la maintenance, le 5S et la MN1 ;
le TRS, indicateur de performance compréhensible par tous.
Vous avez plein d’idées en tête pour améliorer la situation de votre entreprise ? Mais vous souhaitez savoir comment appliquer ces idées. Quelle démarche entreprendre pour actionner ces leviers d’amélioration ? C’est ce que vous allez découvrir dans la prochaine partie.