La supply chain doit satisfaire au triptyque Qualité – Coûts – Délais. C’est-à-dire que l’entreprise se donne les moyens de livrer le service ou produit correspondant au besoin client (le marché), en quantité négociée, au moment et à l’endroit convenus, et au niveau de qualité attendu.
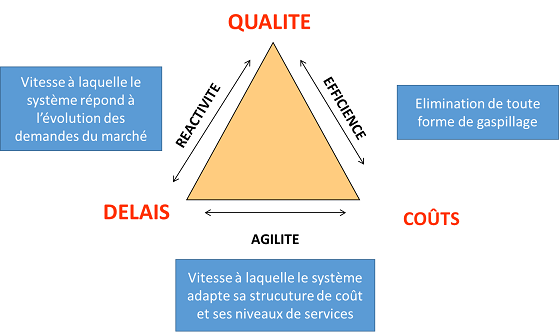
Approvisionnez
Pour commencer, nous garderons le terme approvisionner pour son rôle d’achat, de mise à disposition de l’organisation des matières premières, des produits, des ensembles et sous-ensembles.
Le processus « approvisionner » peut-être illustré comme suit :
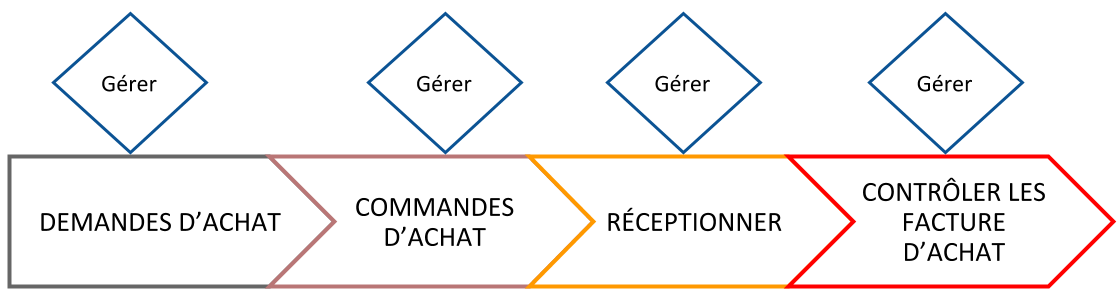
Dans certain cas, nous retrouverons l'expression purchase to pay pour caractériser le cycle de traitement des commandes d’achat, de la demande d’achat, jusqu‘au règlement des factures fournisseurs.
Gérez les demandes d’achats
Une demande d’achat est une instruction sollicitant le service Achat de nous fournir une certaine quantité d’une référence ou service, pour une date fixée.
Elle se caractérise dans l’entreprise par un document interne à notre organisation.
Gérez les commandes d’achats
Les commandes d’achats directs ont pour particularité d’être très fréquemment, voire toujours automatisées en utilisant des méthodes de réapprovisionnement, dites automatiques.
Le choix de la méthode de réapprovisionnement est déterminé en fonction du nombre de paramètres retenus et impactants : le coût, le coût de possession du stock, les délais de réapprovisionnement, la valeur des produits, le type de demande, le nombre de fournisseurs, le nombre de références, le cycle de vie du produit.
Le point de commande (“order point system”) est la méthode de réapprovisionnement utilisée pour déclencher une commande, et tient compte d’une quantité minimale, indispensable pour couvrir la période de réapprovisionnement entre la commande et la réception des produits. Plusieurs types existent :
le système à quantité fixe (fixed order quantity system). C’est une méthode qui génère une commande à quantité fixe à compter du moment où la quantité minimale est atteinte, ce qui peut être confortable pour gérer des demandes régulières, constantes et prévisibles ;
le système min-max permet de gérer les commandes variables et correspondant à la différence entre le stock maximum souhaité, défini, et la quantité de stock. Le stock minimum est notre point de commande.
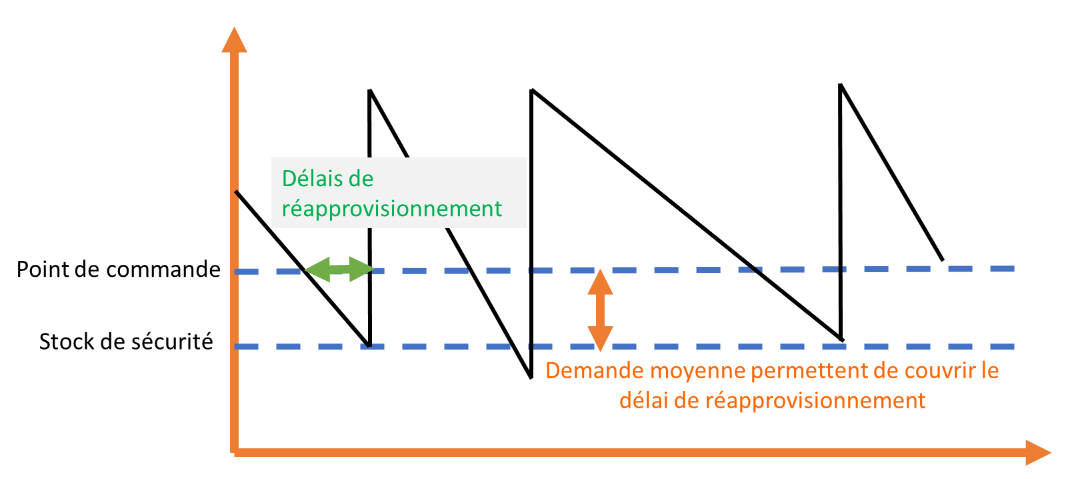
La quantité à commander peut être conditionnée par l’utilisation de la méthode de calcul de la quantité économique, par une valeur fixe : deux façons de réapprovisionner à quantité fixes.
La formule de Wilson
La formule de Wilson (mise au point en 1934), également connue sous le nom Quantité Économique de Commande ou EOQ (Economic Order Quantity) détermine la période optimale de réapprovisionnement d'une unité de production (magasin, usine).
Elle a en fait été introduite dès 1915 par Ford W. Harris, mais a été attribuée à Wilson car il en a fait l'analyse en profondeur, en considérant que la consommation est stable tout au long de l’année et pour un coût proportionnel à la quantité stockée.
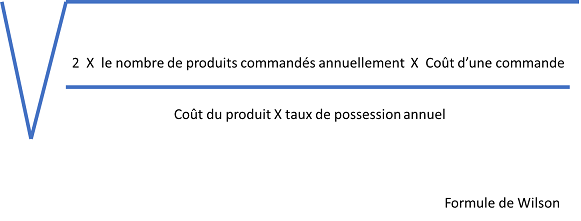
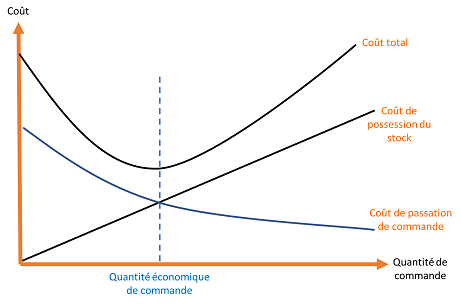
Le système à intervalles fixes (Time-based order system) n’est ni plus ni moins une méthode de réapprovisionnement à intervalles fixes. La quantité commandée est alors variable, et a pour unique objectif de remplacer la quantité consommée durant la période écoulée.
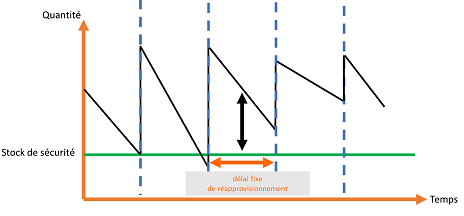
Réceptionnez
Réceptionner les marchandises, c’est préparer leur réception, les réceptionner, les contrôler, les entreposer :
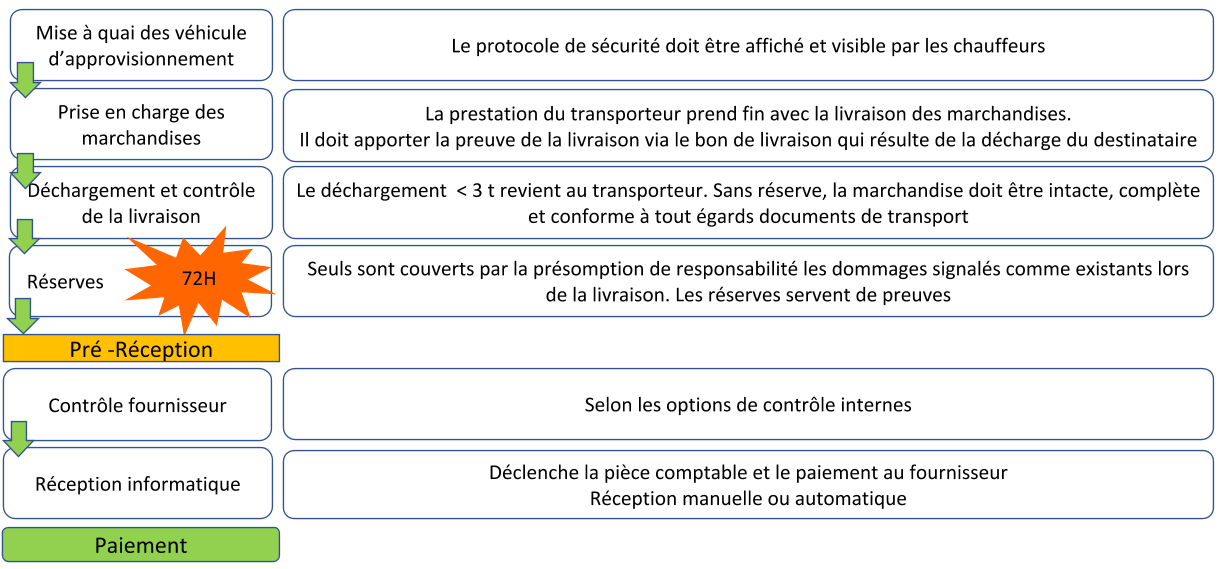
Contrôlez les factures d’achat
C’est l’ensemble des tâches qui incombent au service Gestion – Comptabilité, ce qui suppose une excellente communication, une optimisation des flux d’informations en vue de régler en temps et en heure nos fournisseurs, et de pouvoir traiter à leur juste valeur les différents irritants (problème qualité, retard de livraison, etc.).
Pour ce faire, il est impératif que nous ayons, en amont, défini l’ensemble des clauses du contrat avec notre fournisseur, que notre processus de réception soit identifié et respecté par nos collaborateurs (contrôle qualité, enregistrements, réception conforme par rapport à la commande, etc.
Transformez
Les activités de transformation, de production, d’assemblage, c’est-à-dire l’ensemble des actions qui permettent de créer de la valeur ajoutée dans l’entreprise, sont un maillon de la supply chain. L’ensemble des activités associées à la transformation des matières, des produits, des éléments, ensembles ou sous-ensembles, y compris les flux d’informations, flux physiques et flux financiers, ne peuvent être dissociés.
Distribuez
Distribuer, ou la logistique de distribution, c’est la pratique des méthodes de la logistique traditionnelle pour une gestion optimisée des flux des commandes clients, du fournisseur (entrepôt d’usine, entrepôt de distribution…) jusqu’au lieu de livraison convenu dans le contrat commercial.
Voici les étapes de distribution :
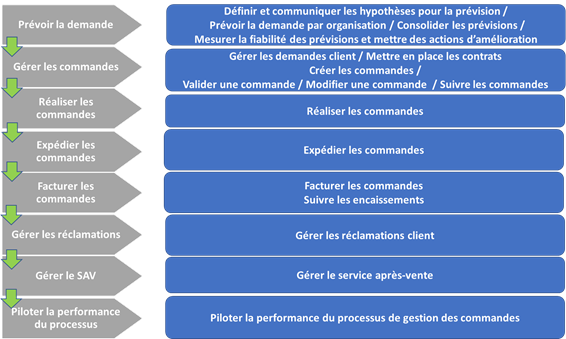
Ces étapes sont complexifiées en raison de plusieurs facteurs impactants :
la multiplicité des intervenants. Il convient de bien organiser la circulation des informations et des marchandises (maîtrise des flux documentaires, planification des opérations physiques à travers le réseau de distribution…) ;
la multimodalité des opérations de transport, du fait de pouvoir ou devoir combiner plusieurs modes de transport successifs pour acheminer, selon la nature, la taille des colis et des produits. C’est pourquoi il est impératif de bien définir le bon emballage pour le bon produit pour le bon transport, de définir des UTI (unités de transport intermodal) et de prévoir que les moyens de manutention adéquats soient disponibles à chaque point de transbordement ;
respect des cahiers des charges clients. Les produits doivent être livrés en quantité et en qualité demandé, dans les délais impartis. Il faut par conséquent adopter les bonnes pratiques (moins de ruptures des charges, gestion anticipée de certaines formalités administratives, intermodalité et accélération des temps de transbordement, etc.) ;
maîtrise des coûts logistiques. Réduction des parcours (pour faire moins de distance, il faut opérer une bonne détermination des routes, bien organiser les tournées, réduire le nombre de retours à vide des camions en leur proposant un fret de retour). Cela implique donc :
un bon choix des prestataires (les prestations achetées doivent correspondre aux besoins),
une meilleure combinaison de moyens, un meilleur taux de remplissage des véhicules, le recours aux stratégies logistiques collaboratives,
l'optimisation des coûts des derniers kilomètres ; le recours au drive ;
maîtrise des risques liés à l’acheminement (risques de transport, manutention et entreposage) :
il convient de réduire le nombre de ruptures de charge lors de l’acheminement, de bien protéger les marchandises et de respecter les conditions de transport pour les denrées périssables,
moins de manipulations engendrent moins de risques et par ailleurs, des coûts d’assurance maîtrisés ;
logistique des retours. Organisation de la collecte et du retour des emballages vides…
Environnement de la production
Dans cette section, il s’agit de mettre en relief l’ensemble des éléments qui agissent sur la production, et de déterminer quelles sont les contraintes qui permettent d’effectuer des choix et de définir les options retenues.
Nous ne produisons pas pour « nous faire plaisir » mais pour satisfaire la demande de nos clients.
L’analyse marketing nous aidera dans cette démarche, dans la définition de la stratégie industrielle. En partant du besoin du marché, nous établirons les besoins non seulement d’un point de vue logistique, mais aussi de la production.
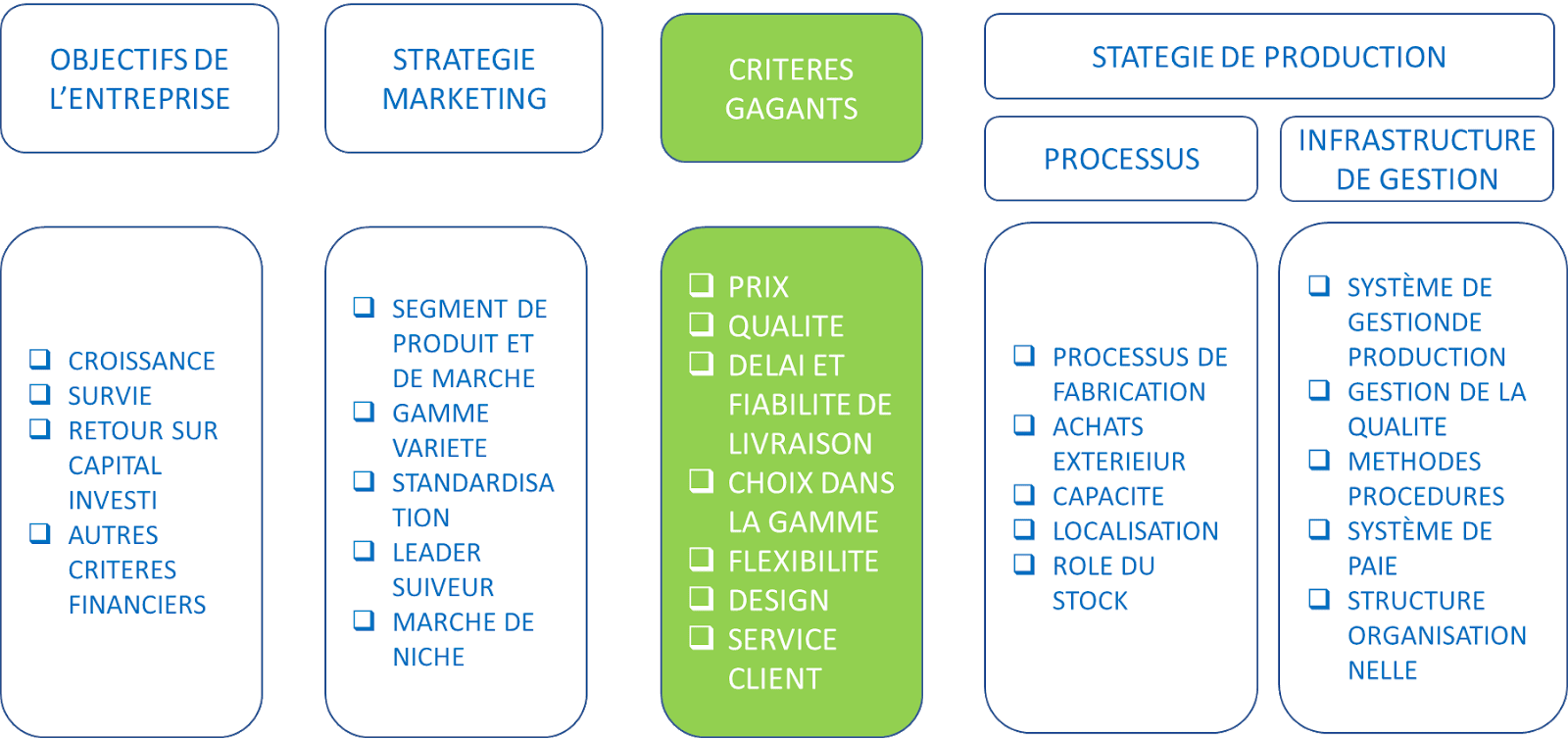
L’environnement de la production doit prendre en considération la « théorie des contraintes ».
Qu’est-ce que la théorie des contraintes ?
Cette théorie vise à améliorer le fonctionnement de l’entreprise en identifiant et en gérant les processus qui constituent les goulots d’étranglement.
Elle a été développée par le professeur Eliyahu M. Goldratt, qui avait commercialisé (en 1979) un logiciel d’ordonnancement de la production OPT (“Optimized Production Technology”) pour équilibrer les flux plutôt que les capacités. En 1984, il rédigea un roman, The Goal, pour promouvoir son logiciel, l’histoire d’un directeur d’usine qui doit améliorer la performance de son site.
La théorie des contraintes part du postulat que l’objectif de l’entreprise est de gagner de l’argent, et qu’il existe toujours au moins un processus appelé « goulot d’étranglement », limitatif à cette quête. C’est pourquoi il est impératif d’améliorer ce processus et donc le processus global, en vue de générer davantage de gains.
Une démarche en 5 étapes :
Étape 1 : identifier la contrainte qui constitue le goulot d’étranglement.
Étape 2 : identifier les solutions permettant de maximiser l’utilisation de la contrainte.
Étape 3 : subordonner tous les autres processus à la contrainte.
Étape 4 : augmenter la capacité de la contrainte.
Étape 5 : la démarche se poursuit pour identifier puis améliorer de nouveaux goulots d’étranglement.