Développement des produits
Le développement de produit ne peut être que l’affaire du service Recherche et Développement ou des méthodes.
Le développement produit est l’affaire de l’entreprise et donc de l’ensemble des parties prenantes de la supply chain. Les caractéristiques du produit, le prix, la qualité, tout ce qui répond au besoin du marché est déterminé lors de la phase de développement, et c’est pourquoi 80 à 95 % des coûts logistiques sont induits par le développement.
Les processus de production, l’industrialisation du produit, le mode de gestion sont des éléments déterminants dans le développement d’un produit ; d’où la nécessité de les définir dès la conception.
La logistique associée à un produit est axée sur le cycle de vie du produit, de la conception à son retrait lié à sa fin de vie. Une telle approche offre un service de qualité tout au long de la durée de vie du produit de la livraison, pendant la période d’utilisation, en vue de satisfaire et de fidéliser notre client.
On parle de CCV, “Coût de Cycle de Vie” en terme économique, puisque l’on comptabilise l’ensemble des coûts générés, par la conception, la production, l’utilisation et le retrait de service du produit.
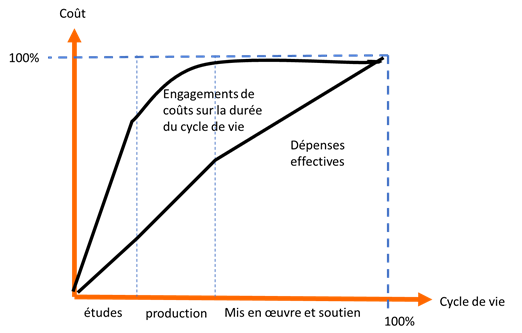
Ce schéma nous fait apparaître que 80 à 95 % des composants du CCV sont figés en fin de phase de conception, rendant toute modification ensuite soit inefficace, soit trop onéreuse.
On peut distinguer diverses approches de conception dans le développement de nouveaux produits :
séquentielle = conception produit + industrialisation + fabrication produit + SAV et maintenance ;
séquentielle et soutien logistique = conception produit + industrialisation + fabrication produit + SAV et maintenance et déploiement des moyens nécessaires dès que le produits est connu ;
SLI (soutien logistique intégré) = intégration du soutien à la conception et optimisation disponibilité et CCV ;
ingénierie intégrée (concurrent engineering) = intégration globale avec prise en compte totale de l’ensemble du processus associé au produit, en particulier la production et le soutien en service dès la conception.
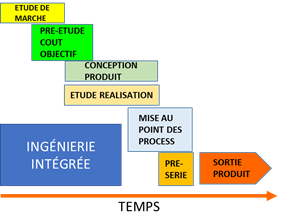
L’ingénierie simultanée ou comment engager des tâches simultanément à d’autres en vue de réduire les délais de mise sur le marché, tout en satisfaisant nos clients.
Le but de cette démarche est d’intégrer l’ensemble des paramètres, tout en réduisant les délais de conception et mise en production des nouveaux produits.
Taille de lot de lancement
La taille de lot de lancement de fabrication correspond au nombre de pièces lancées en fabrication en une seule fois pour satisfaire ma demande.
Un lot de commande peut représenter plusieurs lots de fabrication, si le lot de commande a une taille trop importante.
Au contraire, plusieurs lots de commande d'un produit identique peuvent être regroupés dans un lot unique de fabrication, afin de diminuer le nombre de réglages.
La taille de lot de lancement de commande correspond au nombre de pièces devant être acheminées vers le client :
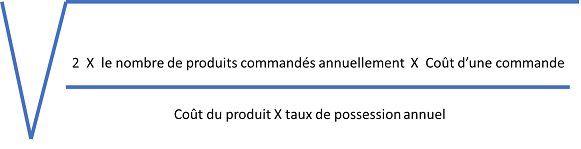
Pour définir la taille de lot optimale, nous utiliserons la formule de Wilson développée dans la première partie du cours. L’intérêt de cette approche, c’est de pouvoir diminuer le coût de lancement et donc la taille des lots. Il est plus intéressant de diminuer le coût de lancement et donc la taille des lots. Plus les prévisions de vente seront exactes, plus les tailles de lots seront précises et économiques.
L’autre conséquence directe de cette optimisation des tailles de lot permettra d’éviter les stocks de produits invendus, déclassés lors de prévisions trop optimistes. Un avantage non négligeable est de pouvoir augmenter le niveau de réactivité lors de problèmes constatés pendant la production, et donc de n’impacter qu’une taille limitée de lot.
Enfin, les délais de mise sur le marché sont plus faciles à tenir et à respecter du fait d’une bonne maîtrise des besoins client. Le respect des délais est plus facile à obtenir.
“Make to stock” ou “Make to order”
“Make to stock” et “make to order” sont deux modèles de production différents, l’un en flux poussé (“make to stock”) et l’autre en flux tiré (“make to order”).
“Make to stock” : production sur stock
Dans le cas d’une demande prévisible et de produits peu onéreux à stocker, ou bien lorsque le délai de production est plus long que le délai client, nous produirons selon nos historiques de demande et la prévision des ventes. C’est la méthode MRP que nous avons vue au début de la partie 2.
“Make to order” : production à la demande
La production est effective uniquement quand la commande client est confirmée. Elle est utilisée pour limiter les coûts de stockage lors de la confection de produits unitaires onéreux, lorsque la demande est volatile, ou lorsque les volumes à produire sont faibles.
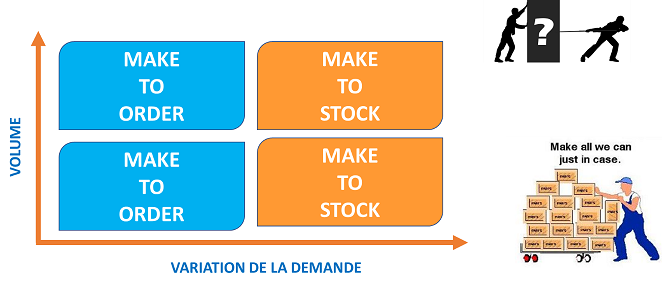
Il ne s’agit pas d’utiliser une méthode ou l’autre, mais de compiler les deux afin d’optimiser la réponse à la demande, de gérer nos stocks, comme dans la différenciation retardée que nous verrons ci-dessous. Par conséquent, une bonne maîtrise dès la conception permettra de concevoir une composition modulaire du produit finis.
Voici un tableau permettant de se situer et de définir quelques orientations :
Stratégie | Quand | Avantage |
Make to stock | Produit standardisés Demande relativement prévisible | Coût de fabrication bas Délai de remise au consommateur court |
Make to order | Produits personnalisés Variabilité | Personnalisation Réduction des stocks Amélioration du taux de service |
Assemble to order | Multiples finitions par produit Demande faible | Réduction des stocks Planification simplifiée Offre large de produits |
La différenciation retardée
La différenciation retardée (“postponement” en anglais) est une forme d’assemblage à la commande. C’est-à-dire le fait de repousser le plus en aval possible les opérations de finition et de personnalisation du produit (“assemble to order”).
Le but est de mutualiser un maximum de stocks de produits semi-finis et ensuite, le plus tard possible, de proposer la personnalisation correspondante à la demande client.
Les clients souhaitent avoir des produits de plus en plus personnalisés, exemple DS avec des modèles DS3 personnalisables qui obligent le groupe à disposer d’un outil de production important, davantage de calage et de temps de changement d’outillage (SMED à voir cours Production).
Par conséquent, l’objectif sera de produire le plus longtemps en « série » avec le prévisionnel, “make to stock”, puis de différencier à la demande, “make to order”.
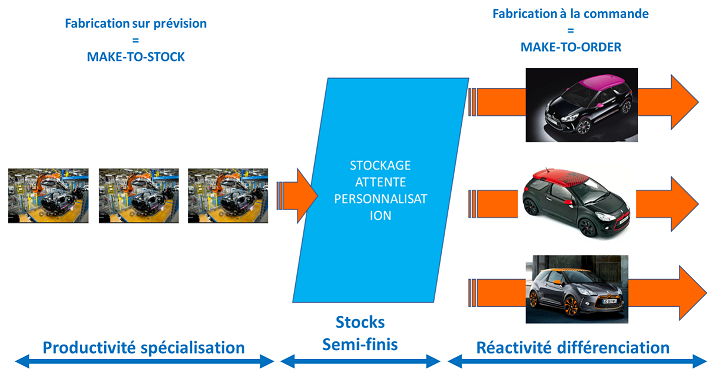
La différenciation retardée présente plusieurs avantages, directement impactants sur les coûts de l’entreprise :
la réduction des stocks ;
la réduction des coûts de production ;
la réduction des risques ;
l’augmentation de la satisfaction client.
Les différents types de différenciation :
différenciation d’étiquetage ;
différenciation de packaging ;
différenciation d’assemblage ;
différenciation de fabrication.
Pour répondre aux différentes stratégies :
différenciation au stade de la distribution ;
différenciation perceptuelle (même produit, services différents) ;
différenciation au stade de la production (standardisation vs technologie).
Management des capacités et planification des charges
La supply chain, c’est aussi être capable de fournir, donc de produire ou assembler les produits attendus par nos clients, par le marché.
Être capable, c’est quoi ?
Nous entendons par être capable, la faculté d’une organisation, d’un collaborateur, d’une machine, d’une entreprise, à produire une quantité donnée sur une période définie :
la capacité théorique correspond à la capacité maximale d’une ressource, sans prendre en compte les irritants (arrêts, pannes, casses, etc.) ;
la capacité démontrée ou établie est quand à elle la capacité issue d’expériences, c’est-à-dire constatée à l’issue d’une quantité produite sur une période donnée ;
la capacité nominale correspond à la capacité calculée à partir de données, comme l’efficience, le nombre d’heures planifiées… que l’on calcule via l’une des formules suivantes.
Nbre d’heures d’ouvertures X Taux de rendement X Taux utilisation
Capacité Théorique X Coefficient d’efficience
La capacité disponible, pour désigner la quantité envisageable pouvant être produite par une ressource pendant une période donnée.
La capacité requise, pour désigner la capacité d’une ressource nécessaire pour produire une quantité d’unités donnée, toujours sur une période donnée. Cette capacité peut varier en fonction du temps d’ouverture du poste de charge, du rendement de l’outil de production, du nombre de mes opérateurs, etc.