La distribution physique
La distribution physique est aujourd’hui l’apanage des « entreprises industrielles de la supply chain ». Ce qui signifie aussi que les rôles de chacune des parties, entre demandeur et distributeur, ont évolué en même temps que l’évolution même du transport.
Les grandes évolutions peuvent être représentées ainsi :
années 1960 : chargeurs - transporteurs ;
années 1970 : chargeurs - entrepreneurs du transport ;
années 1980 : chargeurs - entrepreneurs de la logistique ;
années 1990 : chargeurs - industriels de la logistique ;
années 2000 : chargeurs - industriels de la supply chain
Ce qui veut dire aussi que l’évolution est passée de « moi je suis le client et toi mon fournisseur » uà ne relation commune chargeur-prestataire plutôt collaborative que directive, voire conflictuelle.
Le transport
Le transport constitue un élément important dans le coût de l’entreprise industrielle, soit entre 3 et 5 % du chiffre d’affaires. Le transport routier de marchandise occasionne +/- 10 % des émissions de CO2 et représente +/- 85 % des flux de transport.
La distribution physique des produits nécessite la mise en place d’un processus de transport. Le transport est rarement sous la responsabilité d’un seul département, mais plutôt une combinaison de plusieurs départements, chacun acteur pour un seul objectif : satisfaire notre client.
Exemple de processus de gestion de transport :
Planifier le transport |
|
Préparer les ordres de transport |
|
Gérer la relation fournisseur |
|
Clôturer les ordres de transport |
|
Piloter la performance du transport |
|
Transporter est un élément majeur de la supply chain que l’on peut optimiser dès notre approche de stockage.
Le magasinage est et reste aussi un élément essentiel dans la distribution, y compris avec le déploiement du flux tendu. Il est donc impératif, pour optimiser la distribution des produits, de bien définir la solution d’optimisation des coûts.
Soit je distribue à partir d’un seul et unique entrepôt, donc j’optimise mes coûts de stock et d’entrepôt (un seul), mais en contrepartie contribue à augmenter mes coût de transport, ou bien j’opte pour une autre solution, multiplier les magasins de distribution avec un possible impact sur les coûts de stockage. Alors, quelle option dois-je prendre ?
Zoom sur le DRP
La gestion de production utilise un outil vu précédemment, appelé MRP - MRP2, tandis que la gestion de la distribution s’oriente sur le DRP, « Distribution Resource Planning ».
Il s’agit de disposer d’un outil simple et efficace de prévision, en tenant compte chaque fois que possible des commandes fermes du PDP. Le DRP est donc une extension du MRP à destination de la gestion de la distribution.
C’est pourquoi une distribution de produits de consommation courante (exemple des supermarchés) est organisée sur le même modèle que l’organisation industrielle, et nous pouvons différencier deux cas :
Le système Poussé : cas du DRP pour lequel :
le système est centralisé, les stocks de l’ensemble des magasins sont connus et gérés par un système comme le MRP ;
le système calcule les besoins en réapprovisionnement des sous-magasins, semblable aux règles de calcul du MRP ;
le système attribue les stocks disponibles aux sous-magasins.
Le système tiré du type Kanban, pour lequel :
le système est décentralisé ;
le sous-magasin est acteur de ses commandes en amont ;
le produit est tiré par l’aval, pour en déterminer l’importance des stocks.
Si notre acteur fabricant utilise le MRP et notre distributeur le DRP, chacun de manière optimale, il est indispensable que nos deux entités s’entendent pour intégrer leur système, en vue d’intégrer le DRP au MRP du fabricant pour que ce dernier ait une excellente vision des stocks de ses produits finis, quel que soit l’endroit où ils sont présents.
Une bonne intégration des deux systèmes permet de réaliser des économies globales de coûts logistiques et une diminution significative du risque pour l’ensemble des parties prenantes (transport, lots de fabrication, fabrication à l’unité consommateur, ruptures, surstocks, etc.).
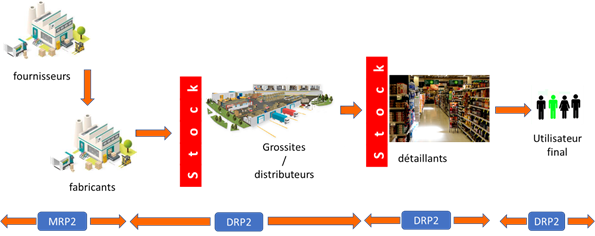
Pour terminer, le DRP permet donc une vision de la situation et du niveau de stock à l’endroit où il se trouve, et le niveau de réapprovisionnement demandé par le point de vente en tenant compte du degré de service, de la taille de lot, du coût et du moyen de transport souhaité.
Cette pratique est souvent associée à la relation de partenariat, que l’on nomme aussi Supply Chain Management.
Centre de distribution et Cross Docking
Les plateformes de distribution Hub ou Cross Docking sont des sites où l’on reçoit des produits ; ces derniers sont réexpédiés dans un délai très court. Sur ces sites, la marchandise ne fait que transiter et toute opération de reconditionnement est quasi-nulle, on préférera l’expédier vers un autre site dédié.
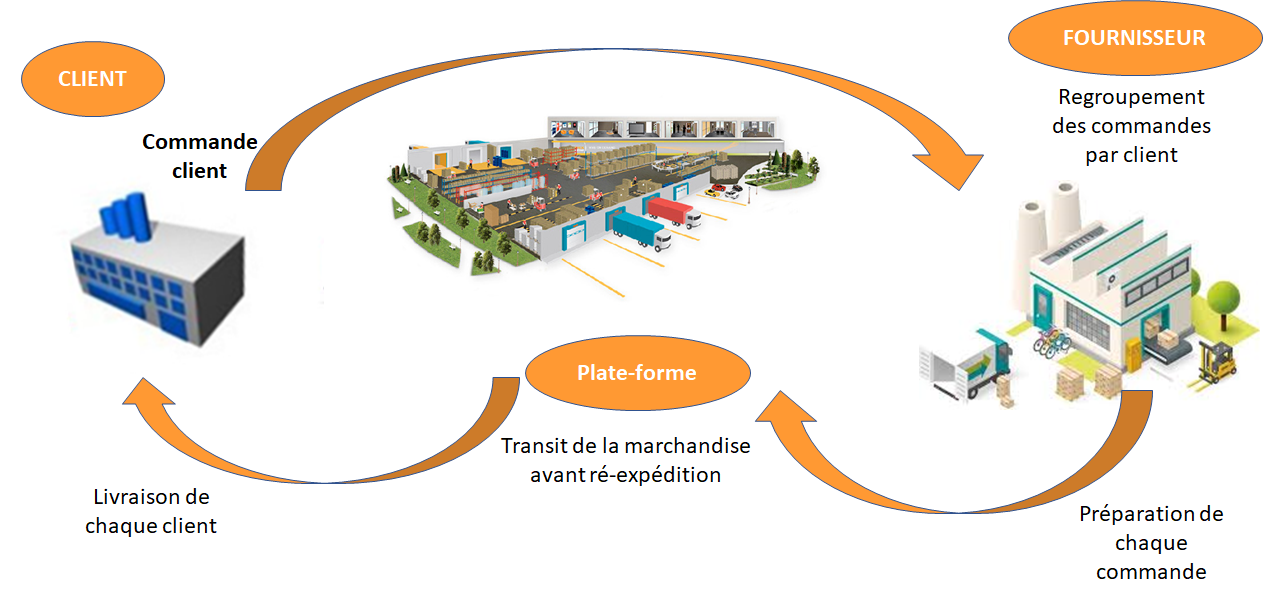
Ces Cross Docking offrent une réelle opportunité de massification des flux provenant de multiples fournisseurs, quelles que soient les distances, pour ensuite être acheminés vers une multitude de clients. Cette solution présente l’avantage d’optimiser la chaîne logistique et de maîtriser les flux à l’échelle internationale.
Optimisez l’entrepôt
Un entrepôt est une zone de stockage où les produits sont entreposés un certain temps avant d’être consommés en l’état ou transformés. L’entrepôt offre la possibilité de réguler les besoins en marchandises d’une entité de distribution ou de production, en fonction des différentes contraintes des parties prenantes. La contrepartie pour l’entrepôt, c’est qu’il est nécessaire de mettre en place une organisation orientée vers le picking.
Picking
Le picking (ou “cueillette”, en anglais) en logistique, c’est l’action d’aller chercher les produits dans le stock pour les regrouper à l’endroit où on va les utiliser, les conditionner, les assembler, etc.
Le principe du picking est de prélever des colis à l’unité ou bien des UVC (unité de vente consommateur), inférieures à un colis, soit des boîtes, des sachets, comme par exemple la brosse à dent que j’achète chez le pharmacien.
Le picking nécessite des rayonnages situés près du sol pour un accès rapide des préparateurs. Par contre, pour les palettes complètes ou semi-complètes, on parlera de réserve. Pour les produits à peu de picking mais plutôt en palettes complètes, il est envisagé de constituer une zone « fast movers » (produits à forte rotation) au sol, sans racks, contenant uniquement des palettes complètes prêtes à être ramenées sur les quais d’expédition.
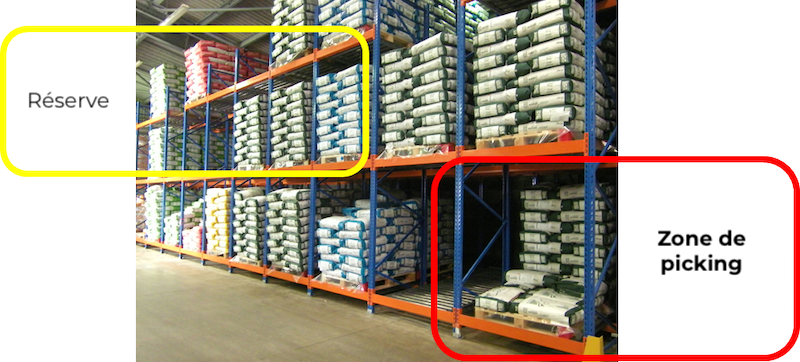
Il s’agit du flux intégrant réserve et picking où sont stockés des produits qui attendent d’être consommés.
Le processus peut être décomposé de la manière suivante :
Réception et mise en stock de la marchandise (palettes).
Réalimentation pour que le livreur ne soit jamais en rupture de produit, soit de manière continue, soit à fréquence fixe (une fois par jour ouvré).
Livraison des composants (via un petit train).
Processus d’évacuation (déchets, emballages, etc.).
Chargement des véhicules de produits finis.
Le choix d’implantation, le type d’entreposage est déterminé par de multiples outils et méthodes d’optimisation de l’entrepôt. On utilisera une analyse ABC et une étude d’implantation géographique. L’utilisation de ces deux outils nous permettra de localiser stratégiquement les différents articles en privilégiant la hauteur pour les articles à faible rotation, et le sol et les emplacements proches du quai d’expédition pour les articles à forte rotation. Pour ce faire, je propose de prendre connaissance de l’outil suivant : la méthode ABC.
La méthode ABC
La méthode ABC est un outil décisionnel, dérivé de la loi de Pareto (80/20), qui stipule qu’en moyenne « 20 % des causes sont à l’origine de 80 % des effets ».
Cette méthode propose de diviser un phénomène en trois classes :
classe A : les items accumulant 80 % de l’effet observé ;
classe B : les items accumulant les 15 % suivants ;
classe C : les items accumulant les 5 % restants.
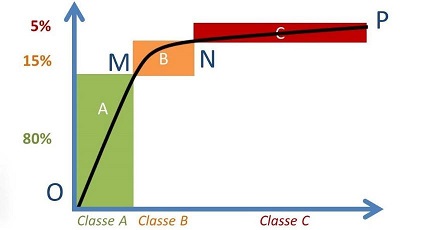
Méthodologie :
Faire une extraction des stocks avec les volumes de vente, et en déduire la rotation par article.
Classer les produits par ordre décroissant de valeur de stock.
Élaborer le Pareto :
Valoriser en % le poids de chaque produit sur le stock global.
Calculer la valeur de stock cumulé.
Construire le diagramme.
Affecter les classes ABC aux articles en fonction de leur rang. Puis étudier les articles de classe A avec de mauvaises rotations.
Pourquoi utiliser la méthode ABC ?
C’est un outil décisionnel utilisé pour la gestion des stocks par la catégorisation des produits ;
si les améliorations apportées à cette classe ne suffisent pas, l’analyse de la classe B sera un excellent complément, mais la classe C n’apportera que peu de résultats pour beaucoup d’efforts (60 % des items pour 5 % d’effets) ;
la perfection coûte cher, car au-delà d’un certain seuil (coude de la courbe), le coût supplémentaire pour améliorer la situation est prohibitif.
FIFO-LIFO
Il s’agit de méthodes de gestion et de valorisation des stocks selon l’ordre d’entrée des lots, en tenant compte de de leur nature :
FIFO = “First In - First Out” ou premier entré – premier sorti (PEPS) : chaque entrée en stock est valorisée à la valeur du lot le plus ancien ;
LIFO = “Last In – First Out” ou dernier entré – premier sorti (DEPS) : les sorties sont évaluées au coût du bien le plus récent.
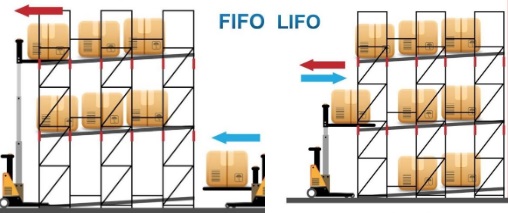
| Avantages | Inconvénients |
FIFO | Minimise les pertes dues d’obsolescence, bon pour les produits périssables (alimentaires ou de haute technologie). C’est une gestion préconisée par le plan comptable général (PCG), reconnu par les administrations comptables. | Répercute avec retard les variations de prix de l’achat. En cas d’inflation, les résultats d’exploitation sont surévalués et la base des résultats est constatée tardivement. |
LIFO | Adapté à certaines marchandises, dont la valeur augmente avec la durée de stockage. S’arrime à la variation des prix du marché. En période d’inflation, elle permet de lisser les pertes en appliquant les prix actuels. | N’est pas reconnu par les administrations fiscales ni le PCG. |
En résumé
À présent, vous êtes en mesure de gérer votre supply chain ! En effet, vous avez abordé le management de la production, la planification de la demande, la satisfaction de la demande client, la gestion des approvisionnement et la distribution via les entrepôts. Vous disposez à ce stade des outils pour une optimisation de la gestion des stocks. Je vous invite à poursuivre dans l’industrie 4.0, l’industrie du futur, où nous abordons les innovations de demain, les systèmes d’information, l’industrialisation des entrepôts, les Cobots, les AGV, les drones d’inventaire autonomes, mais aussi l’intelligence artificielle et ses applications analytiques avancées. À tout de suite dans la prochaine partie !