Dans la partie précédente, vous avez amélioré un processus de fabrication relativement simple. Après une première phase d'observation, vous avez pu tirer des conclusions sur les dysfonctionnements rencontrés par cette entreprise.
Pour cette deuxième partie, je vous propose d'aller plus loin, en analysant cette fois-ci un vrai processus industriel. Vous allez vite vous rendre compte qu'il est alors nécessaire de s'aider d'un outil pour dessiner ce processus, pour ensuite l'analyser et l'améliorer.
Qu’est-ce qu’une chaîne de valeur ?
Plus que le processus de fabrication, nous souhaitons analyser l'ensemble de la chaîne de valeur de cette entreprise.
La chaîne de valeur se compose de toutes les informations suivantes :
Matières premières : quantité ? Valeur ? Durée moyenne de stockage ? Fréquence d'approvisionnement ?
Produits semi-finis : quantité en stock ? Quantité d'en-cours de fabrication à chaque activité ?
Produits finis : quantité en stock ? Fréquence d'expéditions ?
Flux d'informations : y a t-il un ERP ? Délai des commandes fermes ? Amplitude des prévisions des commandes ? Lancement des ordres de fabrication ?
Employés et horaires : combien d'employés ? Quelle est la polyvalence ? Horaires et jours d'ouverture ? Nombre d'équipes ? Heures supplémentaires ?
Équipements et capacité : quelle est la capacité des équipements ? Quelle est la cadence de chaque machine ? Y a t-il des opérations manuelles ?
Ingénierie : quel est le time to market/temps de mise à disposition du nouveau produit sur le marché ? La fabrication du produit nécessite-t-elle de solliciter le bureau d'études ?
Si maintenant, je vous demande de récolter et de synthétiser toutes ces données de production afin d'analyser l'ensemble de cette chaîne de valeur, vous risquez de commencer à pâlir. 😱
Heureusement, il existe un outil très puissant : la Value Stream Mapping (VSM), ou cartographie de la chaîne de valeur.
« Partout où existe un produit pour le client, il y a un flux de valeur.
La difficulté réside dans notre capacité à la voir ! »
James Womack
Pourquoi cartographier ?
La Value Stream Mapping est une cartographie descriptive des flux, qui dans l’idéal couvre la Supply Chain entière (de l’approvisionnement des matières à la livraison au client consommateur). L’objectif est de définir une cartographie de l’état initial, de la critiquer et de créer une cartographie de l’état futur. Elle sert à :
visualiser le flux de création de valeur dans le processus ;
statuer sur le processus et montrer le ratio entre la valeur ajoutée et la non-valeur ajoutée ; donc identifier les sources de gaspillage et de non-performance ;
détailler les temps de cycle et les rendements ;
montrer l’interaction entre les 7 types de flux (matières premières, produits semi-finis, produits finis, informations, hommes, équipements, ingénierie).
La VSM est un outil essentiel qui nous permet de mettre en évidence des goulots d’étranglement, d'identifier comment livrer plus rapidement nos clients ou réduire les en-cours, par exemple.
Le terme de chaîne est bien choisi, car comme on dit : une chaîne est aussi solide que son maillon le plus faible ! Un seul maillon défaillant dans notre chaîne de valeur, et c'est toute l'entreprise qui peut être en péril.
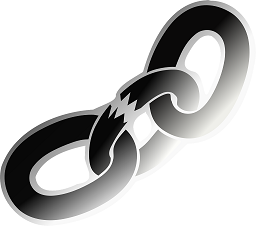
L'intérêt de la VSM est donc d'étudier le flux complet et non un seul maillon, d'autant que c'est le seul outil de cartographie qui lie les flux d'informations et les flux physiques.
Cet outil permet de "faire sauter aux yeux" les causes de gaspillages et lie tous les concepts du Lean. Grâce à lui, vous serez capable de rédiger une véritable Road Map (feuille de route) pour les années à venir, en amenant une cohérence à votre démarche.
Les étapes de la démarche VSM
La démarche d'un projet VSM est relativement simple, elle repose sur 4 étapes :
Identification de la famille de produits à cartographier. Il est compliqué de refondre la globalité de l'entreprise. Ainsi, il faut cibler le produit/process le plus représentatif en termes de volume, et donc souvent en termes de chiffre d'affaires. On peut encore retenir une famille de produits/process sur laquelle on rencontre le plus de dysfonctionnements.
Cartographie de l'état actuel. On réalise un schéma, qui est une photo à un instant t du fonctionnement de l'entreprise.
Cartographie cible. Aussi appelée le Value Stream Design. C'est la vision de ce que doit être le fonctionnement futur de l'entreprise. Même si vous pouvez donner l'impression de rêver. Il faut viser la situation optimale.
Mise en oeuvre du plan de transformation. Élaboration du plan d'action pour transformer l'entreprise.
Apprenez à interpréter une cartographie de la chaîne de valeur
Avant de vous lancer dans la réalisation d'une cartographie, je vous propose d'apprendre à lire une VSM. Vous allez voir, de prime abord, cela peut faire peur, mais en fait c'est très simple !
Décomposition d'une VSM
Sans l'examiner pour le moment dans le détail, voici la cartographie de l'état initial de l'entreprise que nous allons étudier dans le chapitre suivant. Patience, nous la construirons ensemble pas à pas dans le chapitre suivant.
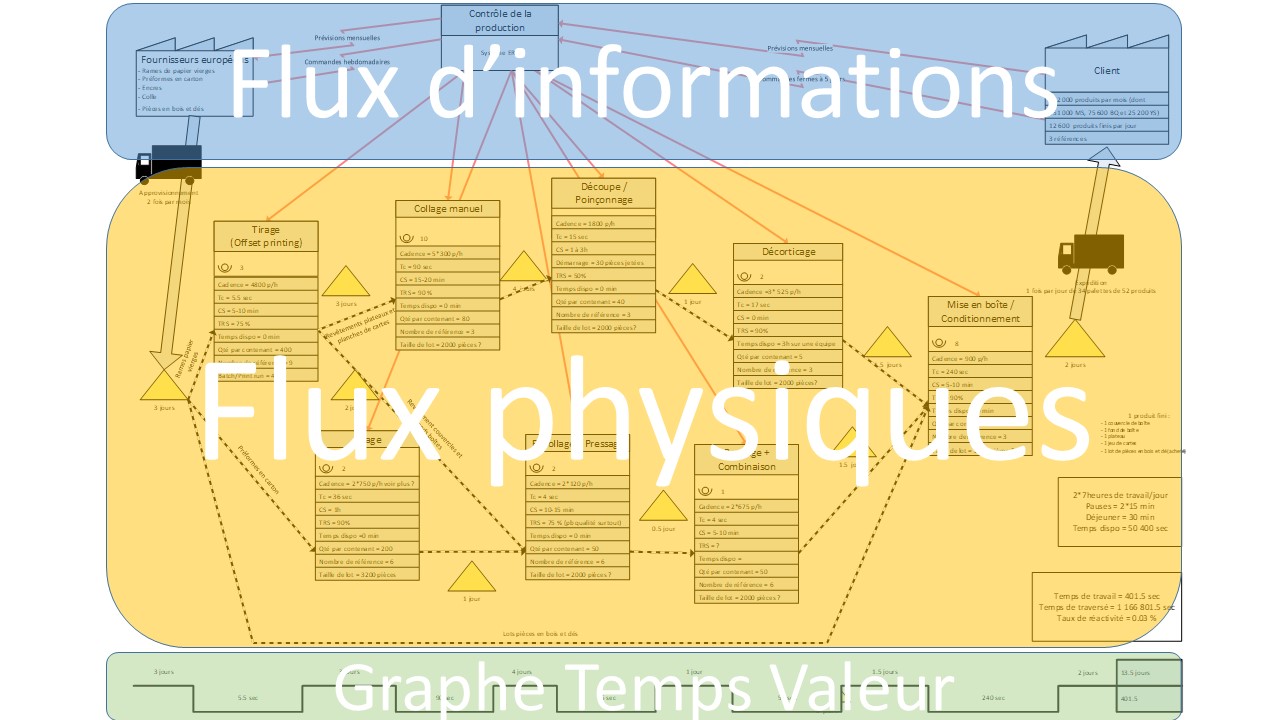
La VSM utilise des pictogrammes simples. Une fois que vous les connaissez, ils permettent :
de lire aisément la carte ;
de comprendre le processus cartographié ;
d'identifier immédiatement des points à améliorer.
La VSM est établie en remontant le flux produit. Il y a trois zones distinctes dans cette cartographie :
la zone centrale est la plus complète. Elle fait apparaître les principales étapes du processus de fabrication et l'ensemble des flux physiques ;
dans la partie supérieure, vous trouvez les flux d'informations. Ils montrent les liens entre les processus de fabrication, et donc les interactions entre les différents maillons de la chaîne ;
enfin, la partie inférieure montre le graphe temps/valeur, encore appelé ligne du temps (Timeline, en anglais). Il fait apparaître les temps de valeur ajoutée et les temps de non-valeur ajoutée.
Le formalisme
La VSM nécessite de connaître un certain nombre de symboles pour savoir l’interpréter. Heureusement, ils sont peu nombreux et relativement explicites.
On trouve trois catégories de symboles, correspondant aux zones de la cartographie :
symboles de flux matières ;
symboles de flux d'informations ;
symboles du graphe temps/valeur.
Détaillons les symboles les plus utilisés pour chaque catégorie.
Symboles flux matières
Les trois essentiels :
par convention, nous ferons apparaître les fournisseurs en haut à gauche et les clients en haut à droite, grâce au symbole ci-dessous ;
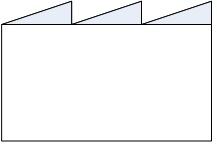
ensuite, nous ferons apparaître les cases processus avec leurs données associées (tâches exécutées, nombre d'opérateurs, temps de cycles, changements de série, attentes, tailles de lot, performance et rendements, qualité, ressource, etc.) ;
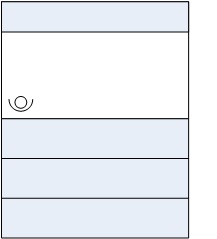
Le dernier symbole de base est celui des dépôts ou points de stockage (pour connaître la quantité de stocks et d'en-cours) :
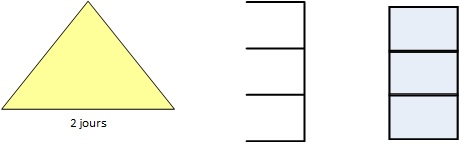
On peut préciser qu'un supermarché n'a rien à voir ici avec la supérette du coin. Ce type de stock reprend cette appellation pour faire le parallèle avec le réapprovisionnement des rayons. En effet, un stock supermarché, dans une entreprise, permet au poste qui l'alimente d'ajuster sa production en fonction de la consommation du poste aval.
Les symboles pour les flux physiques de matières
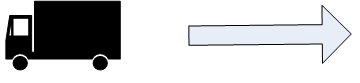

Ces trois derniers symboles méritent une explication :
comme nous l'avons vu lors de la première simulation de fabrication de sushis, il est fréquent de voir qu'un poste fournit un autre poste en flux poussé. C'est-à-dire qu'il va pousser le travail qu’il fait à la personne suivante, tant qu'il a de la matière pour travailler ;
nous avons également abordé la notion de FIFO : c'est donc ici une représentation d'un flux qui respecte le concept de "premier entré, premier sorti". Pour en savoir plus : Sorties de stocks : FIFO, LIFO & Co ;
enfin, le flux tiré physique, ou retrait de marchandises, est le déplacement des marchandises d'un supermarché vers des processus en aval.
Symboles flux d'information
La force de la VSM, par rapport à d'autres cartographies, est de faire apparaître les flux d'informations et leurs interactions avec les flux physiques.
En effet, ce qui va piloter le flux physique est avant tout un flux d'informations : c'est le client qui valide une commande (ce que l'on appelle une commande ferme). Les commerciaux peuvent également fournir un prévisionnel de ventes pour anticiper la production. Une fois cette information reçue, l'entreprise va elle-même passer des commandes à ses fournisseurs et/ou un prévisionnel de commandes, pour lancer l'approvisionnement de la matière première.
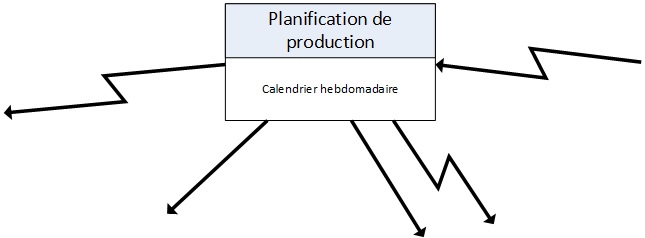
Ainsi, les 3 symboles principaux de flux d'information sont :
la représentation du calendrier de travail (service Planification) ;
les flux sur papier avec les flèches pleines ;
les flux électroniques avec les flèches éclairs.
Les autres symboles des flux d'informations sont liés à des outils pour tirer les flux et tendre les flux. Patience, encore deux chapitres et vous pourrez jouer avec ces concepts. Voici tout de même la représentation de ces symboles :
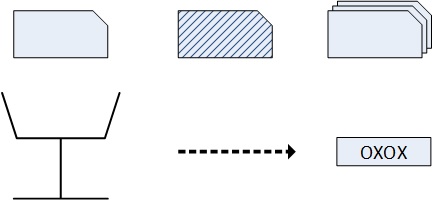
Tout ce formalisme est universel. Il est donc compréhensible par tous, même dans un cadre international.
Symboles graphes temps/valeur :
Voici les derniers symboles. Ils permettent de visualiser puis de calculer le ratio entre le temps à apporter de la valeur ajoutée et le temps total de traversé de l'ensemble de l'usine.
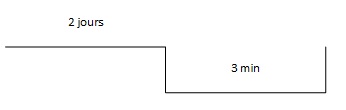
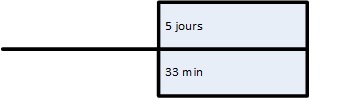
Ce dernier symbole fait apparaître le temps total de traversé (en haut) et le temps total de production, donc de valeur ajoutée (en bas). On calculera alors un rapport appelé taux de réactivité, ou taux de flexibilité.
Dans notre exemple,
5 jours = 7 200 min ;
taux de réactivité = (33 min / 7 200 min) * 100 = 0.46 %.
Cela peut paraître faible, mais c'est un résultat proche de ce que l'on peut retrouver dans beaucoup d'entreprises. L'objectif est donc d'augmenter cet indicateur, notamment en baissant les temps de non-valeur ajoutée.
Si vous souhaitez dessiner une VSM sur ordinateur, il existe plusieurs logiciels dédiés. Pour ma part, mes VSM sont dessinées sous Microsoft Visio. Vous pouvez utiliser également une plateforme comme LucidChart.
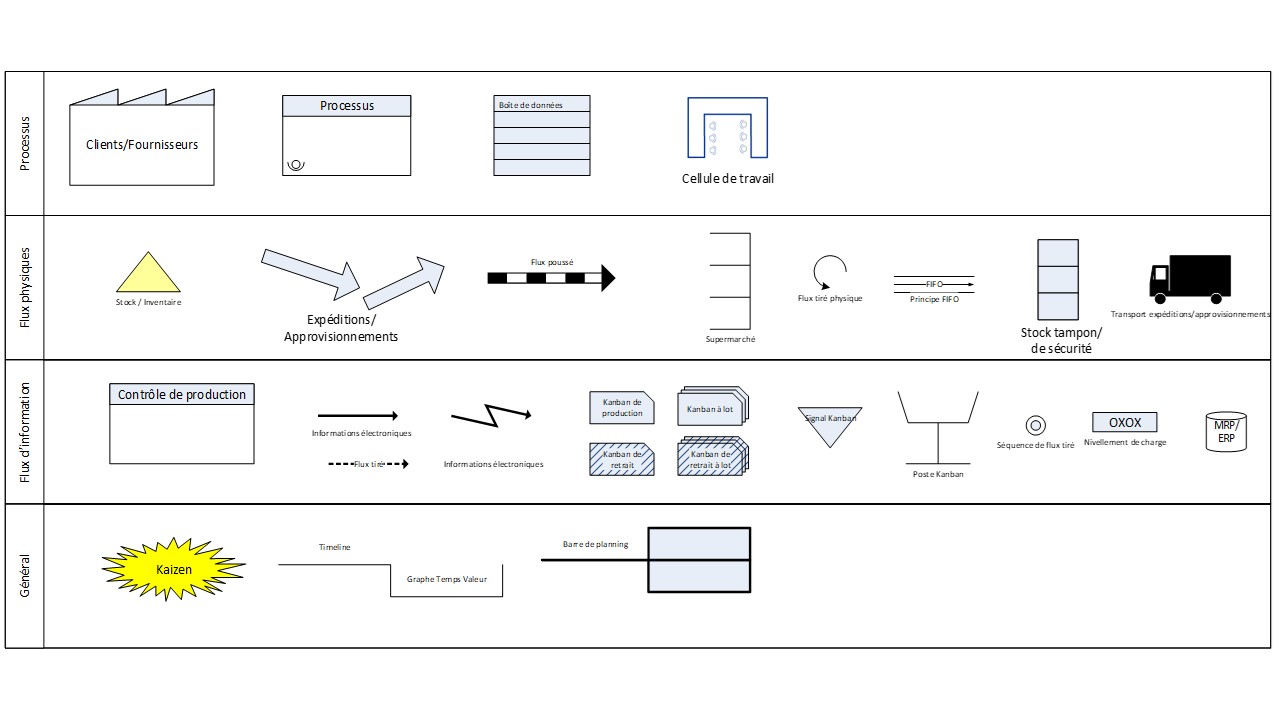
Nous en avons fini avec les symboles. Cela peut paraître complexe, mais pas de panique, le chapitre suivant est destiné à vous permettre de vous approprier pas à pas cette représentation. Vous allez réaliser votre première cartographie VSM ! :soleil: