Pour terminer ce cours, j'aimerais que l'on prenne le temps de parler de la place de l'humain dans nos démarches de transformation Lean, et de transformation numérique.
En effet, nous avons abordé les aspects :
techniques et technologiques ;
organisationnels et méthodologiques.
Il est temps de prendre un peu de recul sur les aspects humains, sociaux.
En effet, la compréhension des outils et méthodes vus dans ce cours est relativement accessible et souvent pleine de bon sens. La difficulté principale sera d'accompagner le changement.
Accompagnez le changement
En effet, la réussite de votre démarche repose sur ces équipes que vous allez accompagner, pendant la transformation certes, mais aussi dans le quotidien. Il faut rassurer, montrer que vous savez où vous allez, et partager l'intérêt de faire évoluer l'entreprise.
Vous devrez savoir identifier et détecter les éventuelles réticences, et au contraire saisir les opportunités. À chaque projet, je vous invite à faire le diagnostic des impacts d'un changement, et d'établir en conséquence une stratégie du changement pour créer les conditions d'appropriation de la démarche. On attendra de vous d'être capable de convaincre et de fédérer.
J'irai même plus loin. Notre monde change vite, l'industrie n'y échappe pas. Vous devez donc inscrire le changement dans une véritable dynamique d'amélioration continue !
Pour cela, vous et vos équipes devront apprendre à apprendre. Je m'explique. Il faut impérativement faire le deuil de l'idée que la nouvelle organisation que l'on vient de mettre en place, sera la bonne pour les 10 ans à venir. Il faut constamment remettre en cause les pratiques. On parle même de capacité à désapprendre pour entrer dans une phase de réapprentissage.
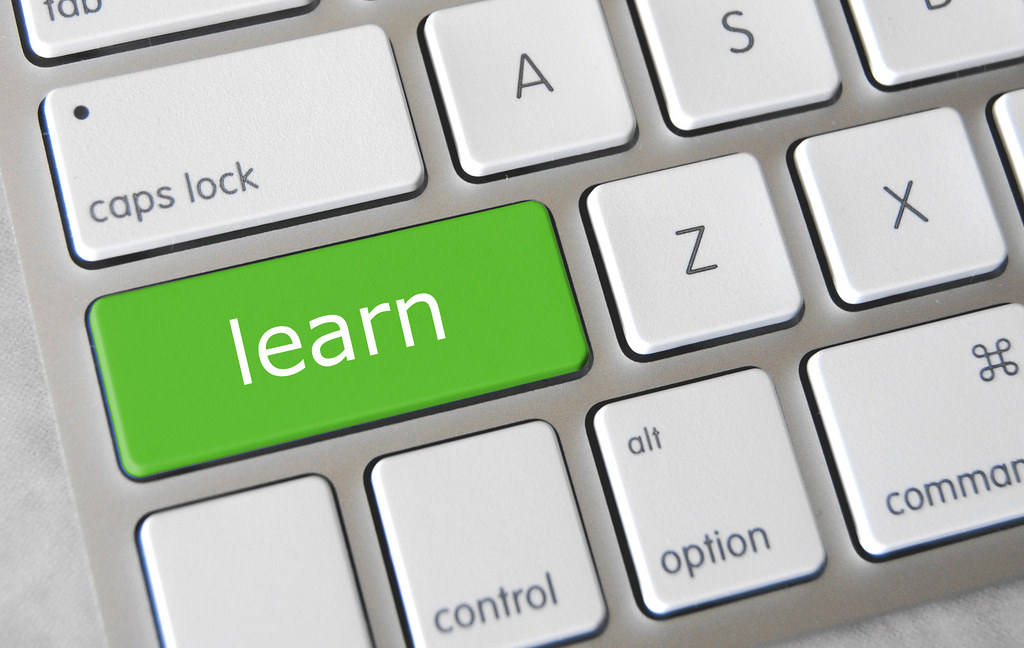
Pour cela, il faudra aussi maintenir et faire évoluer le champs de compétences de ses équipes.
Vous pourrez ainsi identifier les compétences et expertises de chacun ; et, toujours dans un esprit de décloisonnement, construire un réseau d'expertises et animer une communauté de pratiques, afin de partager entre pairs.
Organisation responsabilisante
Pour aller plus loin que l'innovation participative, certaines entreprises vont jusqu'à se poser la question de revoir leur organisation pour accélérer et faciliter les prises de décisions.
On pourrait imaginer que ce type d'initiative n'a sa place que dans une start-up, mais pas seulement !
Regardez par exemple le programme OR pour organisation responsabilisante chez Michelin.
"Un de nos principes est de donner la responsabilité à celui qui accomplit la tâche car il sait beaucoup de choses sur la question et cela lui révèle souvent des capacités dont il ne se doutait pas et qui le font avancer."
Édouard Michelin
L'organisation responsabilisante repose sur des concepts simples :
la confiance ;
l'autonomie ;
l'autocontrôle ;
et la transparence.
Si le sujet vous intéresse voici le chapitre d'un cours très intéressant qui en parle. L'organisation hiérarchique d'aujourd'hui, sans aller totalement vers une organisation apprenante, va devoir se remettre en question et être davantage collaborative, que l'on soit dans des grands groupes, ou dans des PME.
Les impacts d'une transformation Lean
Si vous avez fait quelques recherches sur Internet, échangé avec des industriels, ou encore vu certains reportages télé, vous avez peut-être entendu dire que le Lean ne véhicule pas toujours une image positive.
En effet, il arrive malheureusement que le Lean ne soit appliqué que dans un souci de productivité et de rentabilité, sans se poser les questions des impacts pour les hommes.
Il faut en effet être vigilant, l'optimisation à outrance peut s'avérer néfaste. J'aimerais vous faire part de l'une de mes expériences. Nous avions réalisé une étude des déplacements des opérateurs via un diagramme spaghetti.
Celui-ci nous a permis de comprendre, d'analyser et donc de réduire les déplacements des opérateurs. Notamment, nous avions permis à un conducteur de ligne de limiter ses déplacements autour de la machine en cours de production, ce qui lui faisait faire un sacré nombre de kilomètres, et également d'éviter d'aller chercher toutes 2 heures un nouveau rouleau d'étiquettes pour les emballages. Donc sur le papier, tout le monde est gagnant : l'entreprise gagne quelques minutes de production et l'opérateur aura moins de kilomètres à parcourir dans la journée.
Oui, mais ! Notre conducteur de ligne était en effet satisfait de ne plus avoir à tourner autour de sa machine pour effectuer des vérifications et lancer des commandes sur celle-ci. En revanche, l'aller-retour de quelques minutes pour aller chercher un nouveau rouleau d'étiquette, il y tenait. Pourquoi ? Parce qu'il était très isolé autour de sa machine et que c'était le moment qui lui permettait de s'aérer l'esprit et de croiser d'autres visages.
Cet exemple permet juste de vous montrer qu'il ne faut pas chercher l'optimisation à l'excès, et d'échanger avec les personnes du terrain pour savoir aussi de quoi ils ont besoin. Les calculs et les cartographies ne doivent pas effacer le BSH : le bon sens humain. :D
Dans notre cas, la machine pouvait continuer de tourner pendant les quelques minutes d'absence de l'opérateur. Il aurait donc été dommage de dégrader son bien-être. Il a pu continuer de s'occuper de ce réapprovisionnement.
Quels sont les impacts d'une transformation numérique ?
L'industrie du futur va certes engendrer des mutations technologiques, mais dans le même temps, des mutations organisationnelles et sociales. Se pose alors la question de la place de l'homme dans cette industrie du futur.
Se pose en effet la question de la relation de l'homme au travail dans l'industrie du futur. En effet, l'organisation du travail et les méthodes de management, nous l'avons vu, vont être bouleversées. Le risque majeur de l’industrie du futur est de ne promouvoir que des projets « techno-centrés », et donc de ne pas anticiper ces bouleversements.
Par exemple, il faudra être vigilant à ne pas adapter l'humain au travail, mais bien le travail à l'humain. Et il est nécessaire d’anticiper les questions de santé au travail quant à l’introduction de nouvelles technologies. Même jusqu'à s'interroger sur la relation homme-machine.
L'opérateur équipé d'un casque de réalité virtuelle ou de réalité augmentée, se retrouve alors cloisonné, coupé du reste de l'équipe et replié sur lui-même.
Le risque est le même avec la cobotique (ou robotique collaborative). Il sera primordial de réaliser une analyse de risques avant l'intégration d'un cobot. Celui-ci permettra d'améliorer les lignes de production, en travaillant sur l'ergonomie des postes de travail. On va pouvoir réduire les TMS, diminuer les déplacements de l'opérateur. Le robot n'étant pas enfermé dans une cage, pourra être facilement déplacé en fonction des besoins, pour gagner en flexibilité. Mais il faudra s'assurer que l'opérateur n'y voie pas une pâle copie de son savoir-faire et de sa dextérité. Il pourrait même craindre de se voir comparé à cette machine qui le surpasse en précision, en répétabilité et en endurance. Voici un article qui traite du sujet.
Il faut lui démontrer que c'est la collaboration des deux qui va permettre de gagner en qualité et en régularité de production des pièces.
Heureusement, les normes évoluent aussi dans ce sens, pour donner un cadre à l'installation de ces nouvelles technologies.
J'aimerais terminer avec cette citation :
"Pourquoi ne pas faciliter le travail et le rendre plus intéressant pour que les gens ne transpirent plus ? Le style Toyota ne cherche pas à créer des résultats en travaillant dur. C’est un système qui ne fixe pas de limites à la créativité des gens. Les employés ne vont pas chez Toyota pour travailler, ils y vont pour penser."
Taichi Ohno
L'amélioration continue est une discipline passionnante, sans fin. C'est très gratifiant de pouvoir aider les utilisateurs, les opérateurs et les managers à travailler mieux et à se sentir mieux dans leur travail.
J'espère vous avoir transmis ma passion et vous avoir donné envie de réaliser un premier chantier. Et n'oubliez pas : OPTA ! On Peut Toujours Améliorer !